Material Properties of Binder Jet Parts
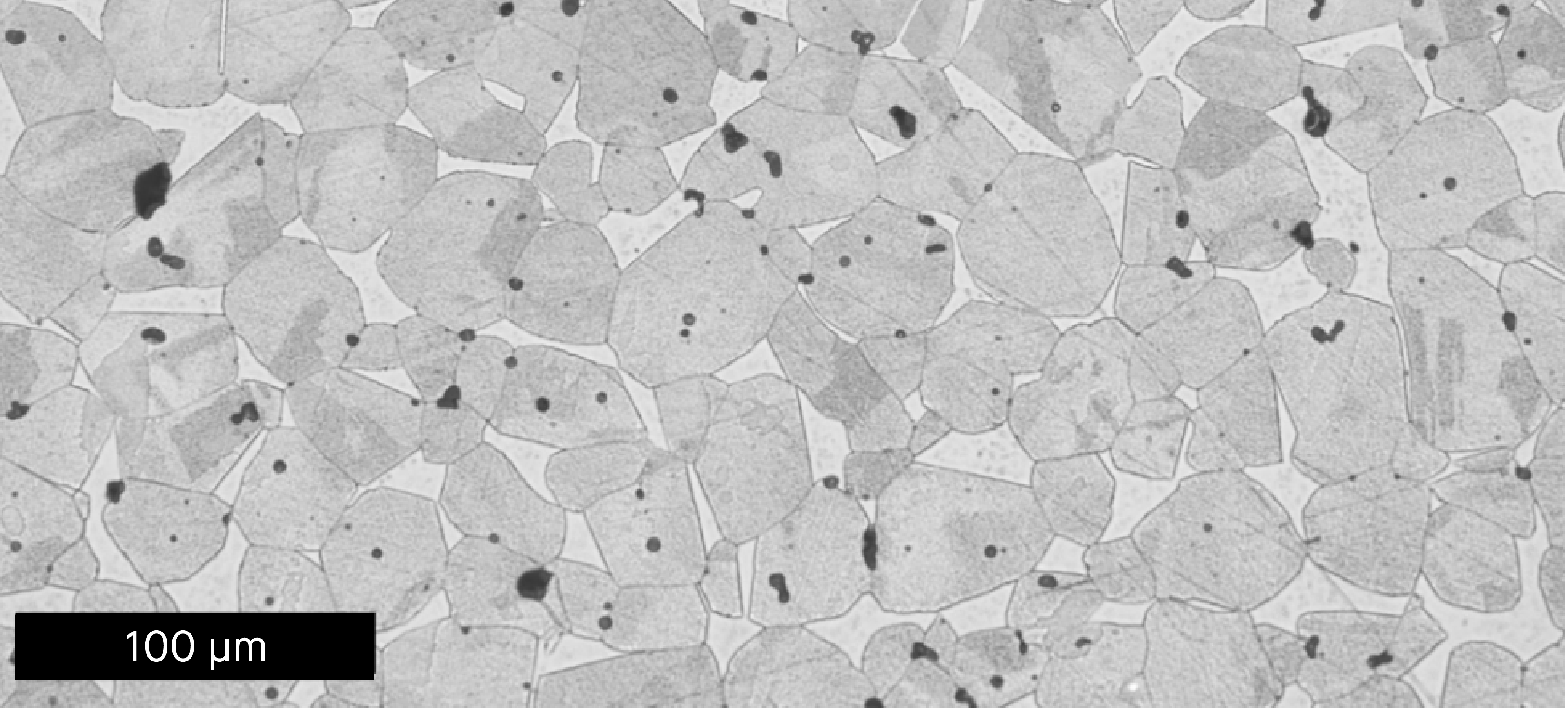
Material Properties of Binder Jet Parts
The binder jet technology at the heart of Desktop Metal’s Shop and Production systems offers a long list of benefits to manufacturers, from the ability to quickly produce complex parts without tooling to creating fine feature details to the ability to print hundreds, or even thousands, of parts in a single print run.
But the material properties of the parts themselves may be the most important.
