The Importance of Inerting for Additive Manufacturing
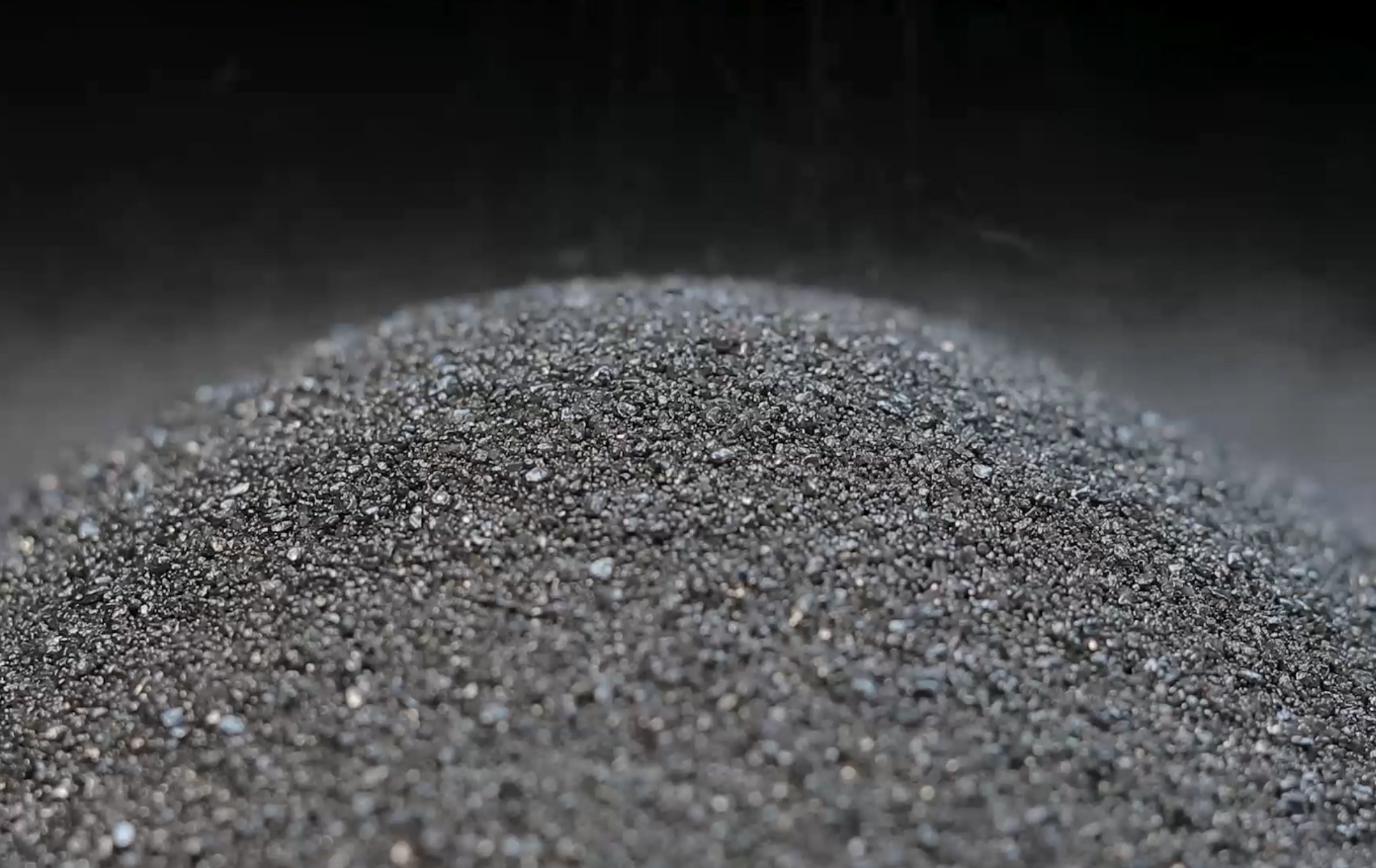
From the start, the Desktop Metal Production System P-50 was designed to incorporate inerting throughout the binder jetting process. This was a key decision, and is central to our ability to offer a system compatible with the widest range of powders.
