Preliminary Findings of the Yale-AMGTA Binder Jet Life Cycle Analysis: Binder Jet Delivers 38% Reduction in Greenhouse Gas Emissions
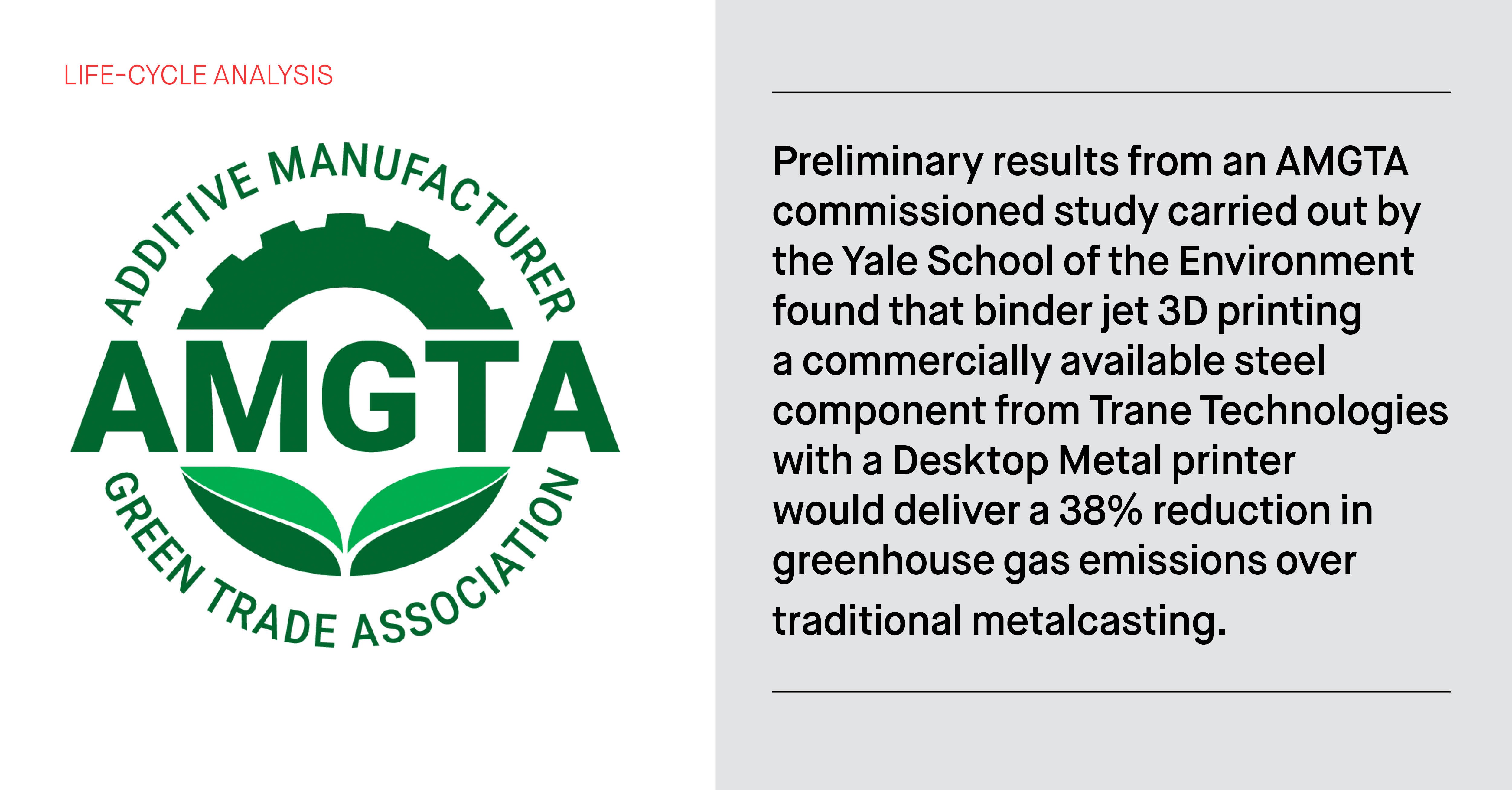
Speech to AMGTA Summit, May 2023, by Jonah Myerberg, Chief Technology Officer, Desktop Metal
As one of the original founders of Desktop Metal, I can tell you that we believe – and have long believed – that we offer one of the most sustainable methods of manufacturing metal with our binder jetting portfolio. Our entire vision of Additive Manufacturing 2.0, to enable production volume additive manufacturing, is driven by the desire to make the sustainability benefits of AM more widespread through higher volumes, so the impact of those benefits can be more broadly realized
I’m here to share with you the preliminary results from a new study funded by AMGTA in partnership with the Center for Industrial Ecology at Yale University, who conducted the study, Trane Technologies, a global climate innovator, and Desktop Metal.
