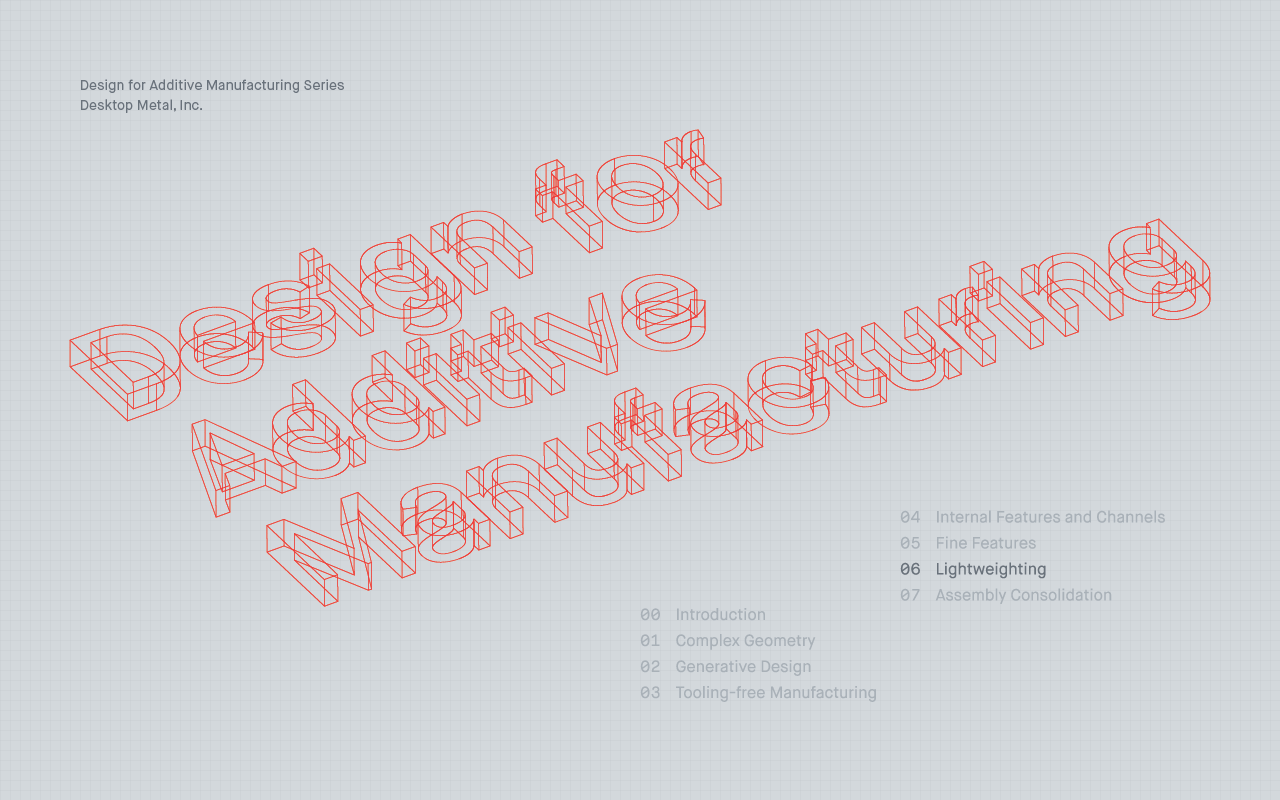
Design for Additive Manufacturing: Assembly Consolidation
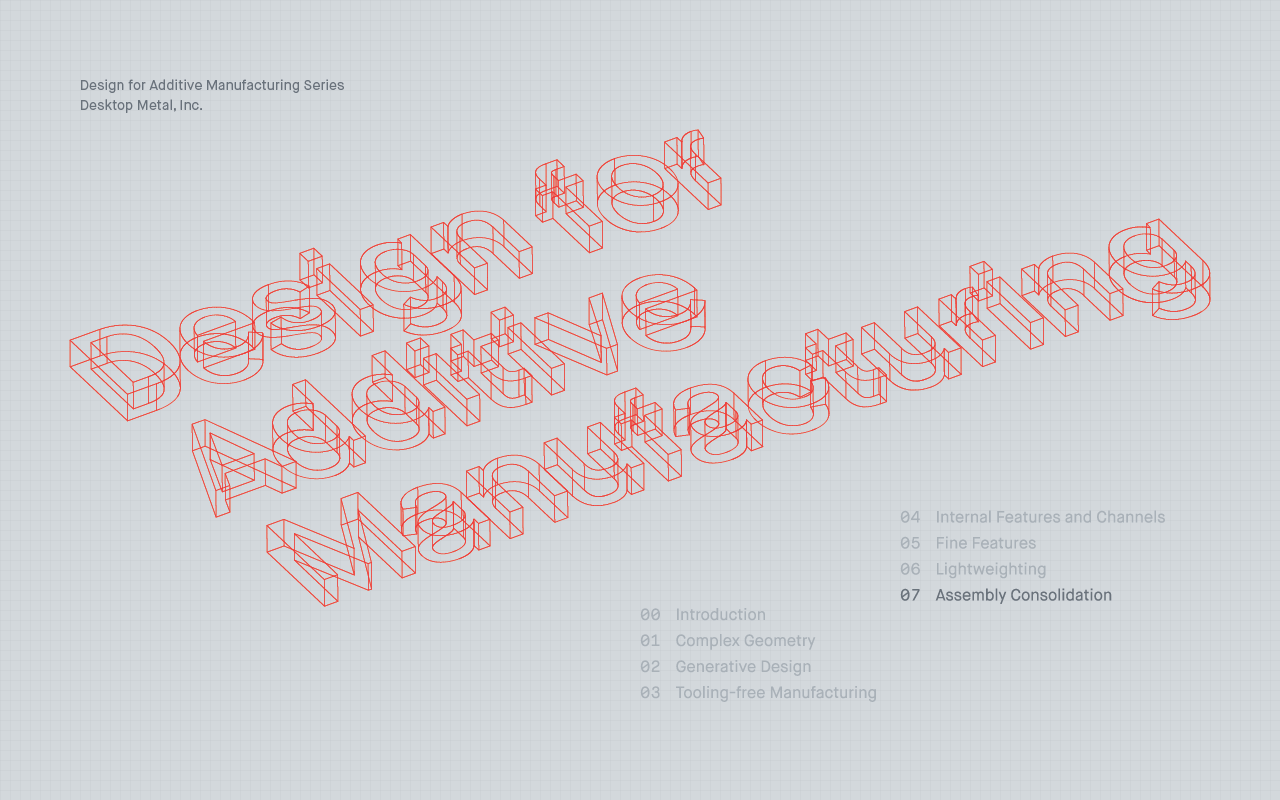
Introduction
Additive manufacturing is rapidly rewriting the rules of how metal parts are made, and it’s doing it with the help of a new design language - Design for Additive Manufacturing (DfAM).
Developed to take advantage of the enormous design freedom that comes with 3D printing, DfAM allows manufacturers unlock a host of benefits - from highly complex geometry to the use of generative design tools to assembly consolidation - and create parts that would otherwise be too difficult or costly to justify with traditional manufacturing methods.
Assembly Consolidation
The ability to create complex new geometry, combined with the additive nature of 3D printing, also opens the door to using DfAM principles to explore assembly consolidation, or the combining of several parts into fewer, multi-functional assemblies.
Because they are designed for their specific application, and not for manufacturing ease, such consolidated assemblies often outperform their conventional counterparts. Assembly consolidation can also significantly increase production efficiency - manufacturing a single part via 3D printing is faster and cheaper than producing several different parts via traditional methods and fastening or welding them together.
Other benefits of consolidating multiple parts include saving money by reducing waste, lightweighting of parts by eliminating the need for screws and other fasteners, and simplified bill of materials and assembly procedures.
Part Examples
Roller Screw
This roller screw is part of a linear actuator used to open and close pilot valves in a steam power plant.
Traditionally, this part is made by cutting the threads on a lathe - a challenging and time consuming process. Once finished, the gears on either end of the screw are assembled with set screws and adhesive.
Printing this part, however, allowed the assembly to be consolidated into a single part, which can be produced faster and more affordably than traditional machining.
