Metal 3D printing for tooling
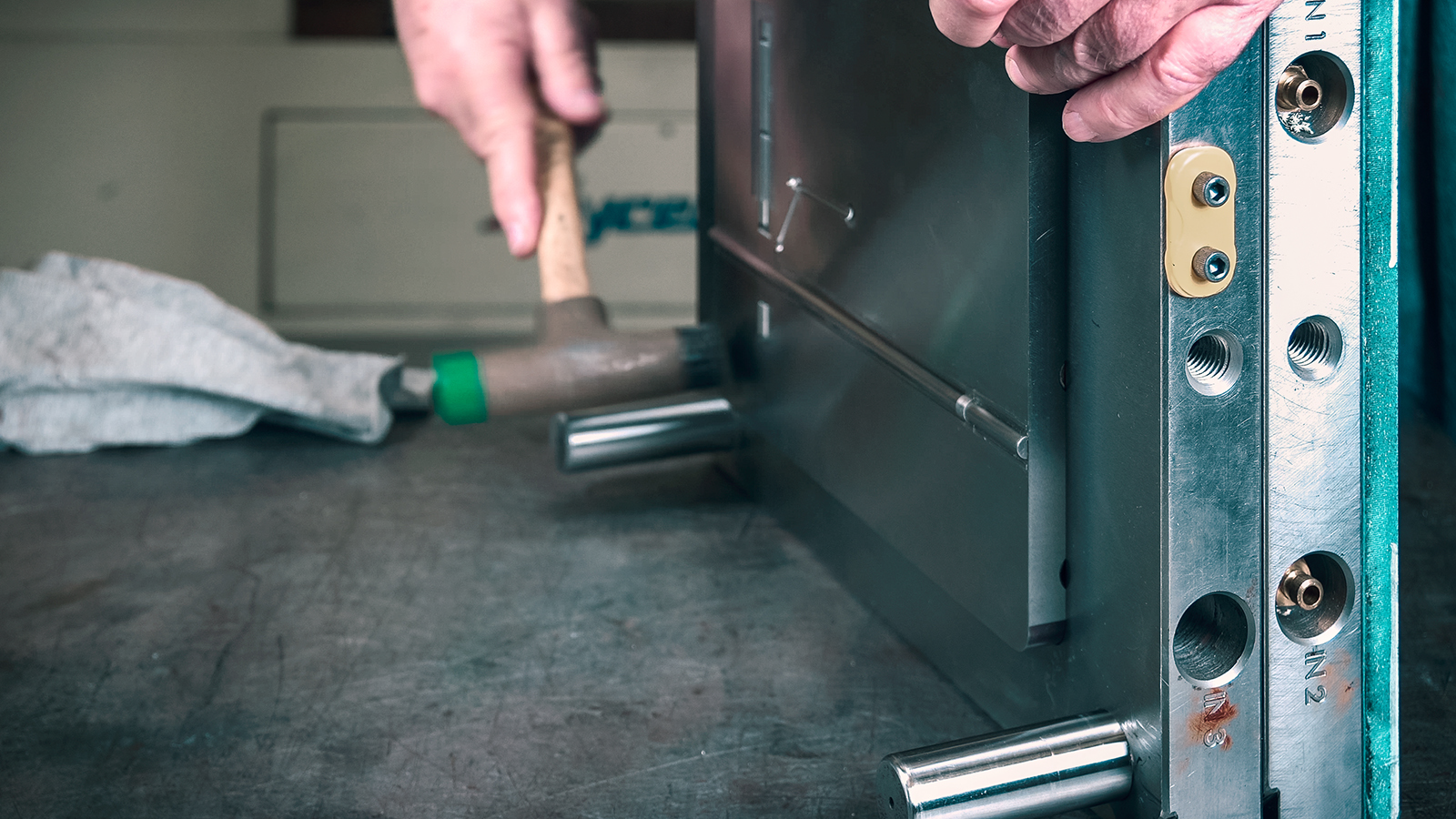
Tooling is a general term for components used in various manufacturing processes—including injection molding, extrusion, stamping, casting, cutting, and assembly. A single tooling mechanism may consist of several complex parts, and the production of tooling can be a complicated process that is both time-consuming and expensive.
