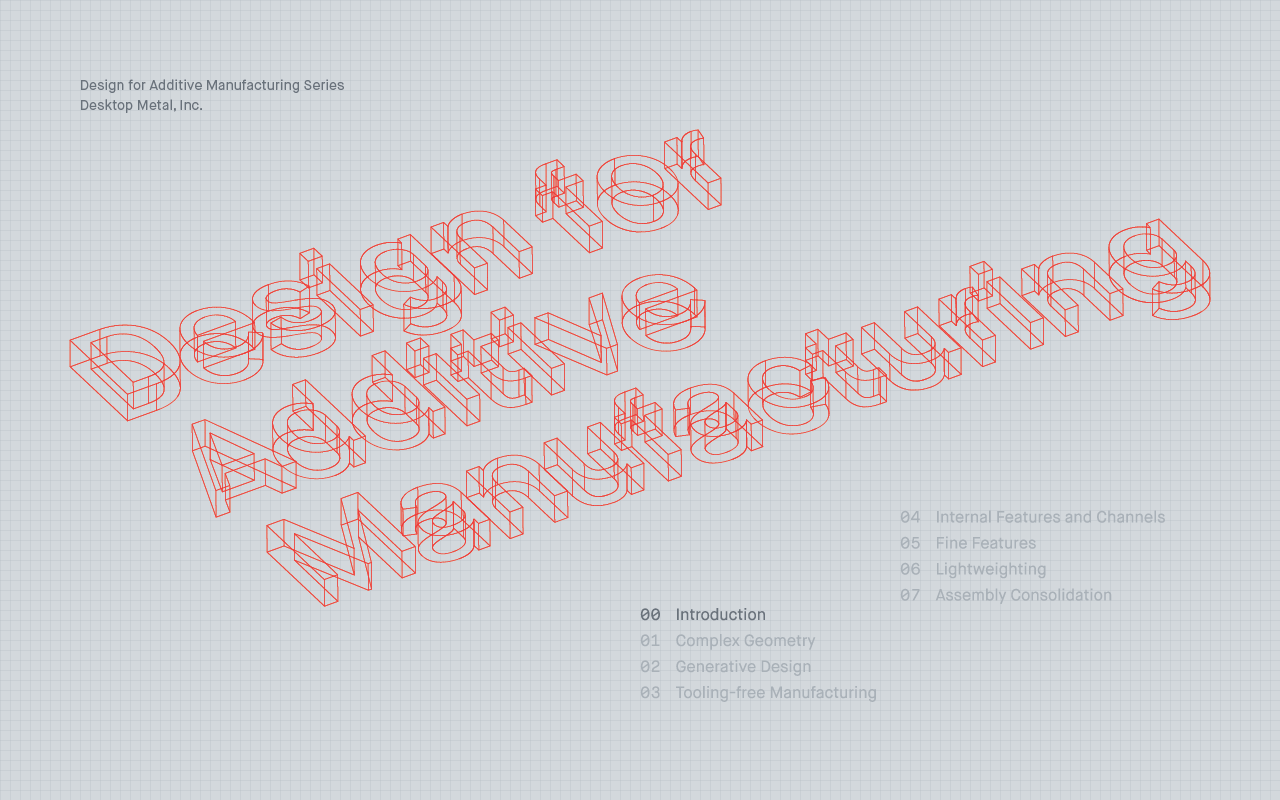
Design for Additive Manufacturing: Complex Geometry
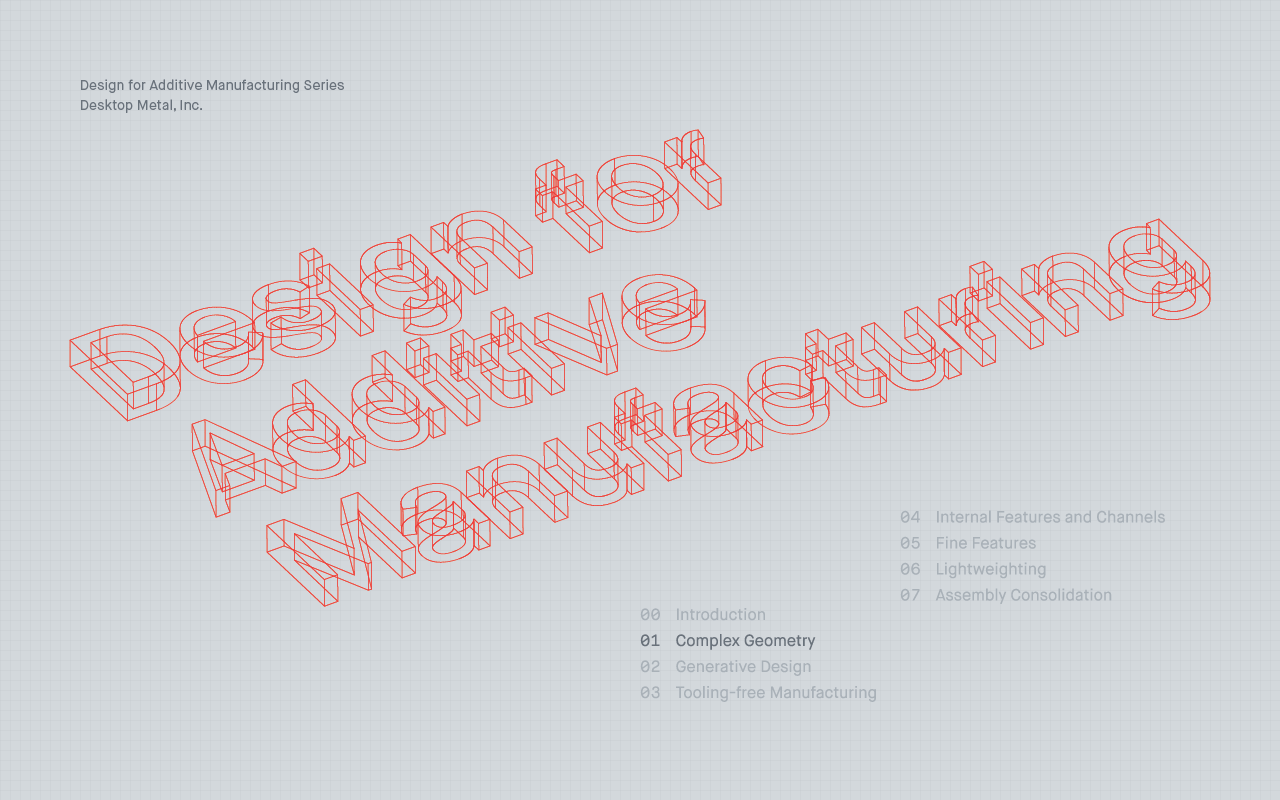
Complex Geometry
Among the chief benefits DfAM brings to engineers and designers is the ability to produce parts with far greater complexity than traditional methods.
Because it’s not subject to the same limits that apply to traditional manufacturing, additive manufacturing allows designers and engineers to access a vast new design space.
The end result, however, isn’t designs that are simply more complex, but that are often better. The ability to create highly complex parts means designers can create parts that are optimized for their precise application, not for manufacturability, resulting in parts that perform better than their traditionally-manufactured counterparts.
And because the cost of printed parts does not scale with complexity, manufacturers can keep costs low, making it far more economical to produce complex, highly-optimized parts for different applications.
Part Examples
EWOL propellor pinion
Located in Milan, Italy, EWOL is a leading vendor of high-tech marine propellers for sailing yachts.
This part is a propeller pinion [Fig. 01], used to connect the propeller shaft to the propeller blades. EWOL, however, faced significant challenges around its manufacture.
