How do you value a multi-purpose tool like metal binder jet 3D printing?
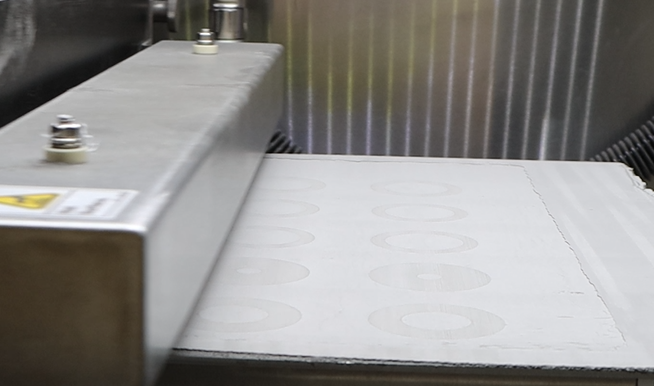
One often hears that 3D printing is “another tool in the manufacturer's toolbox.” And just like there’s no one tool to fit every job, 3D printing isn’t a panacea that’s right for every job either.
So, additive manufacturing isn’t going to completely replace CNC machining and shutter every machine shop. Rather, binder jet 3D printing is a way of harnessing metal – or other materials like technical ceramics and sand – to additively produce complex shapes in a way that’s uniquely different and beneficial from other tools that already exist in a manufacturer’s toolbox. It’s a digital manufacturing solution that eliminates hard tooling or consolidates complicated assemblies and is a powerful addition to any production facility looking to be more efficient in its use of existing machinery or unlock new opportunities. In essence, binder jetting is a smart, new manufacturing tool.
And while the benefits of binder jet 3D printing can often be measured – our customers routinely reduce the weight of their parts by 30 – 40% using our technology – much of the return on investment (ROI) of binder jetting lies in the complex intangibles and specific applications, or where one operates in the supply chain.
Machine Shops: A different way to get to an end part faster and more efficiently
Hybrid manufacturing – CNC machine tools and 3D printing working in tandem - leads to new possibilities in machine shop performance. Contrary to replacing CNC machine tools, it’s beneficial for every metal 3D printer to be supported with a CNC.
Rather than obsoleting CNC machining, 3D printing is a way to free-up capacity for CNCs to do what they do best: precision work. Hybrid machine shops let binder jetting get them to the end result faster; much in the same way a casting requires post processing to remove flash and runners or machine precision tolerances, 3D printing results in a near-net shape part more efficiently. Instead of cutting away what becomes scrap material from a billet of metal larger than the end part, powder is bound together in the shape needed, reducing waste and increasing material use efficiency. After 3D printing, critical surfaces still get machined to ensure tight tolerances. Binder jetting uses only the material needed to build the part, resulting in a greener manufacturing process and increased ROI through raw material efficiency.
Contact Manufacturers: Production flexibility
Fast turnarounds and short-run production are the lifeblood of contract manufacturers, and metal 3D printing unlocks new possibilities like the capability to offer mass customization. Without complicated tooling set-ups, designs can be changed with ease by simply uploading a new digital file. And eliminating hard tooling means multiple designs can be 3D printed at once, maximizing the ability to quickly test and iterate as well as optimize usage of the build area.
With binder jet 3D printing, for example, medical devices can be customized to improve patient outcomes and consumer products can be iterated to quickly incorporate user feedback without difficult, or expensive, modifications to the production process.
OEMs and Product Designers: Optimized designs and reductive decontenting
The benefits of design for additive manufacturing (DfAM) are well known to OEMs and product designers. Conceptualizing a component for function, rather than traditional manufacturability, leads to increased performance from optimized, often organic designs. Yet the ROI extends beyond the part itself, significantly contributing to overall reductive design efforts.
The benefits of generative design to lightweight a particular component lead to lower weights for reductive decontenting. Using optimized designs produced with binder jetting can reduce the size of an engine, for example. The smaller engine then requires a smaller housing surround – requiring less material thus reducing weight and cost. This add-on effect leads to even lighter end products that take less energy to move.
Where to start: From get-started-today models to partnerships for process development
Metal 3D printing can bring transformative benefits to a variety of business cases, and Desktop Metal has a range of solutions to meet the needs of any manufacturer.
The two-step, powder-less bound metal deposition process of the Desktop Metal Studio System is perfect for any office, lab, studio, or classroom space looking to get started with metal 3D printing without extensive facility or safety requirements.
As the leading binder jetting experts, Desktop Metal is home to a range of binder jet 3D printing systems to process metals, sands, technical ceramics, and a variety of upcycled powders like wood.
The Shop System is a complete, easy-to-adopt solution with a software guided workflow designed to be user friendly and highly productive
The Production System achieves speeds to produce parts in volumes and at costs competitive with conventional mass production techniques
The X-Series is a scalable platform that processes specialty materials like silicon carbide, aluminum, or copper
Desktop Metal’s low-risk production adoption process helps ensure success with any manufacturing challenge. Our team can help determine if our technology is right for your application — from finding the right machine for your manufacturing challenge to business case validation and operations support. Learn more about how we partner with you for the whole journey — from both a technical and business perspective — for additive manufacturing 2.0 success.