In key characteristics like strength, ductility, and hardness, both systems print parts that meet or exceed American Society for Testing and Materials (ASTM) and Metal Powder Industries Federation (MPIF) standards, making them ideal for all applications that range from jewelry making to heavy industry.
Achieving those superior properties is possible because the densification technology used by both the Shop and Production systems is built on the foundation of the well-established and well-understood processes used in traditional powder metallurgy and especially those used in metal injection molding (MIM.)
Binder jetting’s MIM foundation is crucial, because it decouples how parts are shaped from their metallurgy. Parts are shaped on the printer using powders that are readily available due their similarities to gas-atomized MIM powders. Parts are then debound and densified during sintering much like MIM parts, freeing manufacturers to create virtually any geometry, with the resulting parts displaying excellent properties.
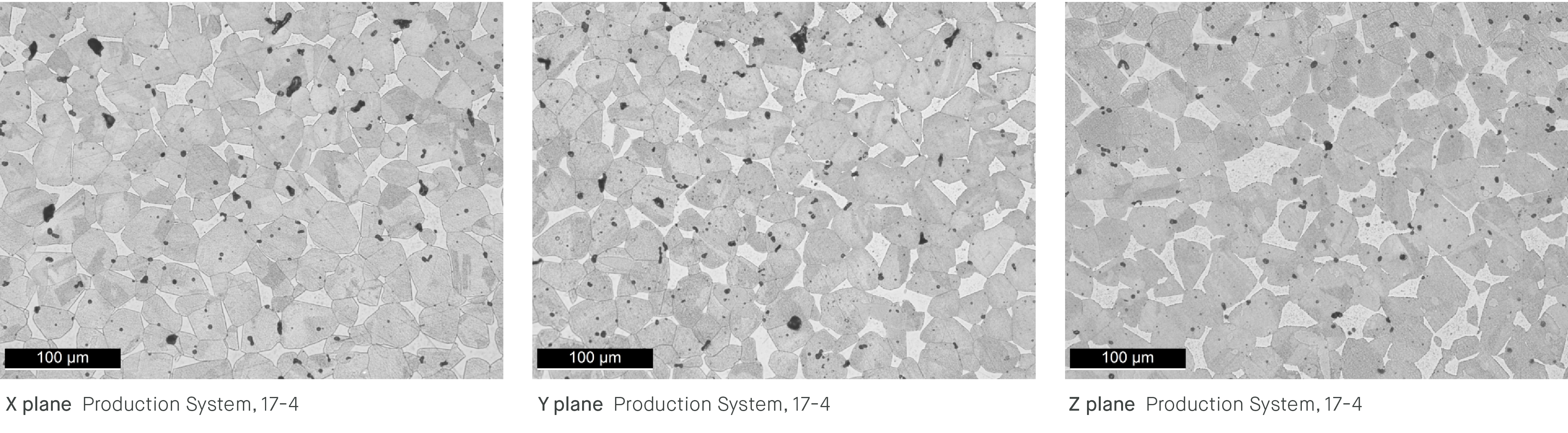
Separation between how parts are formed and their metallurgy is a significant departure from other 3D printing approaches, particularly laser-based metal systems.
Those systems use high-powered lasers to melt metal powder, leaving behind tell-tale artifacts that reveal how a part was formed. The grain structure of powder bed fusion parts often have a grain texture due to the directional solidification of the part. Further, the repeated heating and cooling cycles and the temperature gradient across a part can also dramatically impact parts’ mechanical properties, and give rise to residual stresses within parts that can affect both dimensional and mechanical properties. Alloys that undergo phase transformations (such as the austenite to ferrite transformation in carbon and tool steels) may show particularly high levels of residual stress and distortion if one section of the part is below the transition temperature while another part is above the transition temperature. To counteract this, powder bed fusion parts often require stress relieving processes to alleviate built-up stresses within the part from this nonuniform temperature process.
Binder jet parts, by comparison, are uniformly heated and cooled during sintering, producing a far more homogenous structure and one free of residual stresses. A cross sectioned part reveals a uniform grain size and shape regardless of direction. The mechanical properties in X-Y-Z can be very uniform as shown in the figure below. These bars are tested with machined surfaces.