Originally produced via investment casting, EWOL had to place orders for at least 100 of the parts to justify the cost of casting. This was prohibitively large for a highly-customized, low-volume part. Casting lead times were also quite long, due to the many manufacturing steps involved, and parts still required challenging and expensive machining before a pinion could be delivered to the customer.
Using the Studio System™, EWOL was able to greatly simplify the manufacturing process. By bringing the fabrication process in-house, EWOL can be much more responsive to customer demands because they no longer have to worry about minimum lot sizes. The company was also able to reduce manufacturing lead time, lower the part cost, improve the part quality, and substantially reduce the amount of post-processing required.
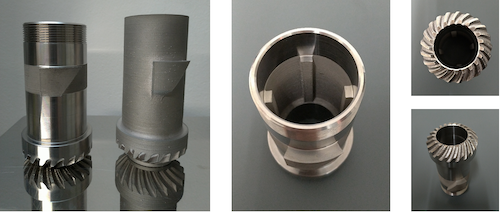
Sensor Holder
This part is used to hold multiple sensors while measurements are taken in a running machine.
The intricate small geometry of this sensor holder [Fig. 02] makes the part an ideal candidate for printing on the Shop System™.
Since this part was never produced in large numbers, redesigning it for a mass manufacturing method like investment casting or metal injection molding was impractical. By printing it, however, the team was able to manufacture the part with an extreme reduction in both manufacturing lead time and part cost.
Printing on the Shop System also allows for manufacturing flexibility - when the design needs to be modified to incorporate different sensors, engineers can simply send a revised file to the printer and have hundreds of sensor holders in their hands that same week.