This paper describes why that choice was made, and why customers of metal additive manufacturing systems should look for this feature in their metal binder jetting solution.
Safety
Most people understand that many powders - even those that are often considered “safe” in everyday life, like dust, flour, sugar or pollen - can become dangerous when dispersed in the atmosphere. If the conditions are right, all can cause an explosion.
To better understand those conditions, researchers created the “dust explosion pentagon,”¹ which illustrates the five elements that must be present to produce a dust explosion.
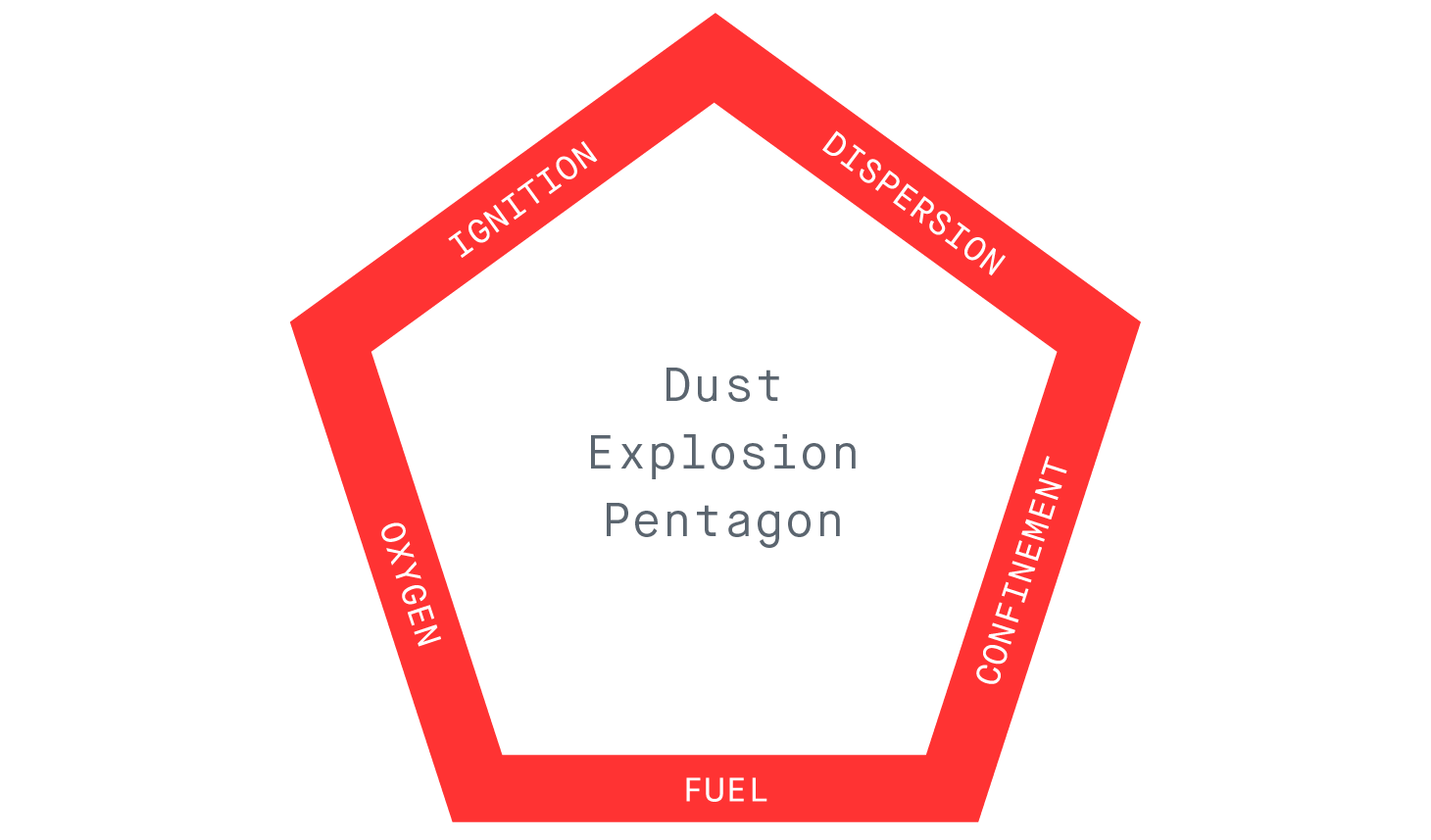
The fuel is the powder itself, but it is important to remember that any material that combines with oxygen (oxidizes) can be made to explode if the other conditions are present.