This part was prototyped for functional testing using the Studio System™ before being produced in higher volume using the Shop System™.
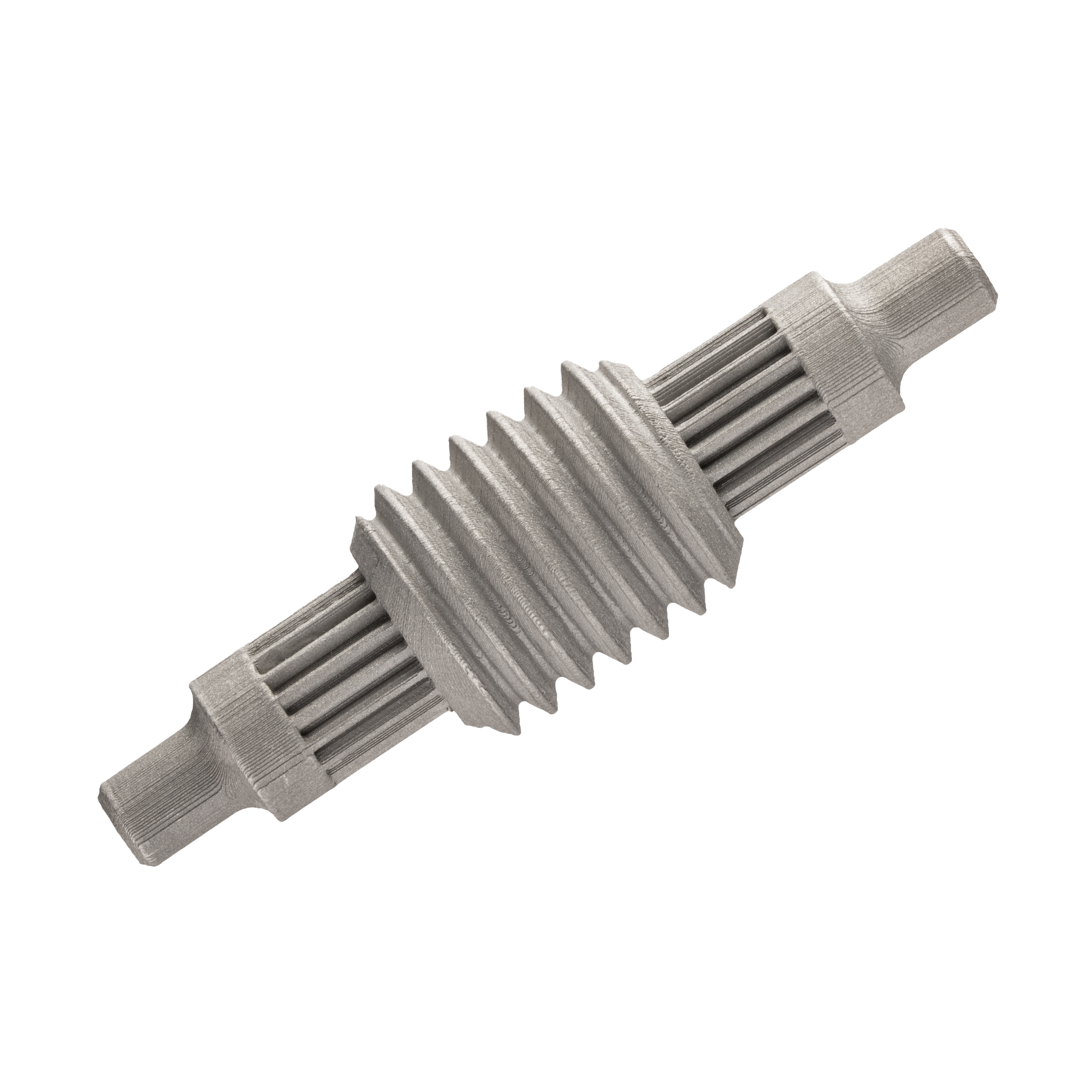
Connector
This is a fluid connector used in chemical processing.
This part features complex geometry and an internal channel that would make it impossible to manufacture as a single component via traditional manufacturing methods.
