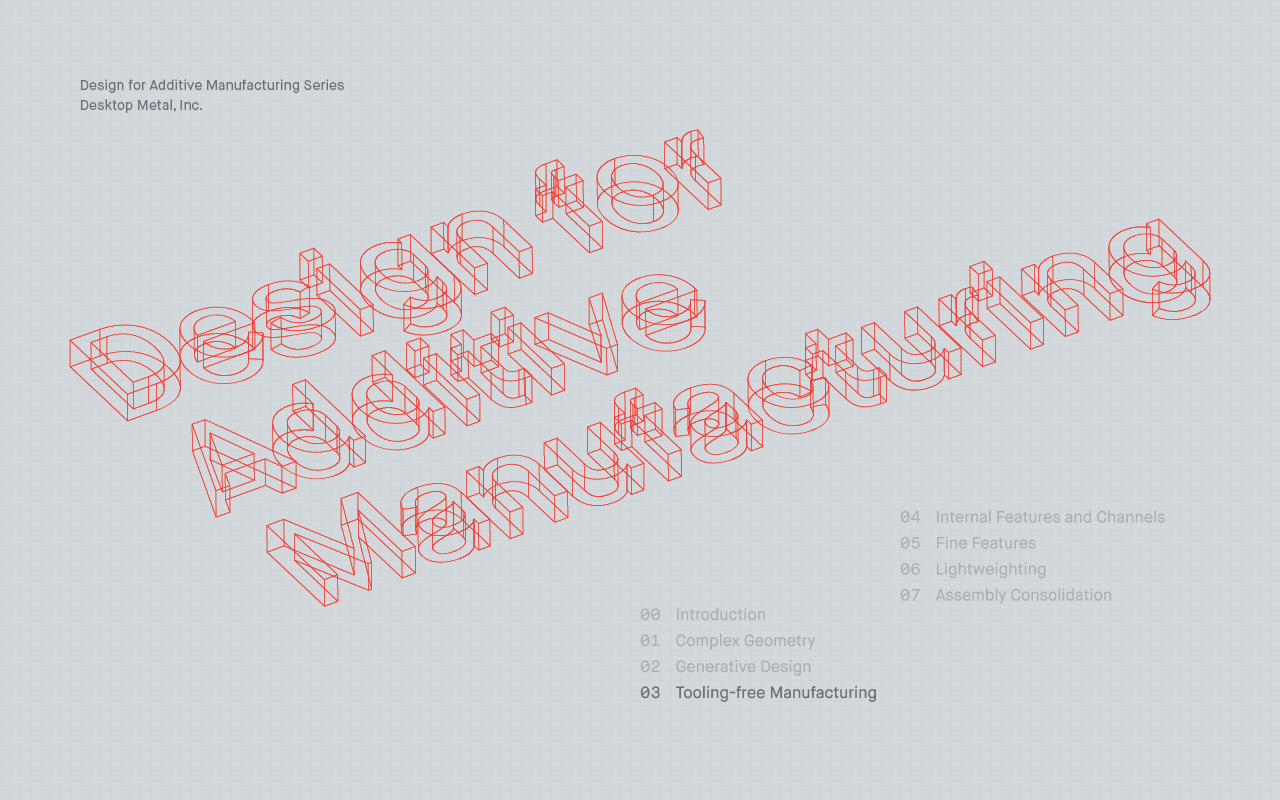
Design for Additive Manufacturing: Internal Features and Channels
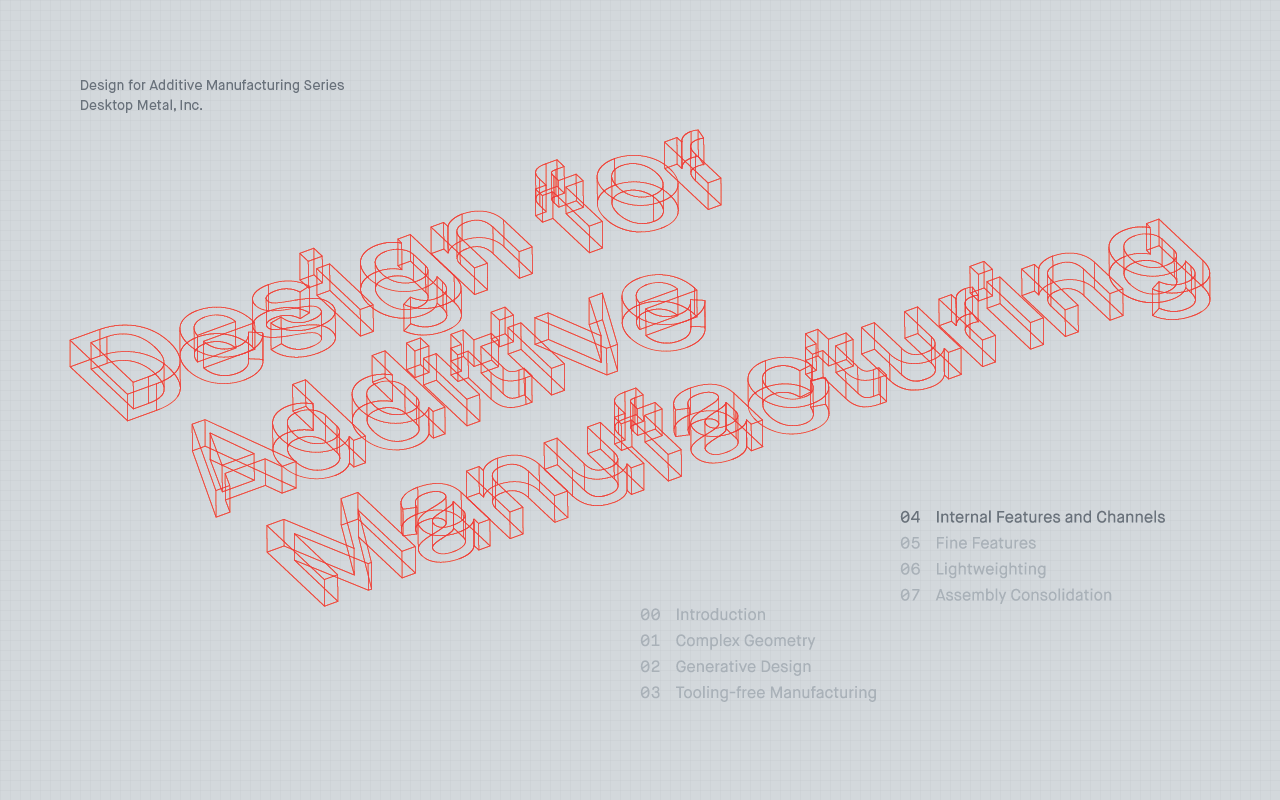
Introduction
Additive manufacturing is rapidly rewriting the rules of how metal parts are made, and it’s doing it with the help of a new design language - Design for Additive Manufacturing (DfAM).
Developed to take advantage of the enormous design freedom that comes with 3D printing, DfAM allows manufacturers unlock a host of benefits - from highly complex geometry to the use of generative design tools to the ability to create internal features and channels - and create parts that would otherwise be too difficult or costly to justify with traditional manufacturing methods.
Internal Features and Channels
For some 3D printed parts, the greatest benefit isn’t on the outside, but the ability to create complex internal features.
By building parts layer by layer, 3D printing opens new possibilities for engineers and designers to create parts with internal features - like conformal cooling channels - that would be impossible for conventional manufacturing approaches.
Incorporating such features into parts can often result in improved performance like faster cooling rates for injection molds and improved heat transfer rates for heat exchangers, leading to production increases as well reducing both the time and cost of creating parts.
Part Examples
Asthma Inhaler Mold Insert
This mold insert is used for plastic injection molding of the mouthpiece on an asthma inhaler.
When injection molding a part, cooling often accounts for up to 95% of the cycle time. Incorporating a conformal cooling channel that closely follows the surface of the mold core significantly increases the heat transfer rate, allowing the part to be cooled and ejected faster, reducing mold cycle time by up to 40%.
Faster cycle times allow injection mold shops finish customer parts faster, allowing them to quickly move on to new jobs and make more money. Internal cooling channels like these are impossible to manufacture via traditional methods but are very simple to print into the part.
Due to the hard plastic that is being injected, this mold was printed in H13 tool steel to give it significantly higher wear resistance. A very difficult metal to machine, H13 can cause considerable tool wear and very slow feed rate. Printing this part to near net shape allowed for a 95% reduction in the CNC machining required - the only need was to touch up critical surfaces and dimensions after sintering. This led to a significant cost savings for this part, even when compared to a version without the internal cooling channel.