The more readily a material oxidizes, the more likely or vigorously an explosion can happen. Removing any one of the sides of the dust explosion pentagon removes the explosion hazard². For example, removing all possible ignition sources or limiting oxygen concentration would make a powder unable to ignite.
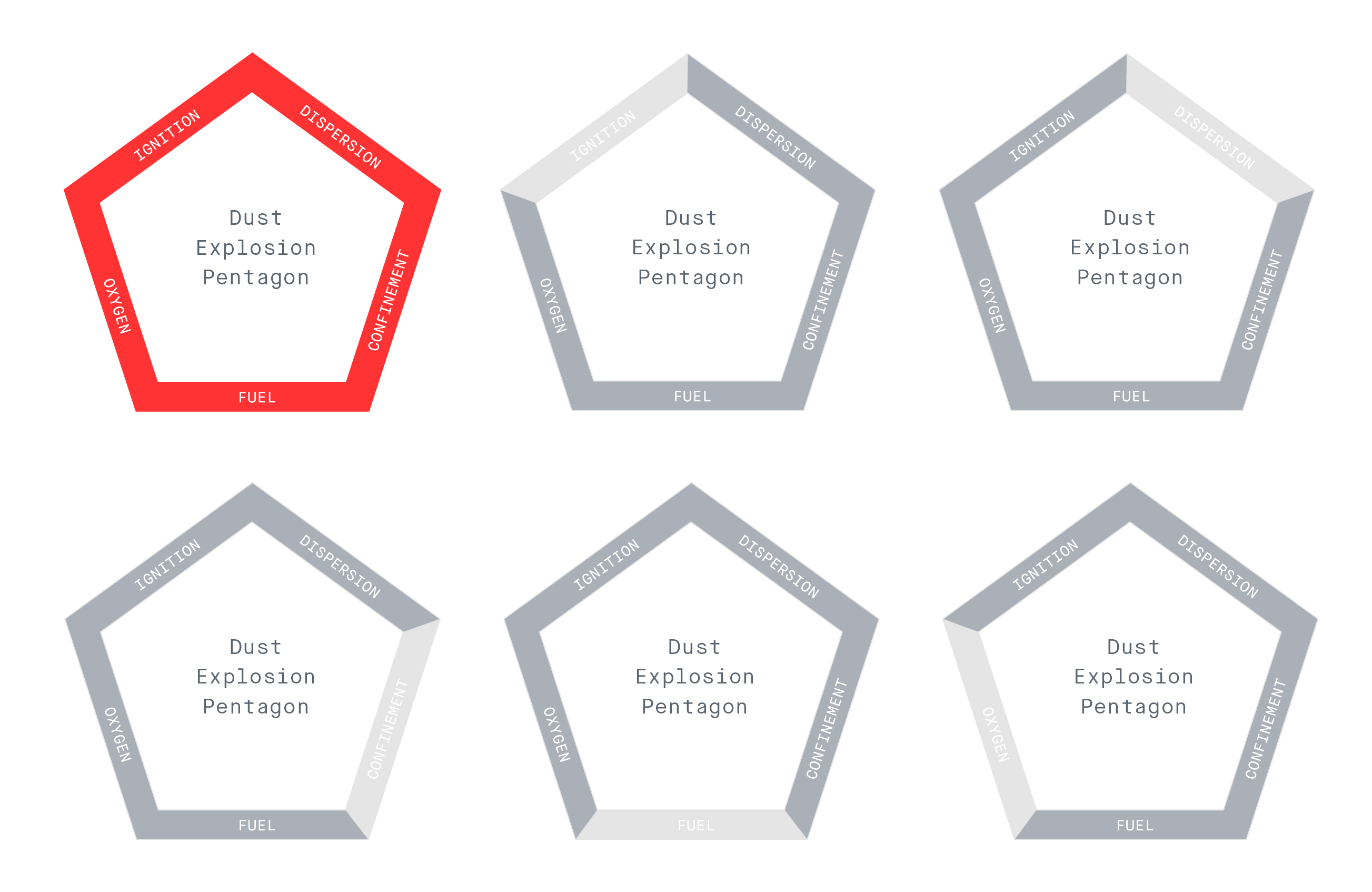
A safe way to process metal powders
There are several standards outlining the safe handling of powders. For metal additive manufacturing, the most relevant is NFPA 484, which outlines the steps additive manufacturing system providers should take to produce components that can safely handle potentially explosive powders.