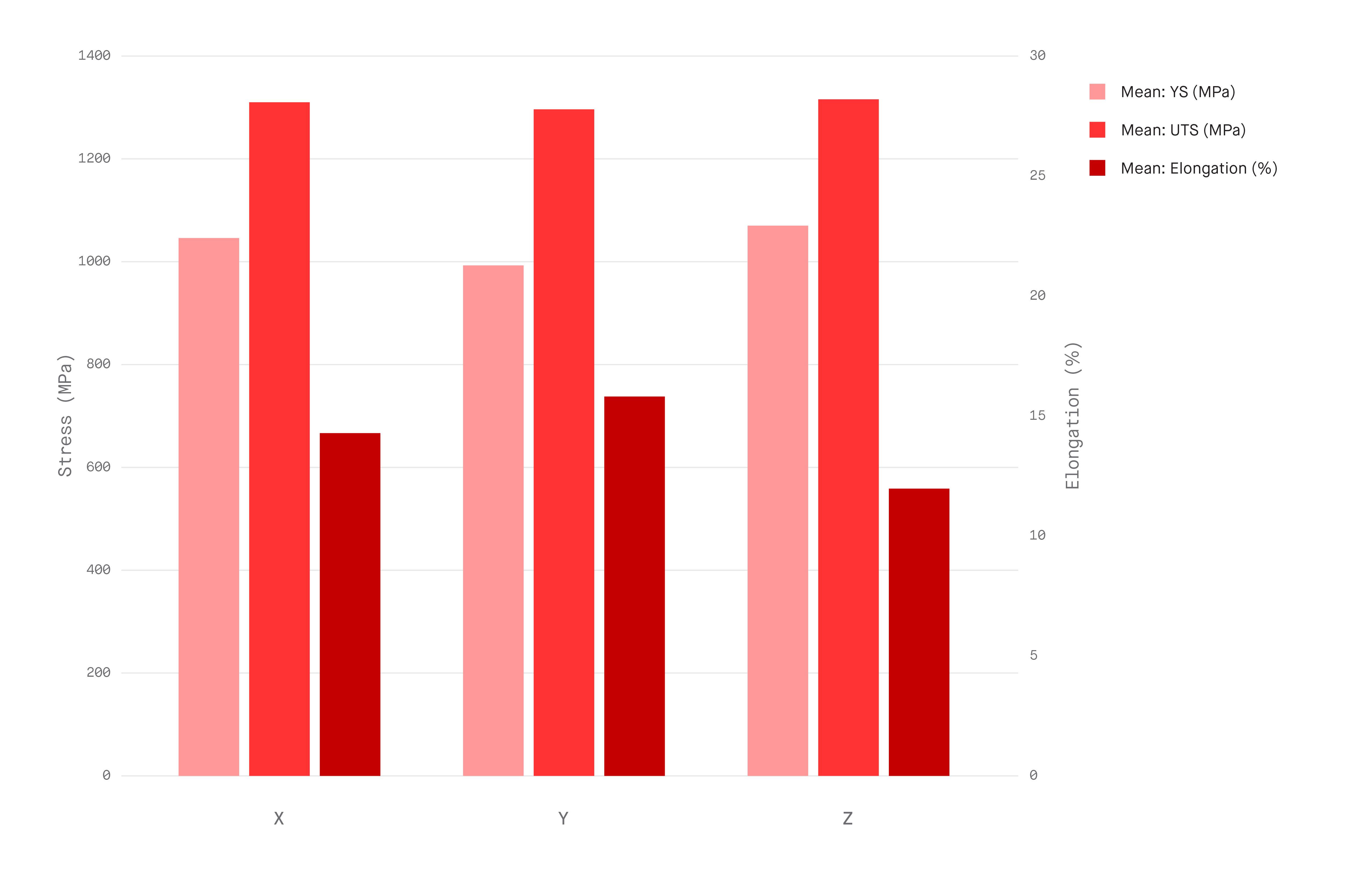
Strength and Ductility
Two key characteristics for end-use parts, strength, and ductility ensure parts will not only withstand the forces they’ll be subject to, but - when desired - will bend or elongate before failing.