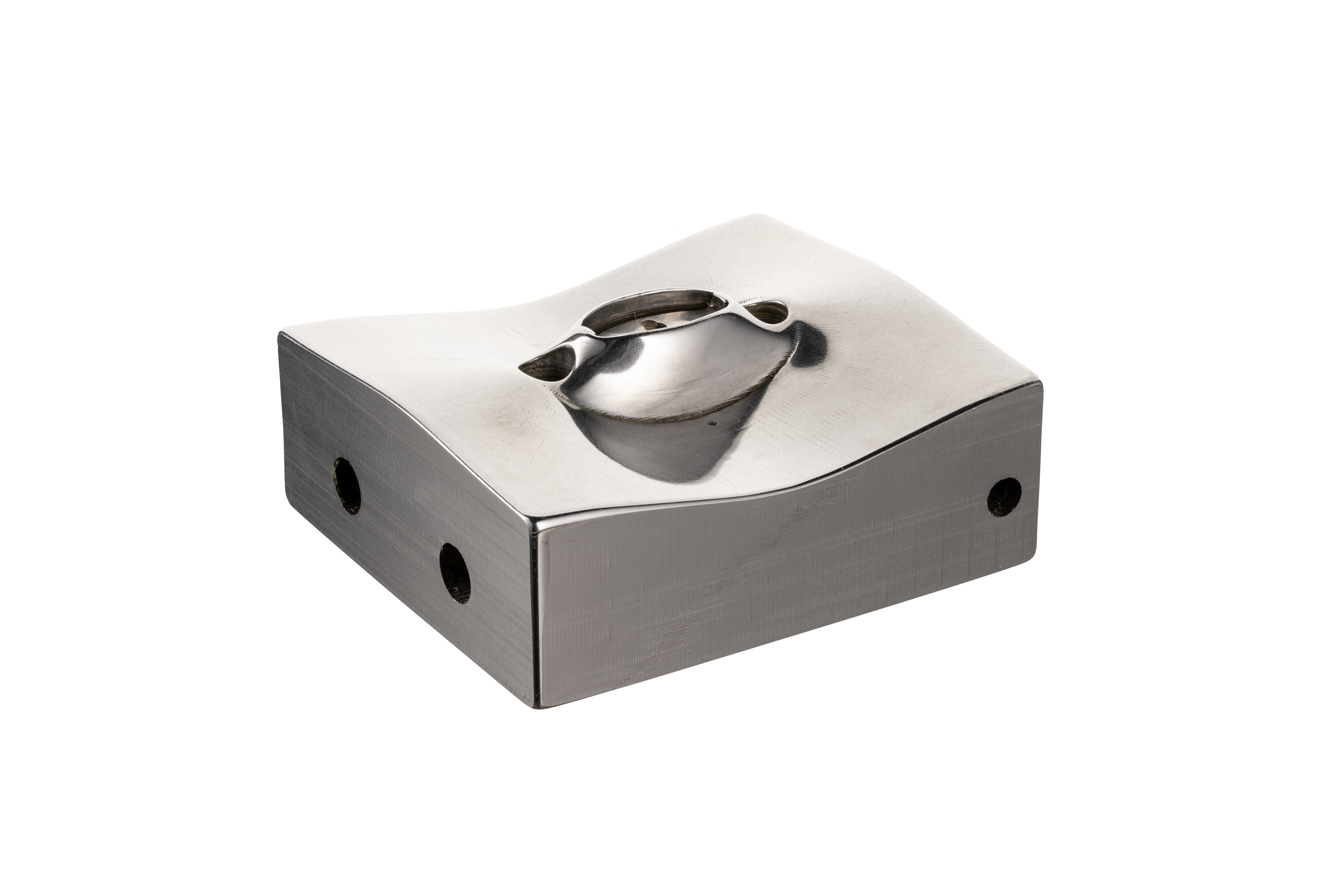
Helical heat exchanger
This heat exchanger is used for continuously cooling fluids in a chemical processing plant.
Since this part was intended for printing from the start, it could be designed with its specific application in mind, rather than for easy manufacturing. This meant printing the part with an internal helical cooling channel - a feature that would be impossible to manufacture via traditional methods.
This cooling channel substantially increases the part’s heat transfer rate. External and internal fins - features that cost very little to print, but would add significant cost if the part were machined - were also added to increase heat transfer surface area. Printing the part in copper allowed for excellent thermal conductivity through the heat exchanger.
