Metal 3D printing for the automotive industry
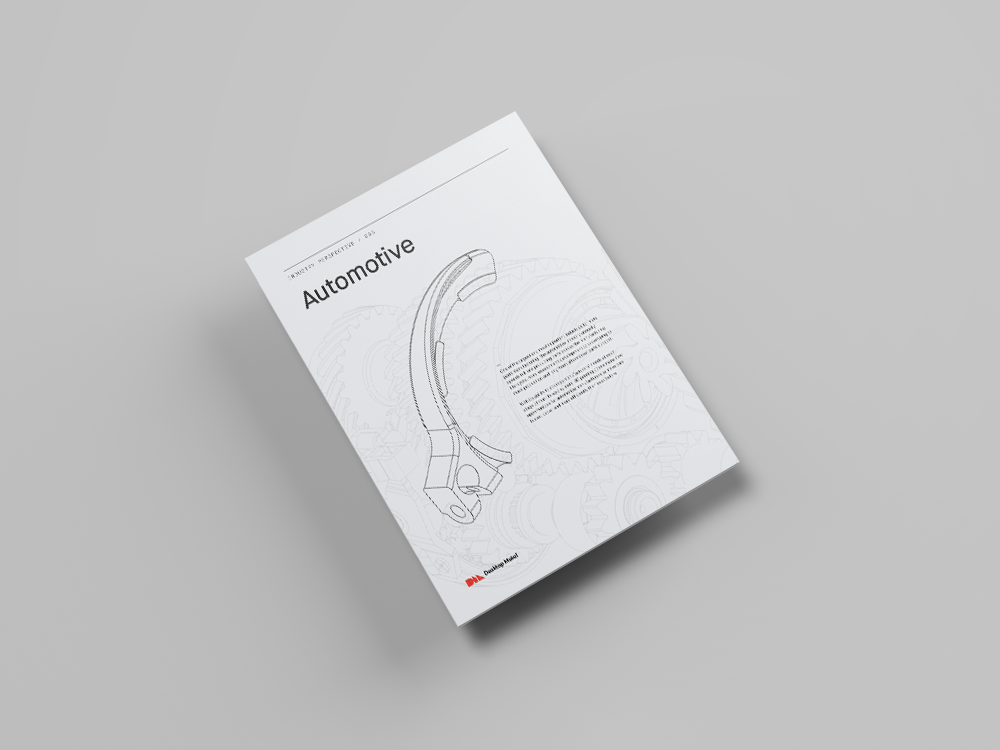
About the Automotive industry
One of the largest and most important industries for metal parts manufacturing, the automotive industry annually spends trillions producing parts across the manufacturing lifecycle, from research and development to prototyping to mass production and long-term aftermarket parts support.
With its ability to address manufacturers’ needs at each stage of that lifecycle, metal 3D printing opens many new opportunities for automotive manufacturers to make cars faster, better and more efficiently than ever before.
The Challenge
The challenges automotive manufacturers face begin with the often-lengthy - three to five years is common - research and development phase for new models. That long timeline means manufacturers must make decisions based on what they believe the market will look like years in the future.
When vehicles do enter mass production, car makers must take on the monumental task of preparing manufacturing lines to produce thousands of parts. That process involves tooling and programming thousands of machines, developing a wide range of manufacturing processes and more,
But it’s not limited to auto manufacturers - hundreds of Tier 1, 2 and 3 suppliers must also ramp up production lines, all while remaining flexible enough to deal with designs that may change, and specific changes made for different markets.
Finally, cars often remain on the road for 20 years or more, meaning manufacturers must deal with the complex and expensive proposition of providing spare parts for those vehicles. Many of those parts may be in such low demand that manufacturers can no longer justify the cost of producing them, leaving customers to search through scrapyards to find rare parts or purchase low-quality, third party parts.
The Solution
Using metal 3D printing, engineers can dramatically reduce portions of the long research and development timeline, leading to a faster time to market. By speeding up research and development, engineers also have more time to iterate on and optimize designs, leading to improvements in fuel efficiency, performance benefits and overall cost savings.
With the ability to quickly produce custom fixtures and tooling that would otherwise be prohibitively expensive, additive technology makes it easy for manufacturers to optimize production lines.