As you all know, one of AMGTA’s goals is to sponsor studies like this to uncover the truth about how AM compares to other forms of Manufacturing. AMGTA’s objective is to be unbiased in these studies and to present the facts, which I will do. But before we get into the results, I’d like to briefly explain what binder jet 3D printing is and why this group of collaborators thought it was important to answer sustainability questions about this particular form of AM.
The Sustainability Case for Binder Jet 3D Printing – and AMGTA
Binder jetting, if you’re not familiar with it is a method of 3D printing in which a digital file is used to quickly inkjet a binder into a bed of powder particles—such as metal, sand, or ceramic—to create a solid part, one thin layer at a time. Unlike other forms of powder-based AM, we do this at room temperature. When printing metals, the final bound metal part must be sintered in a furnace to remove the binding agent and fuse the particles together into a solid object. Sintering is a higher energy component of this process, but overally, you’ll see binder jetting is very efficient overall.
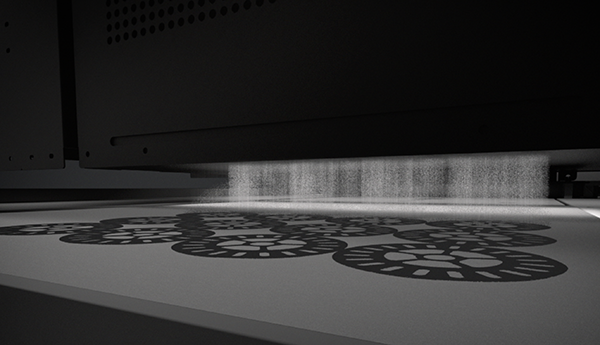
In the AM world, Binder jet 3D printing technology has long been viewed as a desirable and sustainable production method, largely because of its high speed, near zero waste, and its ability to produce new geometries in high volumes thanks to our area-wide printing approach.
As I mentioned, that means we can scale up more earth-friendly designs and materials to deliver higher volumes – with more meaningful sustainability benefits. This is a really important distinction of Binder Jetting versus other metal printing technologies.
But we’ve never really shown how – in detail – binder jet compares to traditional manufacturing methods and even other AM methods for reducing the environmental impact of metal manufacturing. In manufacturing, there are many methods in your tool bag, and every part has its best tool. Binder Jetting is another manufacturing tool we need to apply correctly.
Increasingly, customers were asking us questions about Binder Jetting and we needed empirical evidence to convince them to make the leap into a new, greener way of manufacturing metal parts.
Here are some of the questions we found both ourselves and customers were asking:
- Does binder jetting really reduce waste when you look at the whole lifecycle?
- Does binder jetting reduce GHG emissions when you consider everything?
- How meaningful are new geometries enabled by AM, such as lightweighting benefits?
- Does volume impact really matter?
Not only did we need to know the answers to these questions, our customers wanted to know quantitatively how binder jetting compared to traditional methods. Because they needed to know whether the impact was big enough to invest in changing.
At Desktop Metal and ExOne -- two leading binder jet brands now under one roof since 2021 -- we did not want to greenwash these answers. We needed an independent third party to uncover the truth. We also felt this was a deeply important and relevant topic for today, after all this is why so many of us had gotten into this technology area in the first place.
Before we get to those findings - it’s worth reviewing why this data is so important. We sometimes spend so much time in AM talking about the benefits that our technologies unlock, and not enough time talking about what they can eliminate. The United Nation reports that approximately 10% of greenhouse gas emissions DIRECTLY come from metal manufacturing.
That makes metal manufacturing one of the largest single contributors to GHG emissions and particulate pollution, which you can see in the gray bar for metals in the top right chart. The surge in metal production during the Industrial Revolution in the late 1700s has never really stopped growing, as you can see in the lower right, due to a globally growing middle class and high consumption.
In study after study, such as this one from a leading research institution in Japan, metal production is a critical element of reducing GHG emissions and meeting global goals to try and contain global warming. In fact, this particular report calls reducing GHG emissions from metal production “essential for achieving climate goals.”
So, you can see how the results of this research with AMGTA, Yale, Trane and DM is important to not only our AM community, but also to the direction of metal manufacturers everywhere.
So, let’s talk about this Life Cycle Analysis Study, comparing Desktop Metal’s Binder Jetting to that of an industrial part currently in production. AMGTA worked with Yale and Trane to design a study that would deliver an unbiased comparison of these 2 manufacturing methods. We wanted to study a real industrial part and compare greenhouse gas emissions for both binder jetting and the traditional manufacturing method.
