Five Steps to Evaluate Your Site for Metal 3D Printing
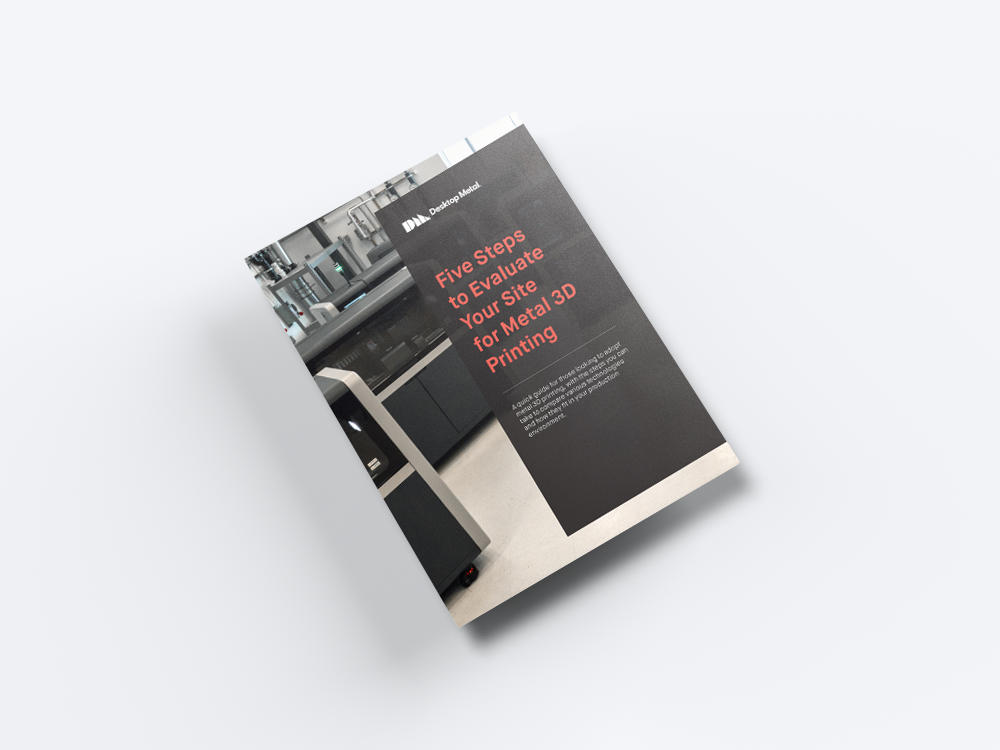
Metal 3D printing continues to gain adoption, allowing businesses to create complex and highly precise metal parts that would be difficult or impossible to produce with traditional production methods. While these additive manufacturing systems aim to be another tool in the manufacturers’ toolbox, the facility requirements of “metal 3D printing” may require some consideration. Usually, customers are surprised how easy it is to integrate into existing site and operations.
First and foremost, the type of metal 3D printing technology you’re looking to adopt will drive your facility considerations. The Bound Metal Deposition technology of the Desktop Metal Studio System™, for example, can be easily installed in just about any existing office or lab space with minimal facilities updates. In contrast, laser powder bed fusion processes, for example, require additional consideration for handling fine loose powder such as explosionproof vacuums, sieving stations, and filter flooding stations that add up to high investment and come with new environmental, health, and safety requirements. Facilities requirements for metal 3D printing technologies like binder jetting with the Desktop Metal Shop System™ fall somewhere in between.
Desktop Metal offers an extensive Knowledge Base including a complete Site Readiness Guide for each of our systems, and our experienced Customer Service team can work with adopters to ensure their layout is functional. Exactly how to best prepare your facility will depend on many variables, including your applications, building, and local codes and ordinances. However, if you’re new to metal additive manufacturing and looking to adopt this technology, we’ve compiled some considerations below about how to evaluate your site for metal 3D printing.
- Determine your equipment and space needs
- Know your facility requirements
- Understand your feedstock and how to handle it
- Identify your operator burden, resources, and gaps
- Make an installation and maintenance plan