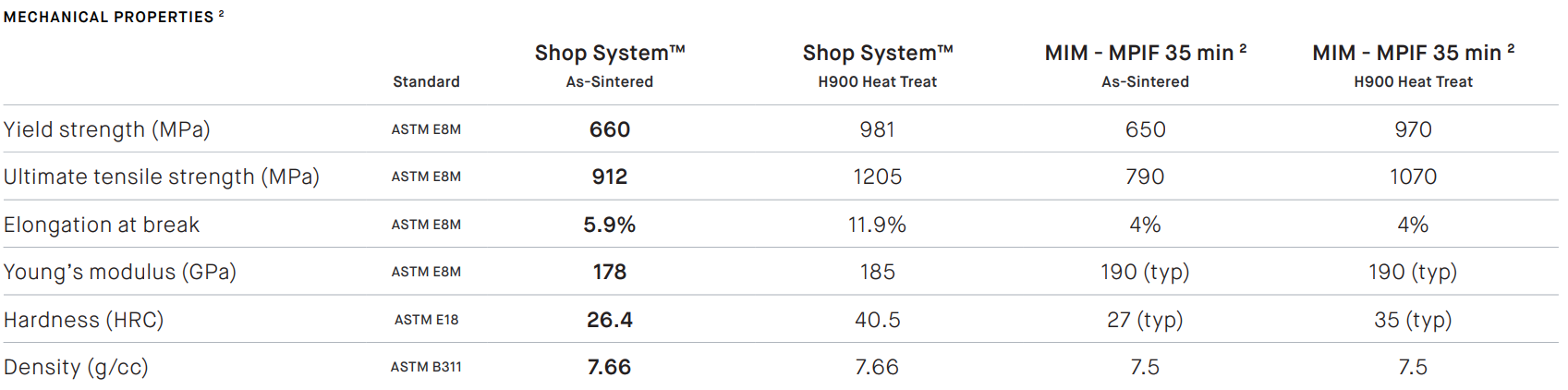
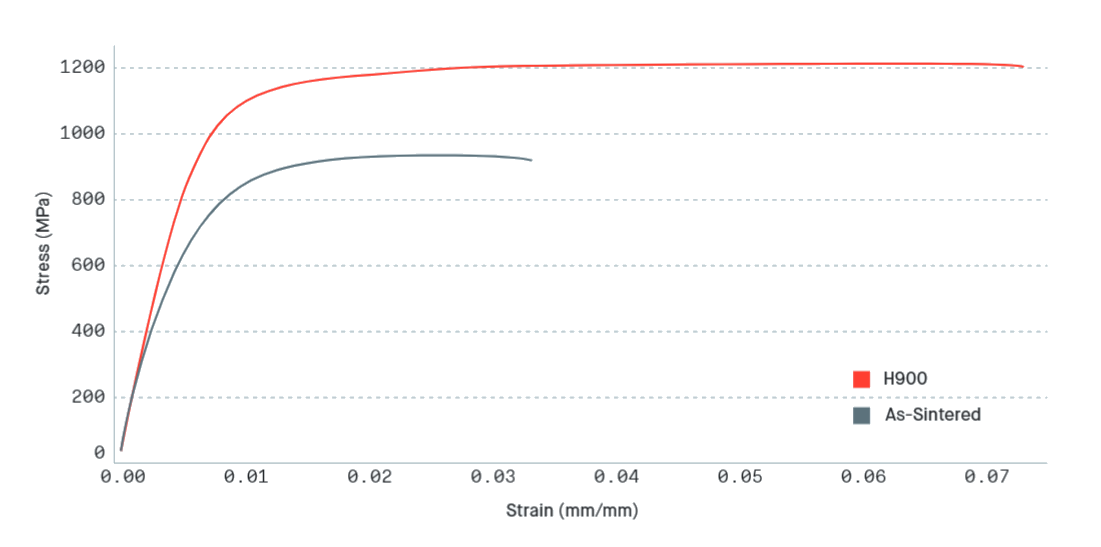
As an example of why both are crucial for metal parts, consider the metal rings in a parachute. Naturally, they need to be strong enough to endure the forces of the parachute opening and the weight of the wearer, but ductility allows the rings to stretch and elongate under larger strains before breaking, meaning the rings can survive under more extreme conditions.