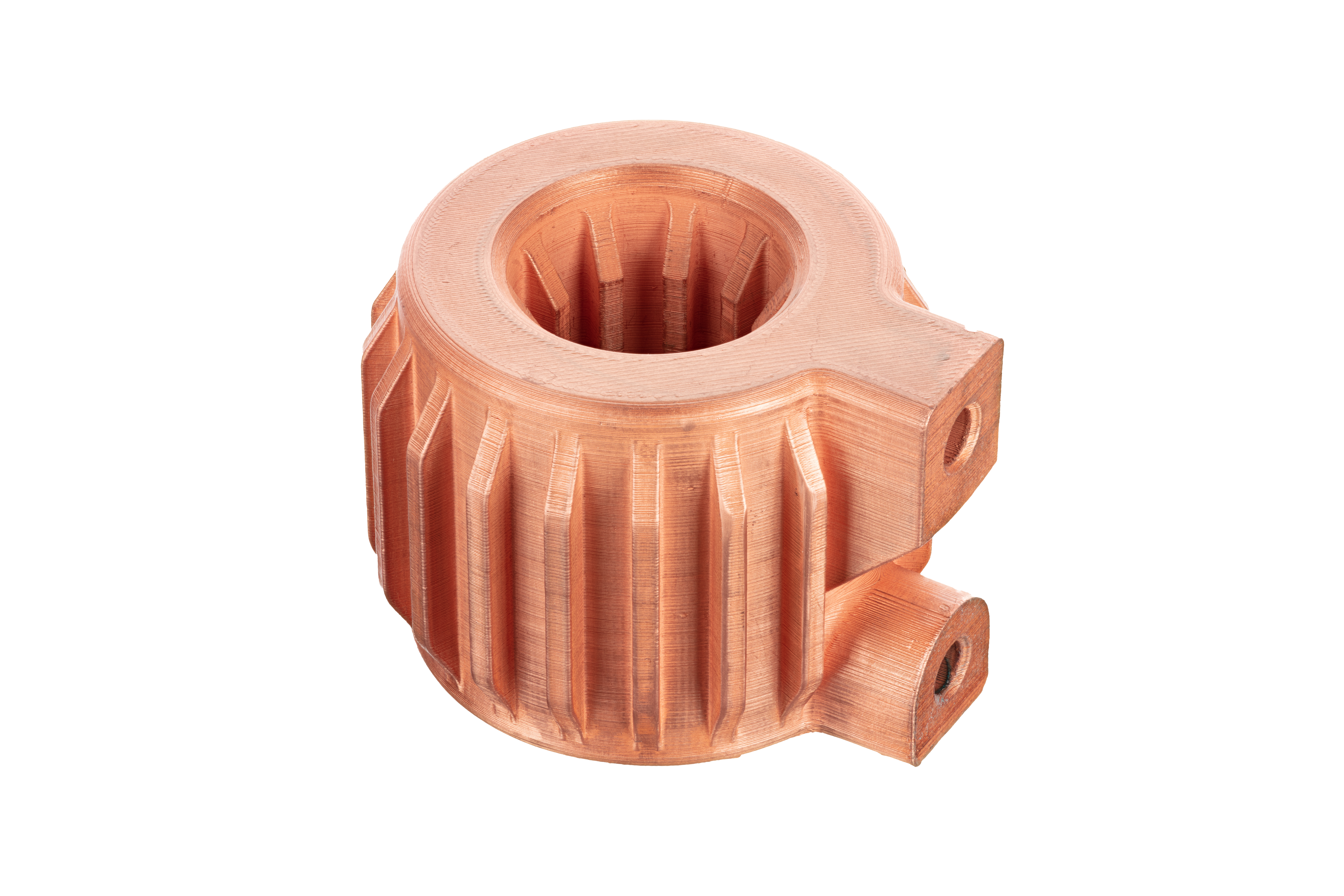
Surgical Tool
This is a nozzle used during surgery; it is beneficial for it to be customized for each patient. The part features an internal channel that would require complex machining operations with multiple fixturing setups; printing the part via binder jetting eliminates those many machining steps, resulting in extensive cost savings. Similarly since binder jetting does not rely on any tooling this part can easily be customized for specific patients.