We also wanted to understand the implications that production volumes and some other variables had on the results, to really dig in and provide useful data to manufacturers who are currently facing these same questions.
A steel scroll set used in an existing Trane HVAC unit was selected as the part. It was decided to not make any modifications to the part we decided to study, so that we could have an apples-to-apples assessment of manufacturing only. Now, we know AM unlocks all kinds of other add on benefits that Trane would take advantage of, but for this study lets consider those as icing on top.
Here’s a closer look at the 2 scroll parts in the set, which have some inherent complexity in their designs. The size of each part is approximately 774 cm3 for the orbiting scroll and 1,288 cm3 for the fixed scroll. The processes being compared were traditional metal casting using a traditional sandcasting approach, and of course metal binder jetting on a desktop metal machine.
For those of you not familiar with traditional sandcasting, a tool is created that represents the 2 sides of the part, the core side and the cavity side. A sand mold is then formed and assembled from both sides of this tool, and then molten metal is poured into this mold package, where it hardens and is then broken out. In this case, the part is then machined, plated and finished.
This study was a cradle-to-gate study, which includes raw material production, transportation and the manufacturing processes, until the part leaves the factory “gate”. It does not include what comes after that. So, the same finishing processes were assumed but no use-phase or end-of-life phase were considered, as those were assumed to be the same.
We also leveraged some existing data from Ecoinvent, the world's most consistent and transparent life cycle inventory database. And our team at Desktop Metal provided real data on use of our X-Series printers and third-party furnaces that would be needed to sinter these parts.
Here are the results of the study, broken out with every step of the manufacturing process to show where equivalent C02 emissions are found. As you can see, in the casting process, the casting or pouring step was the biggest contributor of emissions, accounting for 262 kg of CO2, or 63% of the total 415 kg of Co2 emissions. In the binder jetting process, the sintering process was the largest contributor, but only accounted for 103 kg of C02 emissions, 40% of the total 257 kg of C02 emissions.
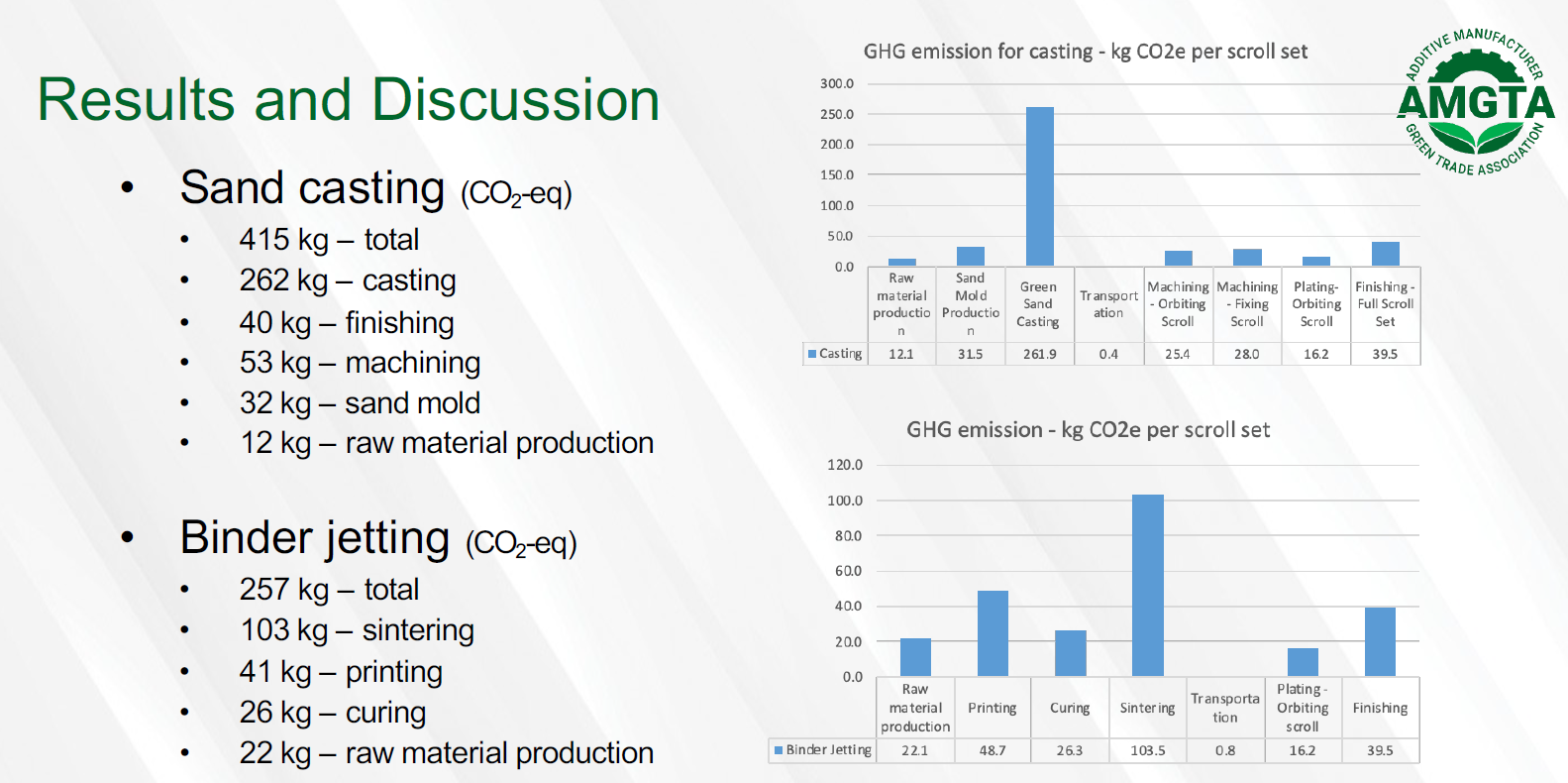
Binder Jetting, in all, proved to be a 38% reduction in greenhouse gas emissions:
