Key Applications for metal 3d printing on the Studio System
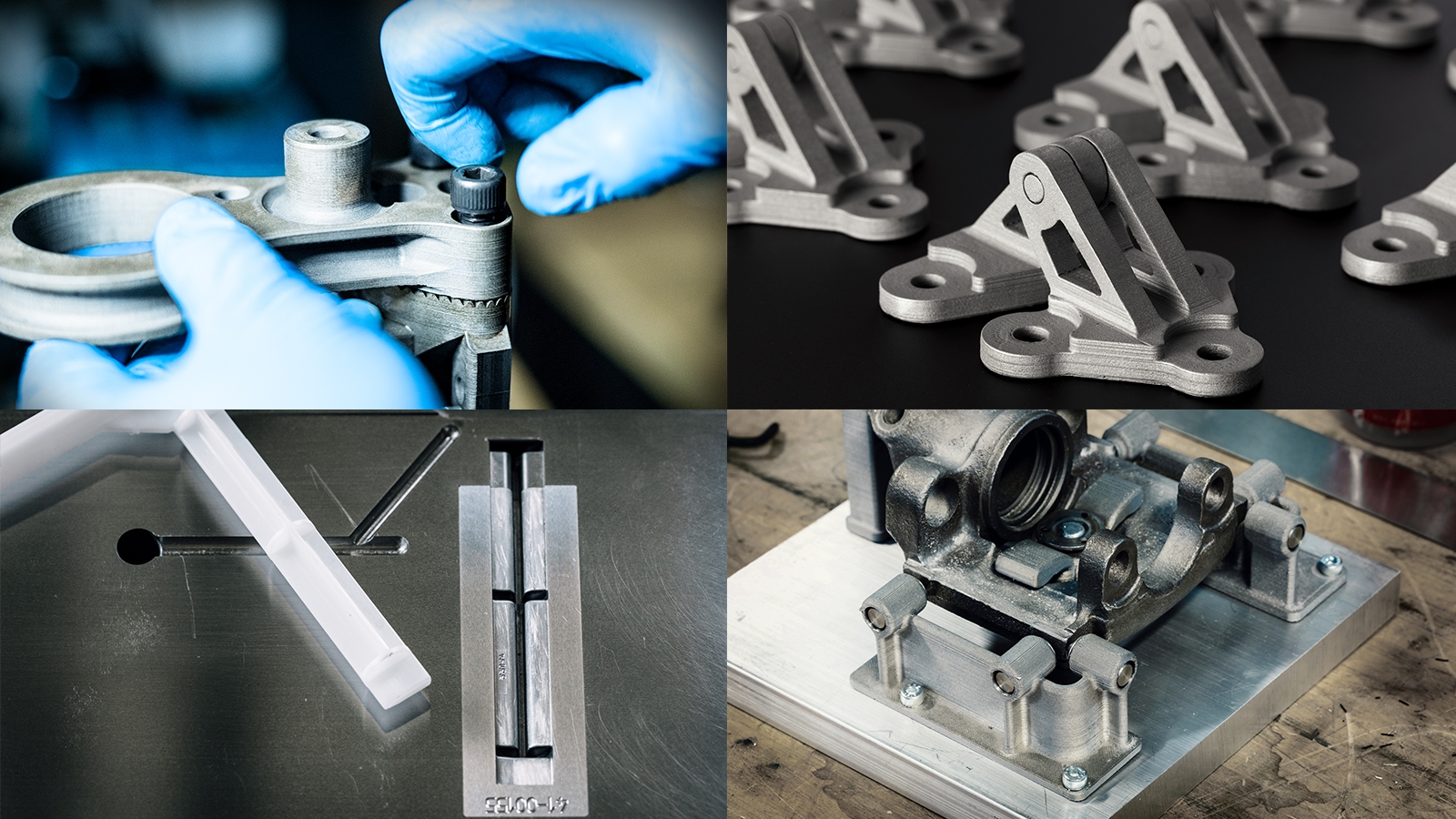
3D printing has been around for decades, but we have yet to see broad adoption of this technology—especially in metal. The industry has promised a manufacturing revolution, but much of the focus has been on low volume production and mostly for plastic parts.
Benefits of AM include the ability to produce parts with complex geometries that are difficult—if not impossible—to achieve otherwise and at a lower cost than traditional manufacturing methods.
Plastic 3D printed parts have a variety of use cases, but applications demanding specific part properties—such as stiffness, strength, corrosion resistance, machinability, or others—require metal. Now, with the increasing accessibility of metal 3D printing, designers and manufacturers are able to produce complex parts quickly using a broad range of materials.
Part Performance
Parts printed with the Studio System have the resolution, accuracy, and surface finish similar to cast parts. Sintered parts meet dimensions within ±0.8% and the parts can be post-processed—by CNC, EDM, grinding, tumbling, media blasting, plating, welding, and heat treating—to achieve critical dimensions and finish.