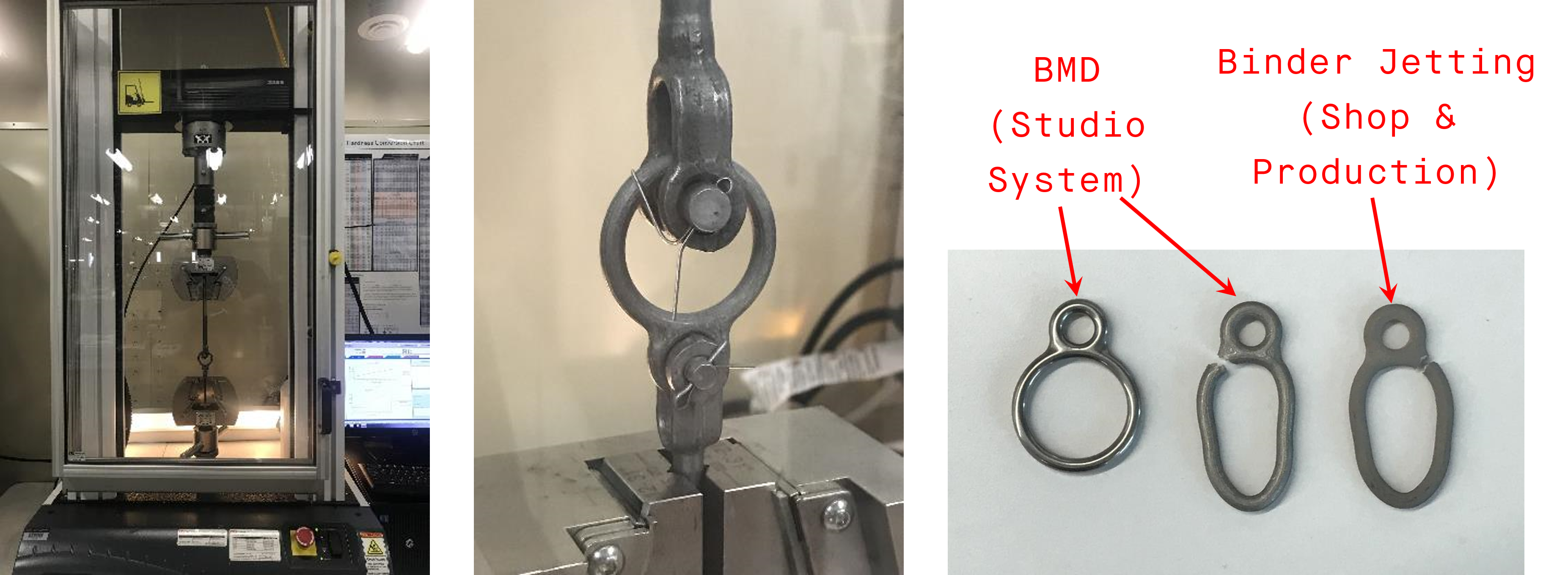
To test the properties of Shop and Production system parts, Desktop Metal scientists printed a wide variety of parts.
Those parts were then sintered using a variety of different furnace architectures. Among the furnaces tested were:
- Metal hotzone furnace - Often the most expensive per-part furnace architecture, but can sometimes yield enhanced densities and corrosion resistance. Results from 2 furnace manufacturers are shown.
- Graphite hotzone furnace - Less costly than metal hotzones, these furnaces offer the flexibility of batch process, and often yield satisfactory properties in MIM 17-4PH, carbon steels and tool steels.
- DM Studio Furnace - The DM Shop System utilizes the affordable DM Studio System furnace
The tests showed that in both yield strength, tensile strength and elongation under strain, binder jetted 17-4PH stainless steel performed well compared to the standard for MIM parts.