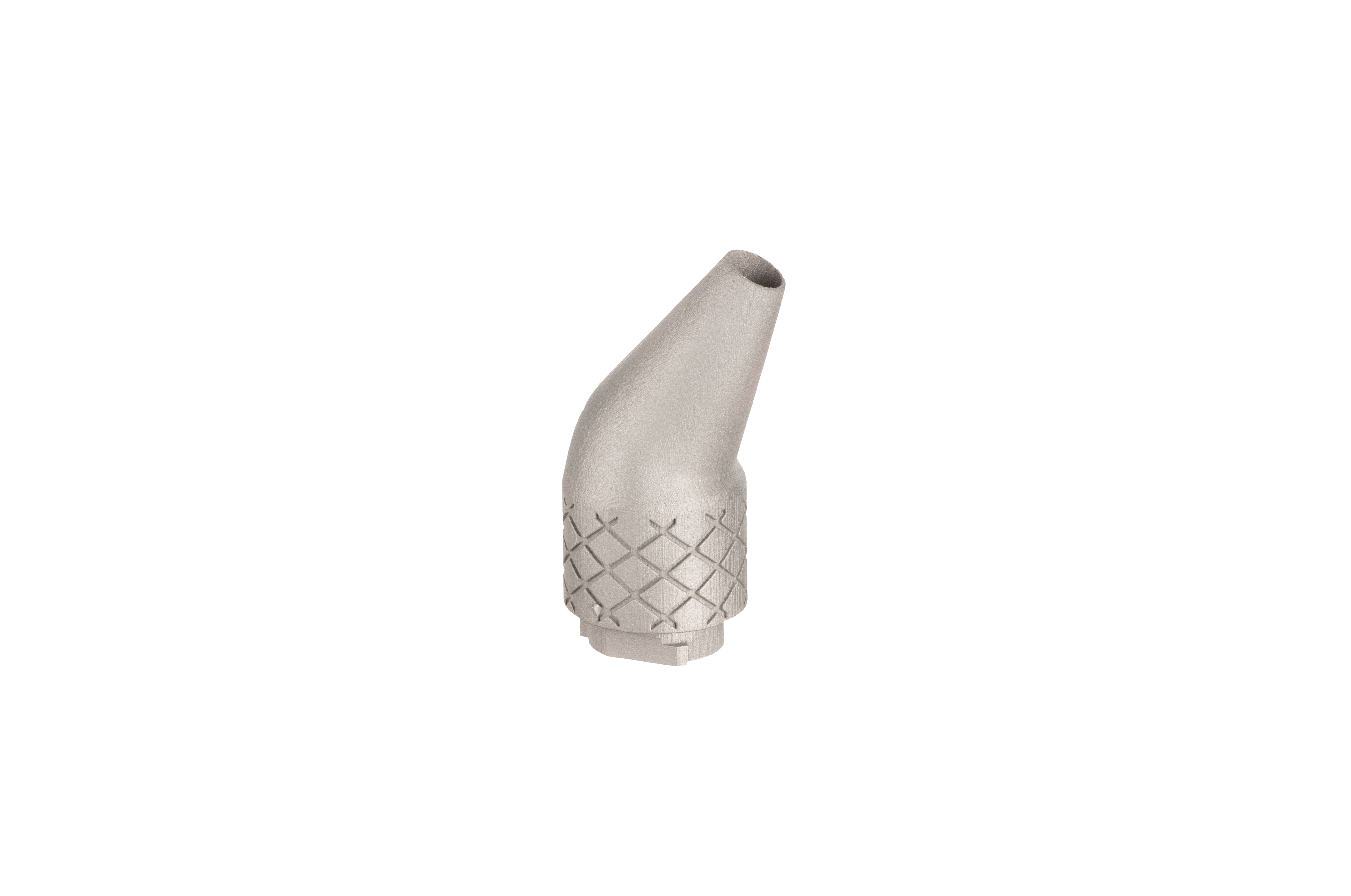
UHT Atomizer
This fuel atomizer is used for mixing steam and fuel in a steam boiler to power a liquid natural gas (LNG) tanker.
With the Studio System, the engineers were able to radically redesign their conventional atomizers for significantly better performance.
This 3D printed atomizer features complex internal channels and oblong shaped holes, which could not be manufactured with traditional methods. These channels and oddly shaped holes allowed for drastically better fuel mixing, leading to much better performance as well as fuel savings.