The technology can also make production lines more flexible. As design changes are made, manufacturers may have to produce new parts for vehicles that may be produced in relatively low numbers. Rather than commit to the time and expense of creating complex tooling or long lead times for third-party suppliers, manufacturers can simply print the parts and keep manufacturing lines running smoothly.
Aftermarket parts - especially those that were once cast - can be easily supported by metal 3D printing. Rather than keeping a huge inventory of tooling for casting parts in large lots of a few thousand, manufacturers can meet the lower demand for parts by printing them on demand as customers order them.
Killacycle Taper Lock Coupling (Shop System)
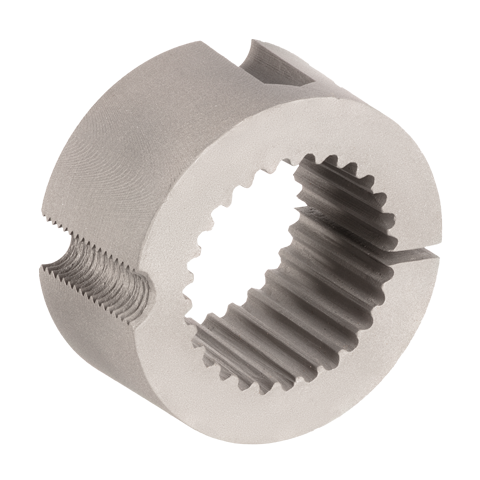
This part is a taper lock coupling designed for a high-end, custom motorcycle.
The Killacycle is an electrically-powered motorcycle built for drag racing. Using the Shop System, engineers were able to design for function rather than for the manufacturing method, allowing them to use a tapered design that would be difficult to manufacture via traditional methods.
The Shop system allowed for a greatly accelerated manufacturing lead time, allowing the team to rapidly iterate on the part.
Shock Absorber Piston (Studio)
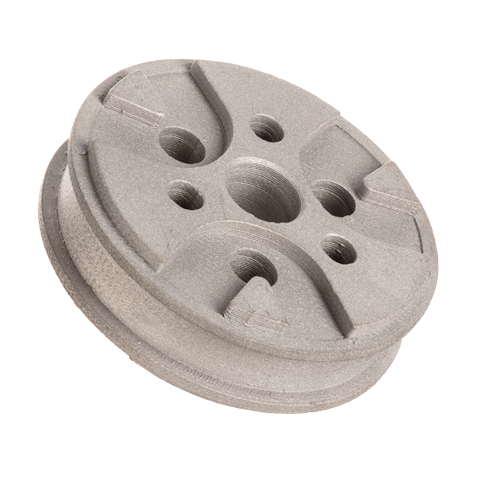
This piston is used in a shock absorber to provide dampening over uneven surfaces.
This part features complex internal channels that are optimized to direct the flow of oil and provide the right level of damping. These internal channels could not be manufactured in any method other than additive manufacturing.
Using the Studio System, engineers were able to quickly produce a number of functional prototypes from 17-4 stainless steel with subtly different geometries and test the performance of each.
That ability, to create multiple iterations of the part while reducing both the cost and development timeline, allowed the team to ultimately identify the piston’s optimum design.
With the final design locked, the parts can be mass-produced using the Shop System.
Gear Shift Knob (Shop)
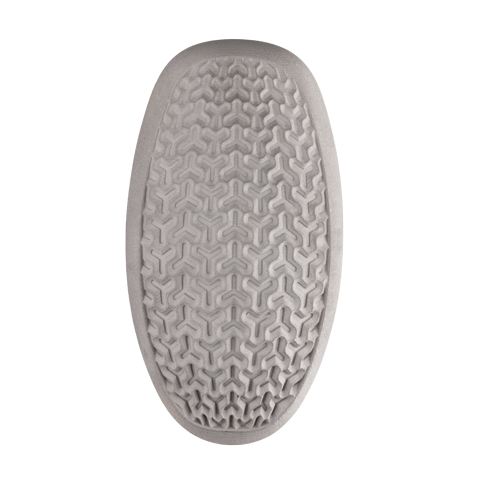
An example of mass customization, this textured gear shift knob can be printed to customer specifications.
