University of Maine: Advocating for Advanced Manufacturing
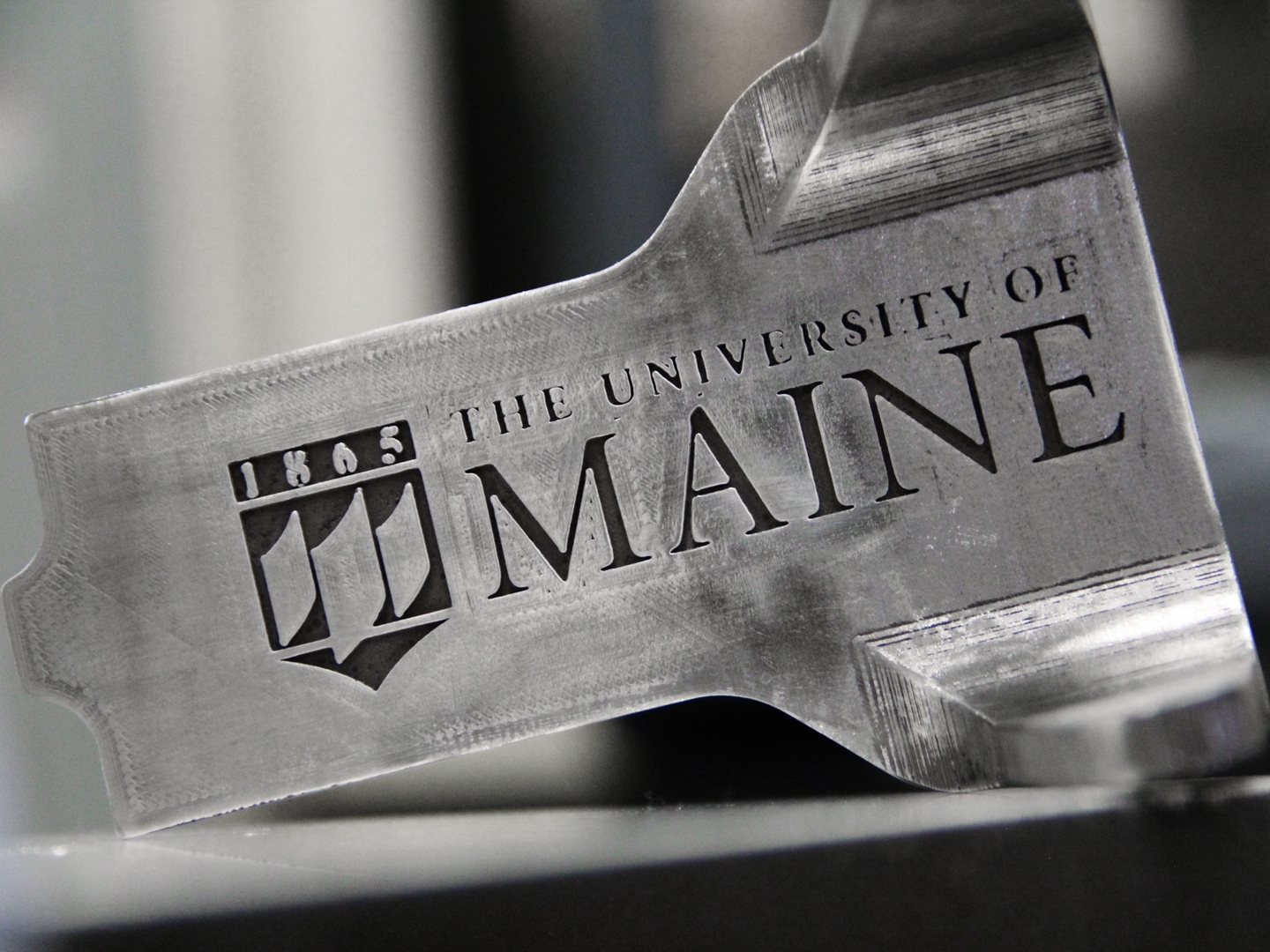
About University of Maine
Based at the Advanced Manufacturing Center (AMC) on the campus of the University of Maine, the Center for Additive Manufacturing of Metals (CAMM) was established as a public-private partnership aimed at helping Maine manufacturers learn about the benefits of additive metal manufacturing technology, as well as workforce development and training and to facilitate the adoption of AMM technology throughout the state.
The challenge
In the last half-decade, the manufacturing sector in Maine has grown dramatically - today it accounts for nearly 10 percent of the state’s total output, with 1,600 firms employing more than 50,000 people.
But as the world of manufacturing becomes increasingly digitized, those firms need to stay up-to-date on the latest technologies and how to use them.
That’s where the Center for Additive Manufacturing of Metals (CAMM) comes in.
Located on the Orono campus of the University of Maine, CAMM houses the state’s first metal 3D printer, and was created for two complementary purposes - to give students hands-on experience with the technology before they enter the workforce and help industries in the state explore and understand the possibilities of metal 3D printing.
Advocating for advanced manufacturing
A prime example of those possibilities came when students went searching for what - at first glance - seemed to be a simple gear.
While acting as advisors to a nearby high school’s FIRST Robotics team, students found that a key component - a ten-tooth gear with a half-inch hex bore - wasn’t available as an off-the-shelf part.
Rather than change their design, the team turned to 3D printing.
Because it eliminates the need for hard tooling, additive manufacturing significantly reduces the lead time and labor costs associated with traditional manufacturing, the team was able to print and install the gear in just weeks, and keep their build on schedule.
Other students have used the system to investigate how different shapes affect the shrink rate for sintered parts, and for capstone projects that have included the creation of custom-designed, completely 3D-printed Stirling engine and the recreation of parts from an early-1900s steam locomotive.
CAMM’s industry partners, meanwhile, have been able to reap similar benefits - companies like Hussey Seating and Pratt and Whitney have worked closely with the center to design and fabricate custom-designed parts in small quantities at lower cost than traditional parts.
Why Desktop Metal?
Though they considered a number of 3D printing technologies, CAMM staff chose the Studio System in part because it represented a largely untapped area of additive manufacturing research.
Unlike laser-based systems, which are widely studied at institutions around the globe, the Studio System offered CAMM researchers the unique ability to “open the hood” to study the process in detail, and are working to publish their results.
Other factors in the decision were the system’s office-friendly design and price.
Laser-based systems rely on powerful lasers to fuse metal powders and require massive upfront investments - often $1 million or more for equipment and facilities.
The Studio System, by comparison, uses no loose powders or dangerous lasers, and instead relies on a technology called Bound Metal Deposition™ in which rods of metal powder and binders are heated and extruded to shape a part.