The process of tool-making is expensive and time-consuming. It can be tedious due to complex geometries and part requirements, and it might involve the assembly of multiple parts. If a tool breaks or the design changes, the entire production schedule can be delayed—or stopped completely—until a replacement part is available.
It’s common for tooling components—such as mold cavity inserts, extrusion dies, end-effectors, stamps, and cutting inserts—to be produced in low volume, involve complex geometries, and require tool steels whose hardness makes them difficult to machine. Each of these factors can have a significant impact on overall production cost and lead time. In the automotive industry, for example, the production of tooling components can result in hundreds of millions of dollars spent and years added to the development timeline. Additionally, third-party tool-makers are limited by strict deadlines and leave little to no room for effective design iteration.
In-house metal 3D printing makes it possible to produce tooling faster and at a lower cost-per-part. With the Studio System, manufacturers will be able to print in tool steels that are difficult to machine, allowing for prototyping in the same material used in final production.
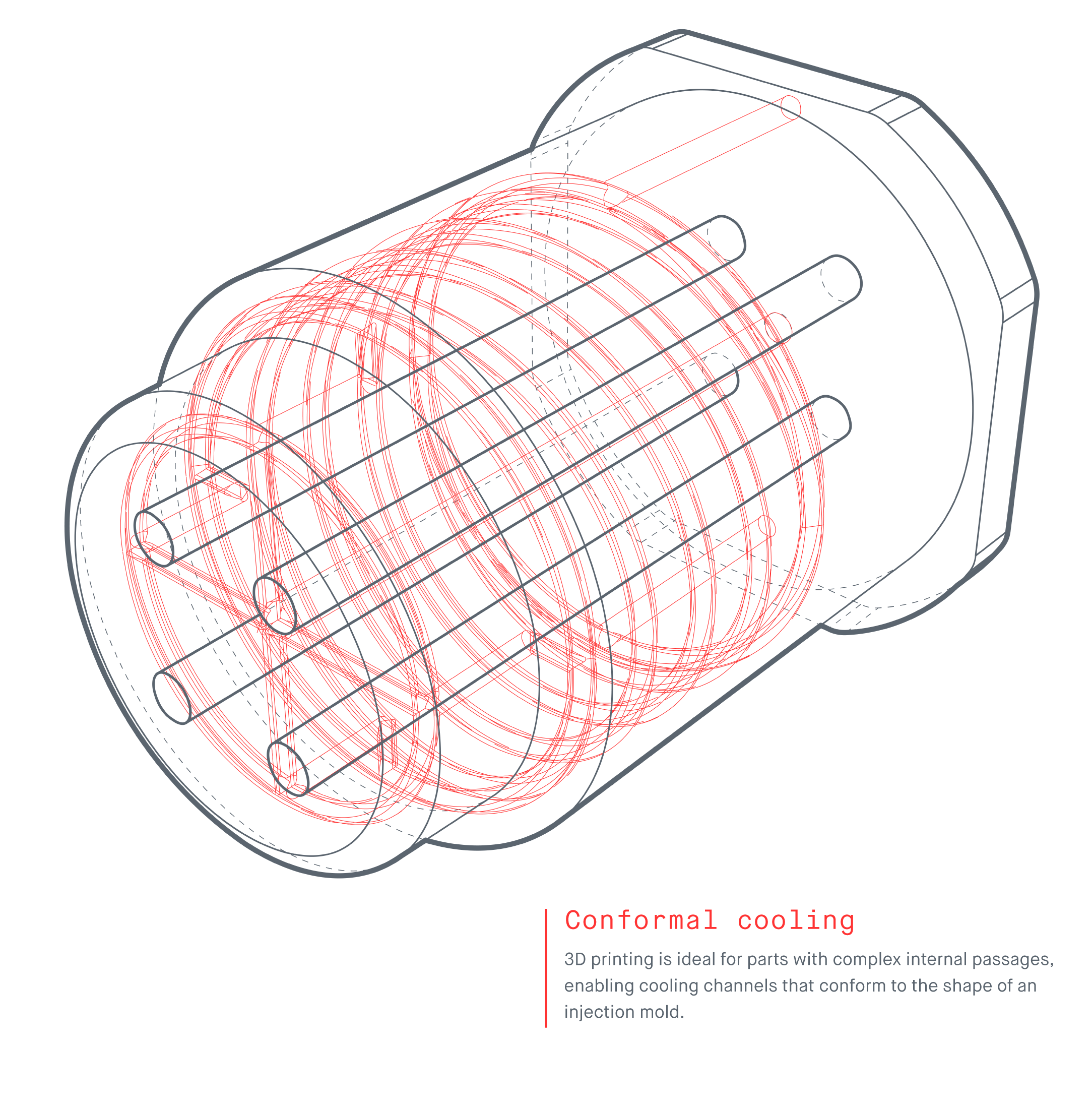
Injection molds with conformal cooling channels
The benefits of metal 3D printing for tooling applications are seen with the production of custom injection molds. Mold-making firms who design and build complex injection molds experience first-hand the challenges of traditional manufacturing processes for achieving complex designs.