Printing this part, however, is easy, and results in a higher performance part than the traditionally-manufactured assembly, while simultaneously reducing part cost and manufacturing lead time.
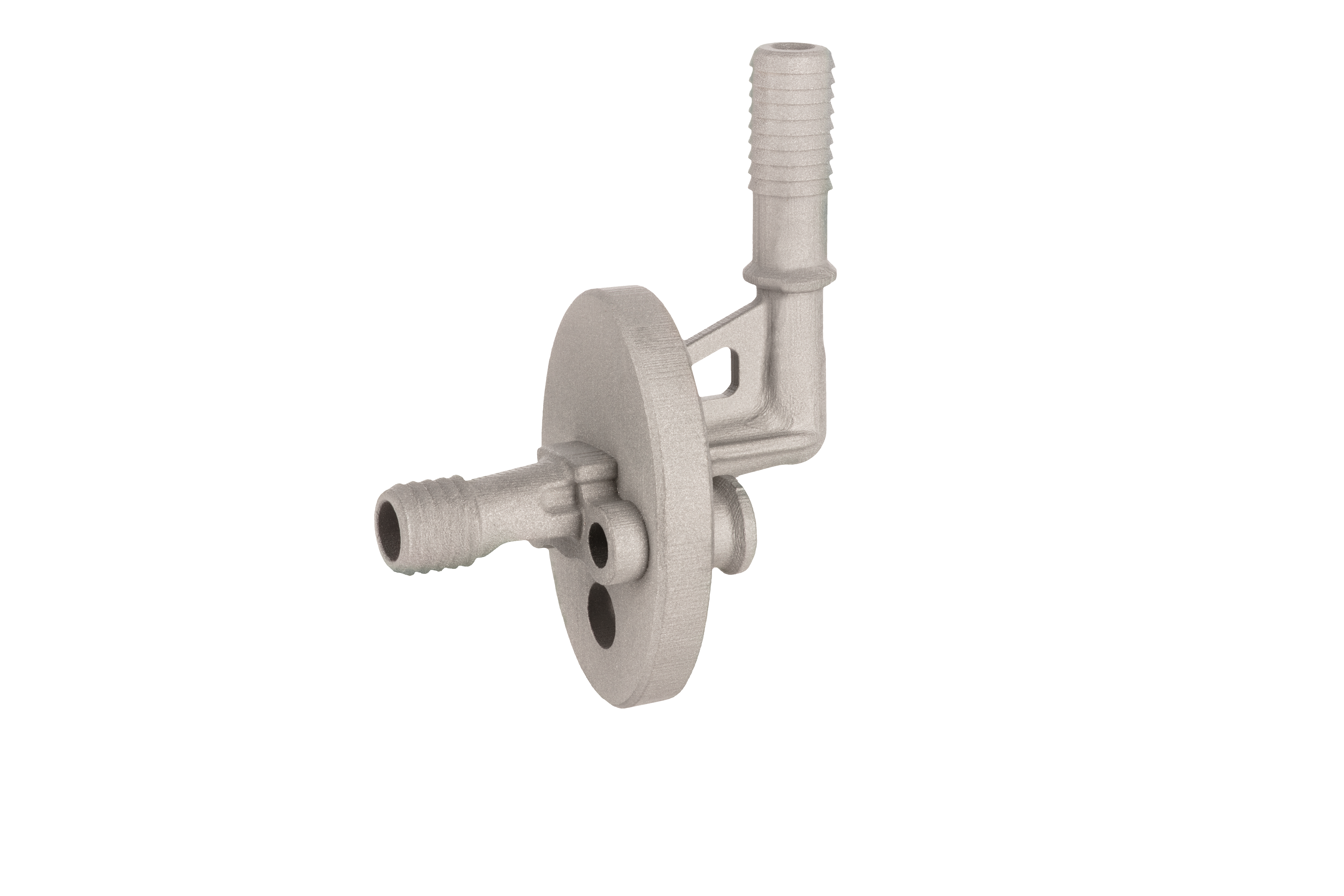
Crankshaft Starter Gear
This gear connects the crankshaft to the generator and water pump in a motorcycle engine.