On-demand manufacturing of custom knobs is enabled with the Shop System - expanding design flexibility and avoiding warehousing costs.
The short manufacturing lead times allow for many custom knobs to be produced with a variety of different designs. Printing on the Shop System also allows for a dramatic reduction in cost compared to traditional manufacturing methods.
APG Coining Fixture (Studio)
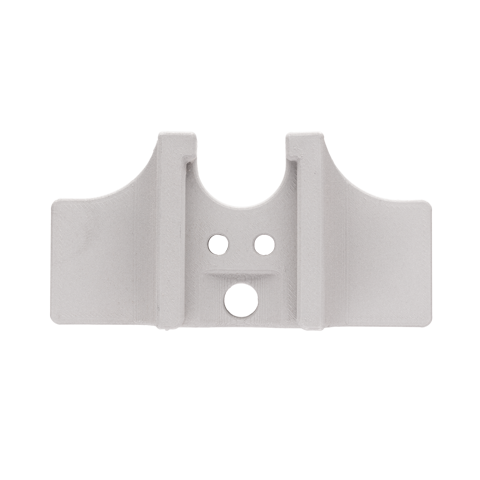
This fixture is used to achieve critical tolerances on metal injection molded (MIM) parts.
Because 3D printing eliminates the design constraints associated with CNC machining, fixtures like this one can be custom-built for each particular application.
And by dramatically reducing the lead time to produce metal parts, APG was able to put this fixture into use in just three days, allowing them to get manufacturing lines running quickly.
Printing these parts with the Studio System eliminates CNC lead time and frees up the machine shop for more critical work.
Mercedes Thermostat Housing (Studio)
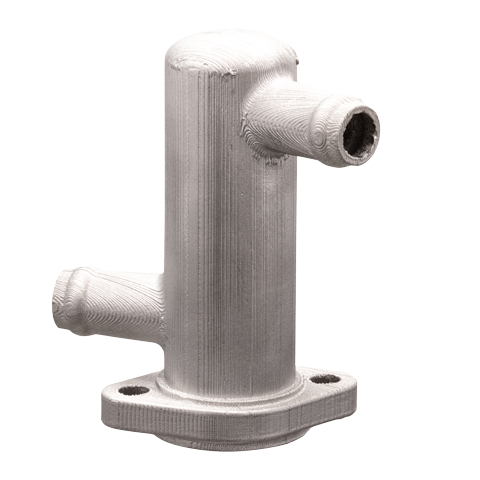
This thermostat housing is part of the cooling system on a vintage Mercedes Benz engine.
This thermostat housing was originally cast, but as demand for replacement parts dwindled, it was discontinued, and the parts became difficult to find.
Attempts to recreate the part have been frustrated by the fact that the molds and tools used to produce it no longer exist, and geometry that is too complex for machining.
Using the Studio System, however, aftermarket parts suppliers can quickly reproduce rare parts like this housing, keeping vintage cars on the road.
Transmission Shift Fork (Studio)
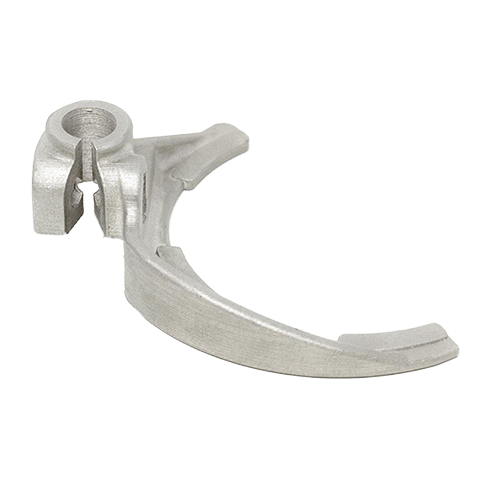
Shift forks are used to move the synchronizers that change the gears in a manual transmission to ensure a proper mesh. This fork is originally cast in high volumes, but when replacement parts are needed in lower volumes casting is not a suitable manufacturing method due to the very high tooling costs and long foundry lead times.
Printing this part greatly simplifies the process of producing replacements, just upload the files, hit print, and a few days later your replacement part is ready to install; greatly reducing the manufacturing lead time, logistical burden, and part cost.