In applications like injection molding and thermoforming, the process of cooling the newly molded part is critical to quality assurance and can account for about 95% of the cycle time. Once injected into the mold, the plastic must be rapidly and uniformly cooled to ensure part quality. Mold-makers design internal channels throughout the mold cavity through which coolant will pass immediately after the injection. Non-uniform cooling may result in weak spots—or even a failed injection cycle.
Due to the limitations of traditional manufacturing methods, cooling channels are often limited to straight lines. The more intricate the geometry, the more difficult it is to achieve. Conformal cooling channels—that is, channels that closely adhere to the shape of the injected part—are the best way to achieve uniform cooling. This reduces or eliminates hot spots and increases coolant flow turbulence—resulting in better part quality and an overall reduction in cost-per-part.
Parts with complex designs and internal structures—such as conformal cooling channels for custom molds—are ideally suited for additive manufacturing where fabrication time and cost-per-part are not necessarily dependent on design complexity.
Conformal jigs and fixtures are designed to adhere to the shape of the part that is being manufactured while enabling an even distribution of the clamping forces. Often, this includes intricate designs that are difficult—or nearly impossible—to machine.
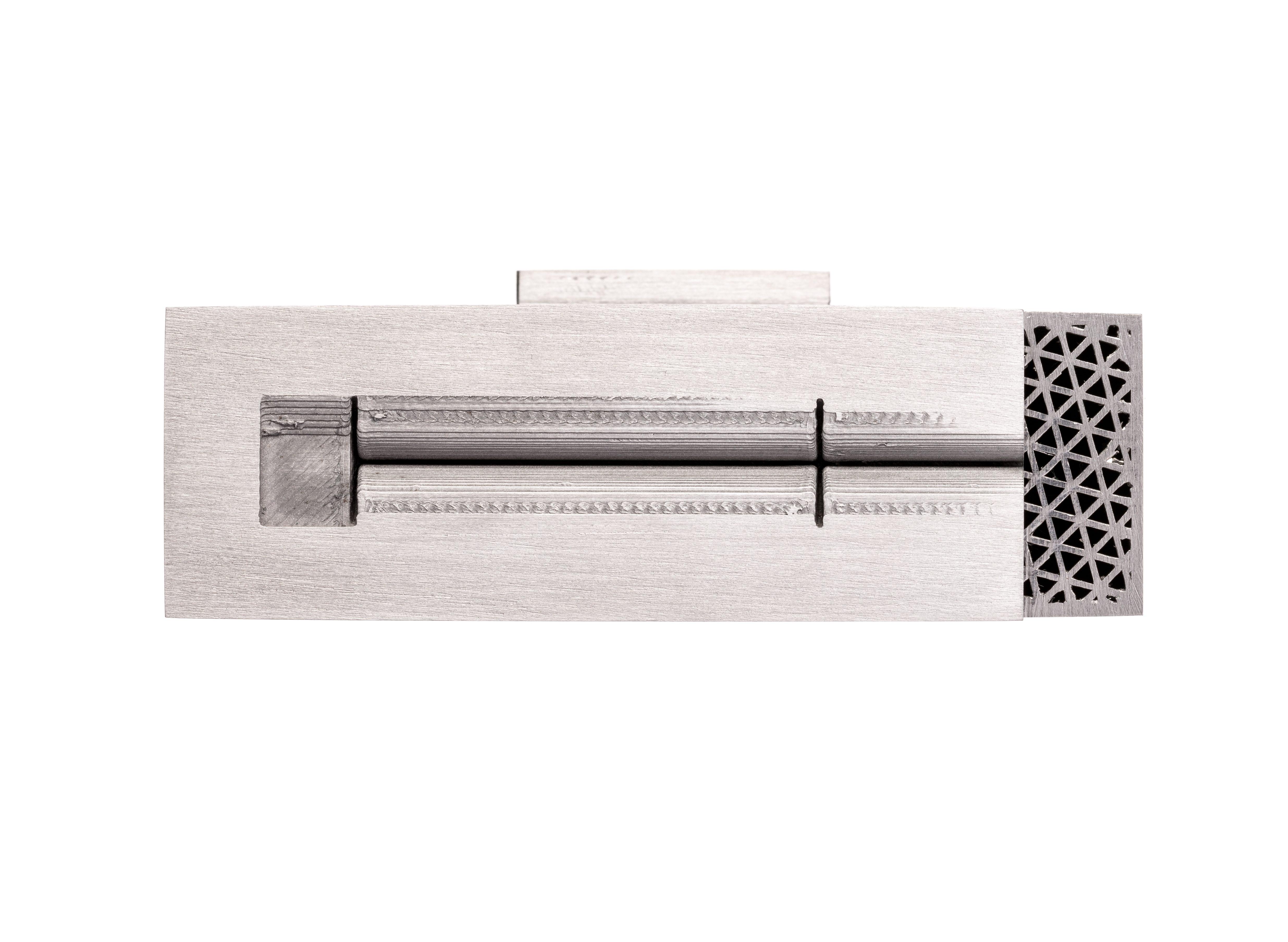
Alternative metal 3D printing methods, such as laser-based systems, deliver the benefits of additive manufacturing, but their initial cost and operational complexity make them inaccessible for most small to mid-sized engineering teams.