Manufacturing this part via traditional methods would require casting followed by broaching operations to form the gear teeth.
Using the Studio System, the final part was fabricated in just a few days at a low per-part cost, allowing parts to be prototyped and tested quickly before moving to a mass manufacturing method.
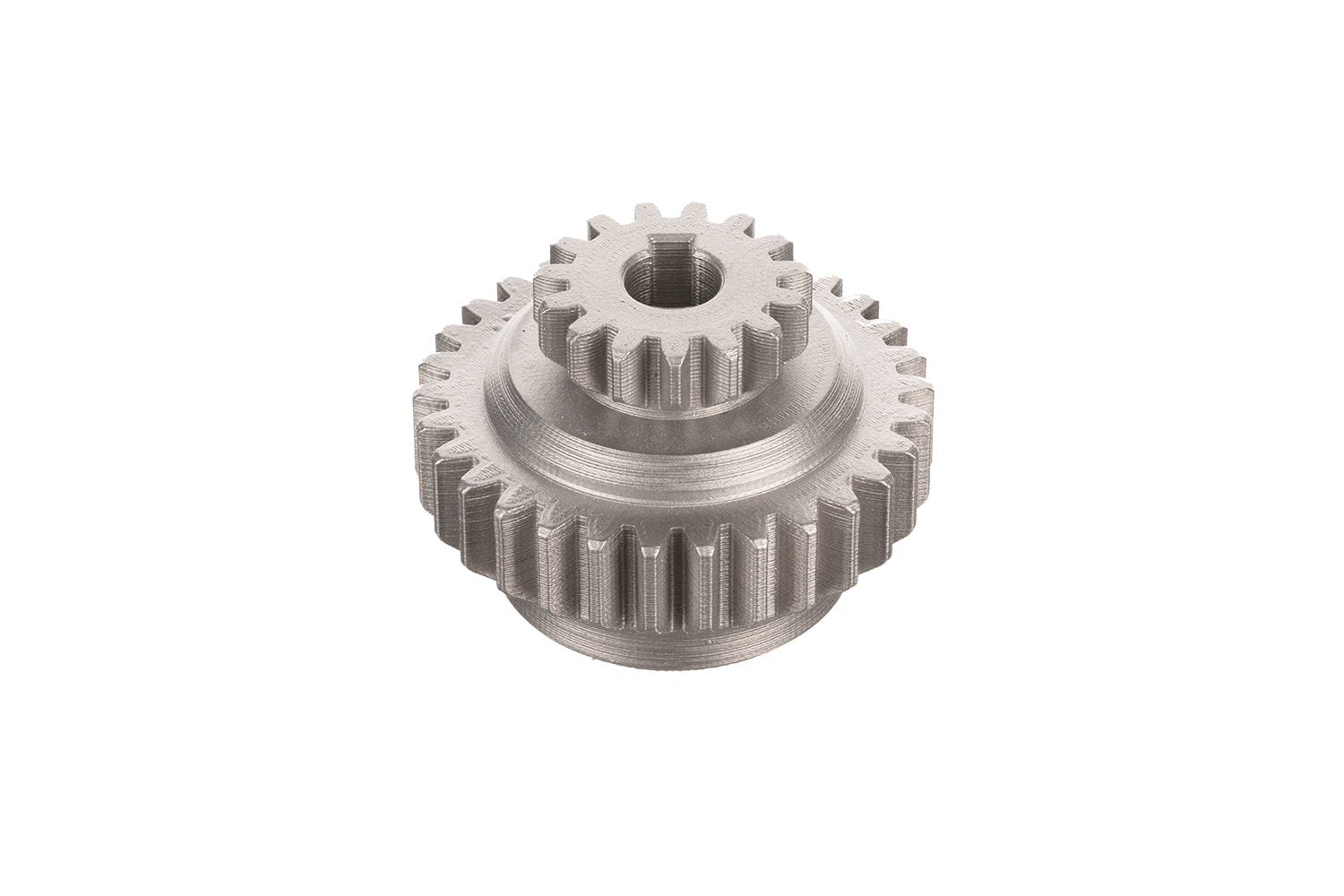