Here you can see a side-by-side comparison of each step in each process. Binder Jetting requires a slightly less efficient Raw Material production process, but this allows for the elimination of the significantly less efficient pour casting process, shown in gray, and the introduction of a much more efficient sintering process, shown in dark blue, even when combined with the low temp printing process.
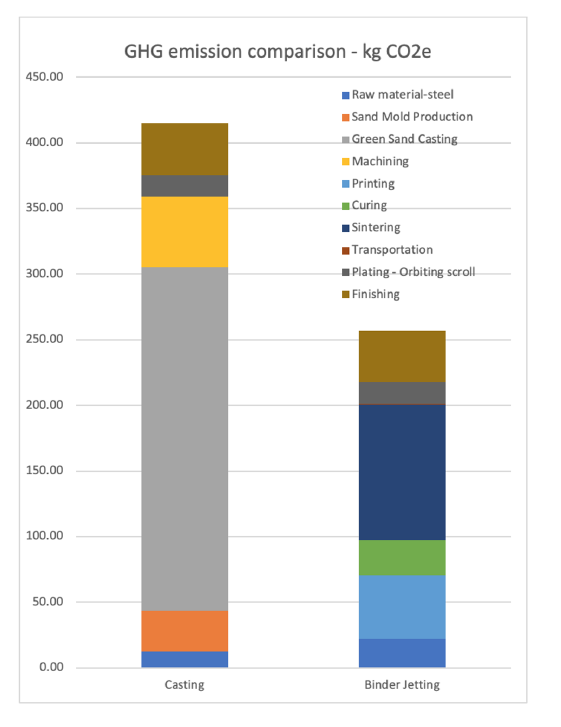
Digging further into the details, we find some really interesting things that customers should consider when making their manufacturing method selection.
Flexing the source of electricity that we used in the LCA shows us what type of effect renewable energy has on the study, and thus each method of manufacturing. The study showed that greener forms of electricity can have a significant additional affect on Green House Gas Emissions for both manufacturing methods, up to a 66% improvement in countries like Sweden, but that the results still stand nonetheless, Binder Jetting always remains as a cleaner option.
It also showed that production volumes can have a benefit in greenhouse gas emissions, depending on the Binder Jet machine that is used.
Trane explains why this research was so important to them here: “Prior to this project, uncertainty about the life cycle emissions of binder jetting versus conventional manufacturing approaches was a barrier to AM adoption. With the results of this study, Trane Technologies is in a better position to comprehensively consider AM's cost, productivity and environmental impact earlier in a product's design cycle, when risk is lowest, and the potential benefits are highest.”
This is not the first data, nor will it be the last data, demonstrating the inherent advantages in sustainability of Binder Jetting as a tool for mass production.
This new AMGTA research adds to previous binder jetting research, such as this from Oregon State University, strengthening binder jetting’s case for metal part production. This study by Oregon State and their Advanced Technology and Manufacturing Institute concluded that metal powder could be directly recycled or reused at least 16 times in the binder jetting process, for an overall material efficiency of 96%. This is many more times that other process that use similar powders. At Desktop Metal, we often reuse material even more frequently than this, without the need for recycling activities offsite. This efficiency has additional important implications for lower cost and lower levels of environmental impact, but that’s part of a future study…
In conclusion, Desktop Metal offers a variety of metal 3D printing options that are being proven to compete with conventional metal production in many ways.
We’re incredibly grateful to the team at AMGTA for their support into this important type of research.