Bringing the benefits of metal 3D printing in-house with the Studio System enables the rapid prototyping and on-demand production of custom tools—as well as the ability to print in tool steels that are difficult to machine. The ability to make replacement parts quickly reduces overall lead time and costs associated with third-party manufacturing.
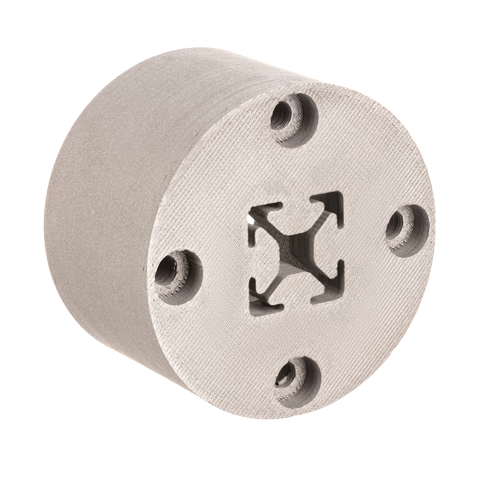
Extrusion Die
Beyond the design flexibility and ease with which 3D printing solutions can achieve complex internal structures, the implications this has on part cost are significant. This is demonstrated in the an evaluation of the fabrication process of an extrusion die, shown below. Printed in 17-4 PH stainless steel, the Studio System was able to achieve complex extrusion profiles—specifically, a hexagonal shape through which material will be injected.
Metal vs. Plastic
While there have been advances in plastics, the vast majority of tooling will perform better if made out of metal. Generally, tooling is used in environments with high heat and they are often exposed to abrasive chemicals and media. Plastic parts will distort and warp in these environments and, after repeated use, they will begin to wear. The lifetime of metal tooling is much greater than that of plastic. Additionally, it is much stronger and stiffer than plastic, so for tooling applications in which a significant force will be applied, metal tools are required to prevent deflection and preserve repeatability.
The Studio System is capable of printing some of the most difficult to manufacture materials that are desirable for tooling—H13 tool steel, Inconel 625, 17-4 PH stainless steel—and can produce tools quickly and affordably.
For tool-makers, leveraging the benefits of metal 3D printing allows them to offer more advanced services that result in higher-quality parts. Bringing this technology in-house makes it possible to win more bids with a more competitive timeline and reduced cost-per-part as a result of the on-demand production of tooling components.