3D printed flexures
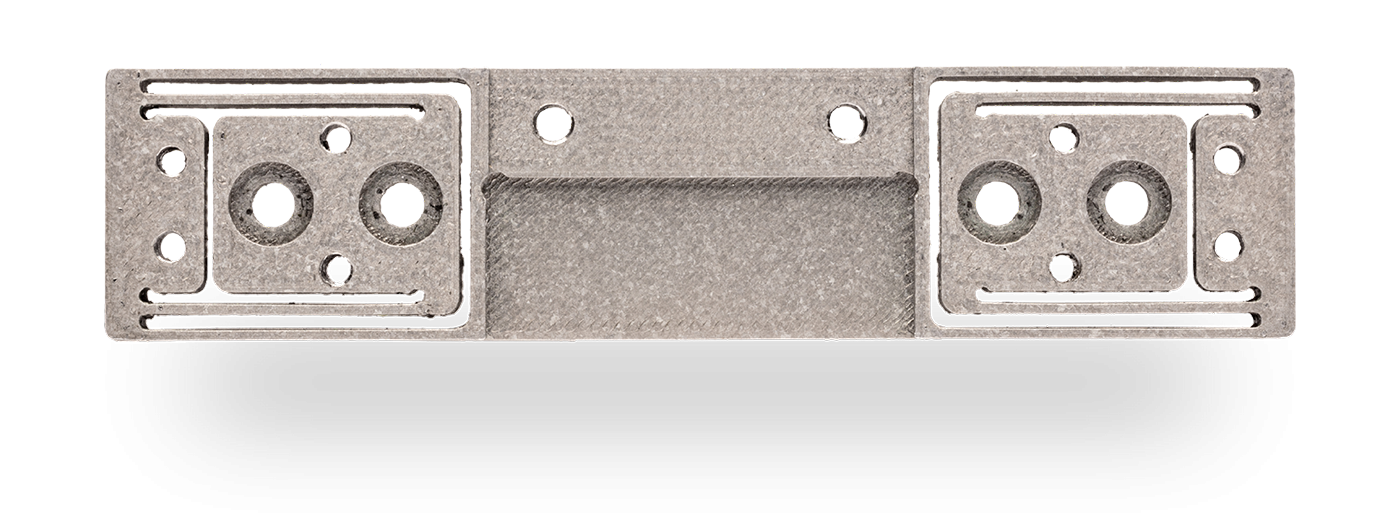
Background
Flexures are used for precise adjustment in devices like optical stages and actuating clamps—such as collets and compliant features—where minimizing backlash is critical. Based on their geometric complexity, fine features, and susceptibility to vibration, flexure designs are challenging to achieve using traditional manufacturing methods.
Challenge
Typically, flexures require comprehensive, multi-step manufacturing processes—including wire EDM, water jet, brazing, and combinations thereof—to achieve the desired geometry. Often, each additional degree of freedom within a flexural mechanism requires its own manufacturing considerations (different setups, multiple parts, different processes, attaching multiple stages). These technical and procedural complexities contribute to a challenging and time-consuming workflow to achieve the required compliance or adjustment.
Solution
The Studio System provides the design flexibility needed for producing complex flexures without the cumulative manufacturing processes required with traditional methods. Rather than designing a part for expensive, multi-step manufacturing processes, and spending hours—or even days—producing custom workholding fixtures, engineers and designers can now print fine, complex features directly. This introduces new capabilities for product development through on-demand manufacturing.