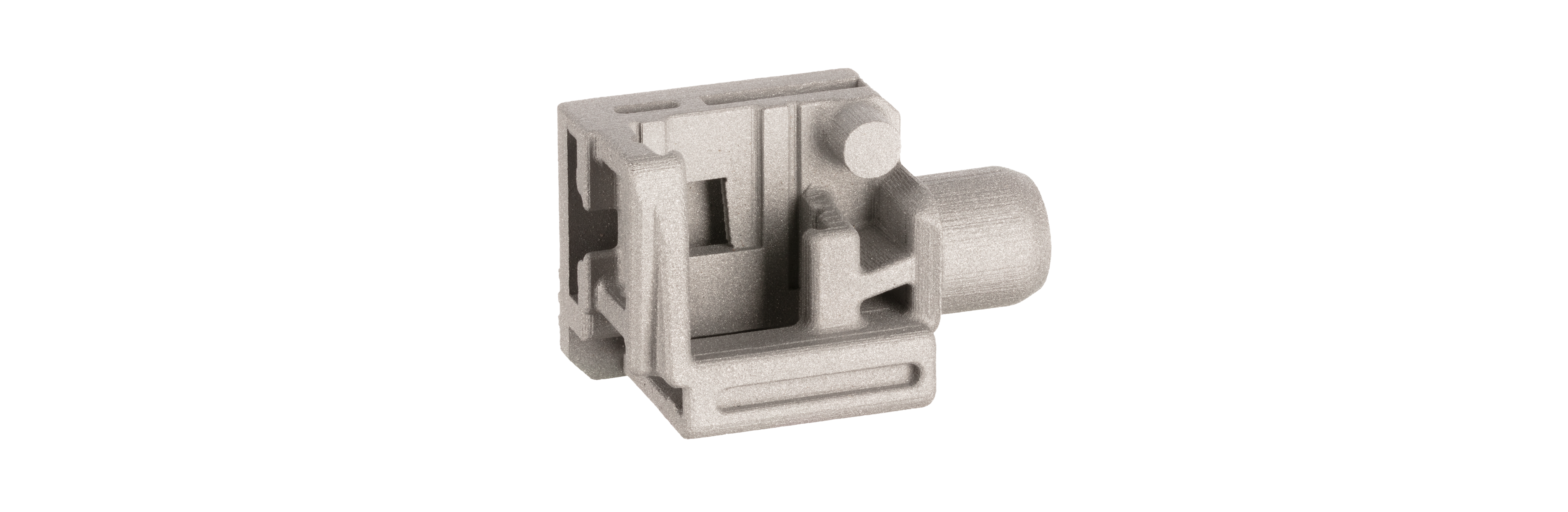
Power Steering Joint
This joint [Fig. 03] is designed to transfer power from an electric motor to the steering wheel in an electric power steering system. The part features intricate spline teeth that are used to connect the join to the electric motor, these teeth generally require extensive post processing after the rest of the part is machined, but with binder jetting the teeth can be printed with the rest of the part extremely easily. This greatly simplifies fabrication of this complex part.
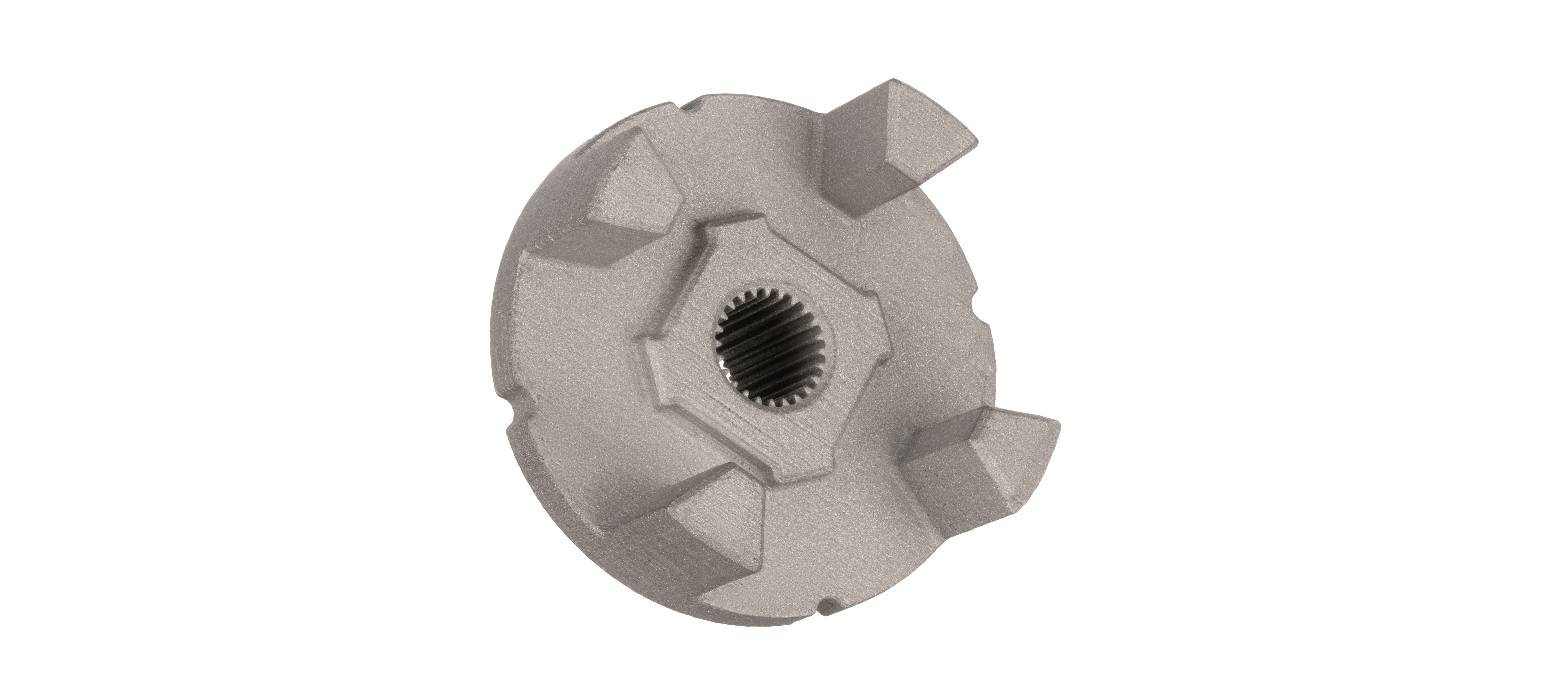
Custom Bolt