A number of steps system providers can take are spelled out in the NFPA 484 standards, but the preferred method is to prevent explosion through oxidant concentration control. By using processes that take place in an inert gas or vacuum environment where oxygen is present only at low concentrations, providers can remove the “oxygen” side of the dust explosion pentagon. Desktop Metal’s Production System P-50, and it’s smaller sibling, the Production System P-1, use an inert gas environment throughout all processing steps to ensure safe operation with a wide range of powders.
In situations where oxygen control is not possible, NFPA 484 offers several other alternatives. These methods attack other legs of the pentagon and include controlling dispersion with continuous air filtration to ensure low fuel concentration, eliminating ignition sources, using enclosures that can withstand an explosion or controlled venting in the case of ignition. Many of those alternatives, however, are not effective across a broad range of powders, making them less preferable than an inert environment.
Another consideration is the way regulations may change over time. By choosing the most preferred mediation method, the P-50 system ensures compliance into the future.
Enabling the broadest range of powders
Both the P-50 and the P-1 systems were designed from the ground up as an open-powder system, allowing customers to use off-the-shelf MIM powders, custom or proprietary powders, or some combination thereof.
To maximize the range of powders compatible with the system, inerting is a clear choice. By limiting oxygen concentration to no more than 2 percent, both systems have the broadest range of powder compatibility on the market today.
Alternative approaches can’t offer this range and flexibility. As an example, consider approaches that remove ignition sources. While it is possible to source components, like motors and switches, with protective, sealed housings that limit their chance of causing ignition, a binder systems will still use inkjet printheads to eject binder onto the powder. Those printheads and their electronic drivers are significant consumers and dissipators of energy and, by definition, must be in relatively close proximity to the powder.
That close proximity limits the types of powders which could be used. Only powders with a sufficiently high Minimum Ignition Energy (MIE) - specifically, one higher than the energy stored in the printheads and their drive electronics - could safely be used.
Best material and part properties without compromise
Other approaches to solving this problem also result in compromises in the manufacturing process or in the material properties of the final part.
For example, systems that don’t rely on inerting may claim compatibility with Ti-6Al-4V powder, but can only accomplish it by limiting the minimum particle size in the feedstock powder. While this creates a less explosive powder – bigger particles have lower surface area, which limits the rate the powder can oxidize - it can also have significant consequences on final part and material properties.
The final step in the binder jet process is sintering, which consolidates parts into their final, solid form. Sintering works by reducing surface energy, so the less surface area a part has, the less surface energy it will start with. The result is longer sintering cycles, and potentially incomplete densification of the metal, which could leave voids in the material that can lead to compromised material properties.
Larger particles may also require higher sintering temperatures, increasing the likelihood of slumping and distortion during sintering. With few particle-to-particle contact points between larger particles, the risk of distortion increases even more. Larger grain sizes can also result from higher temperatures, compromising final material properties.
While systems without inerting may claim compatibility with a wide range of alloys, it’s likely they rely on feedstock powders with larger particles, forcing customers to make compromises. Other approaches, like pre-coating the powder, can force even more compromises and limit the choice of off-the-shelf, low-cost powders that are available today.
Summary
By providing an inerted system, the P-50 increases material compatibility and the range of powders that can be used, both of which maximize value for the customer.
By enabling unique applications with novel and proprietary powders as well as compatibility with widely-available MIM powders, the P-50 realizes the lowest per-part cost available for today’s metal additive market. For us, the choice was clear.