This custom-designed bolt [Fig. 04] is used in specific applications where an off the shelf fastener wouldn’t suffice. Due to the high cost of hard tooling, most bolts are manufactured in quantities of millions. For this bolt, however, only a few tens of thousands were needed. This part features complex lightweighting features as well as the thread. Threading the bolt would generally be a secondary rolling or tapping operation but with binder jetting the working thread can be printed right into the part. Printing on the Production System also allows this bolt to be produced with no tooling required, allowing for a dramatically reduced cost per part.
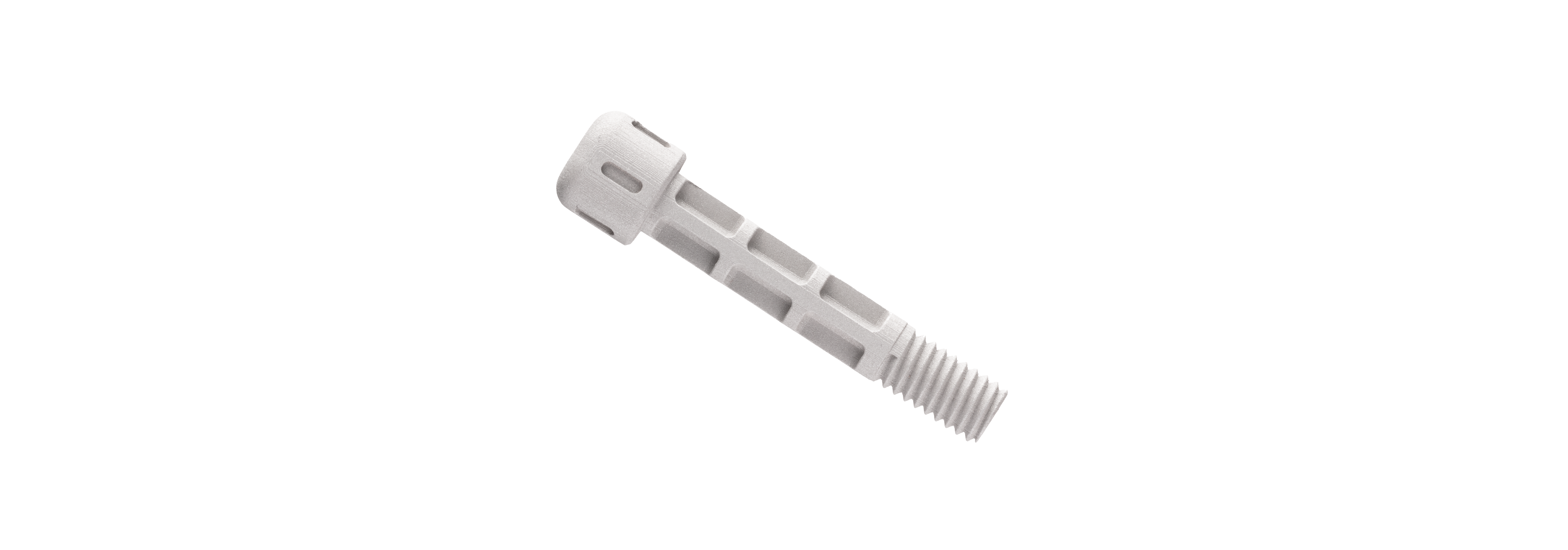