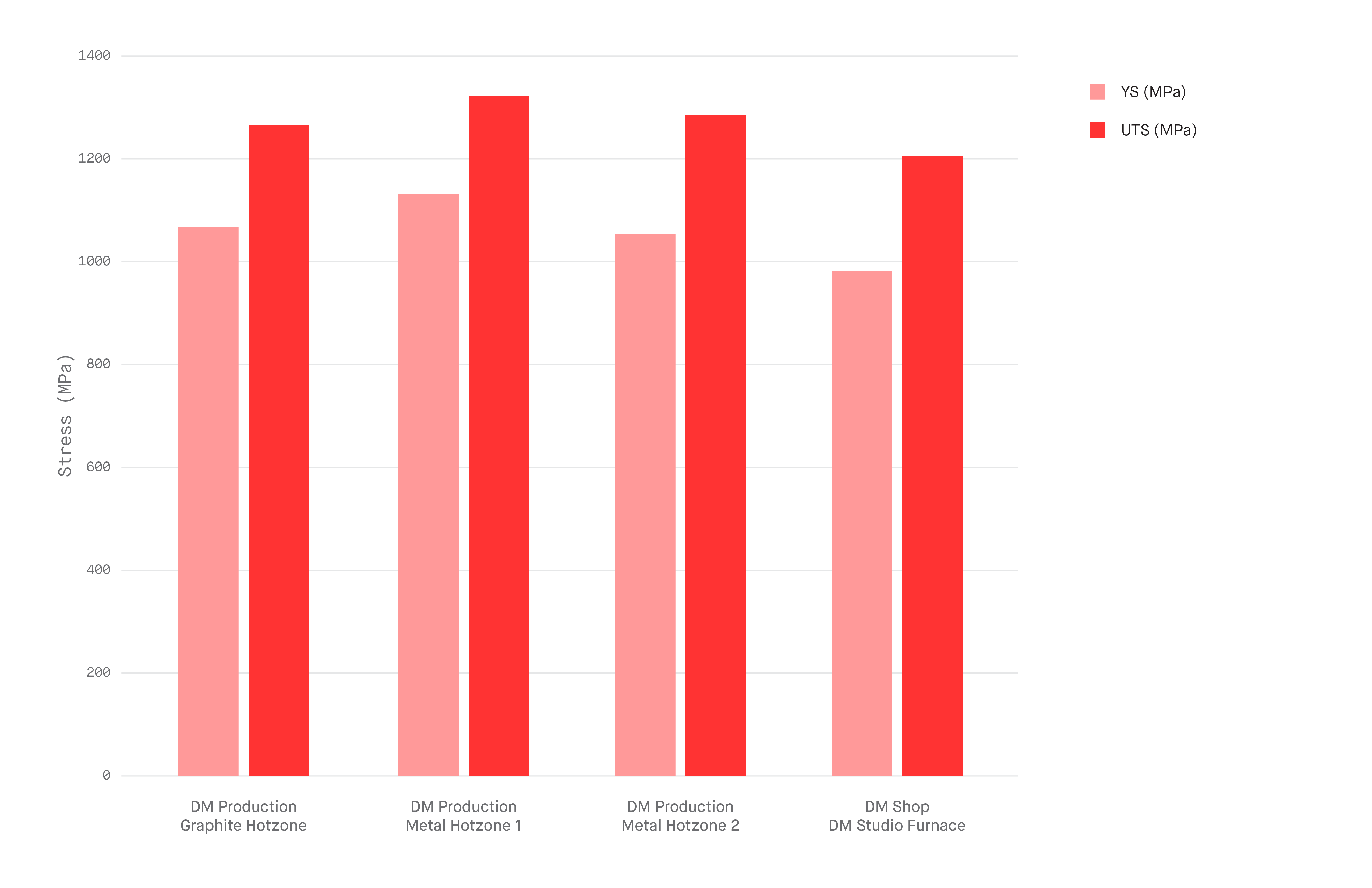
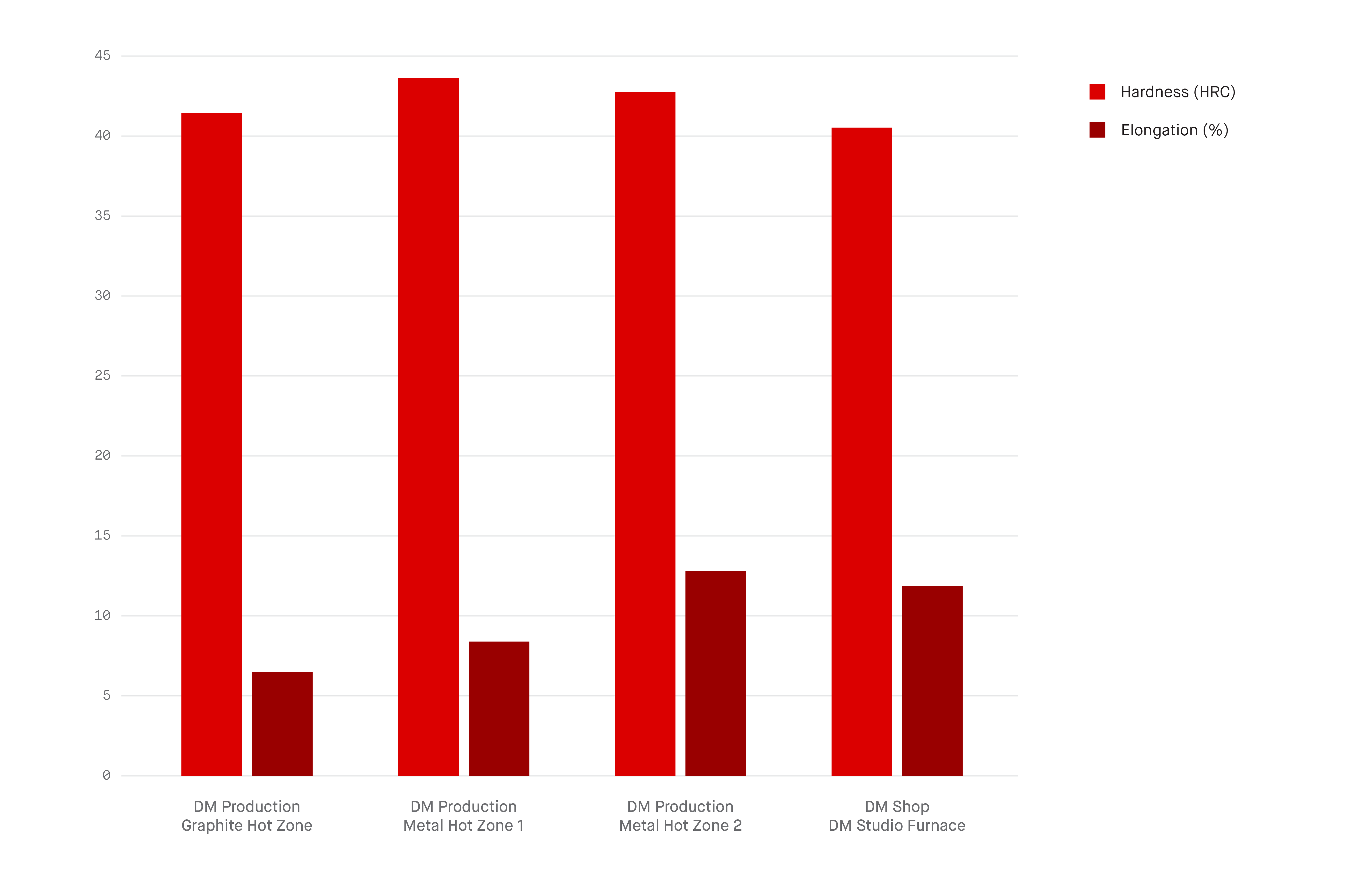
Heat Treating and Hardness
Many applications, particularly manufacturing tooling like mold inserts, sheet metal tooling, and extrusion dies, require parts with high hardness to ensure parts can withstand repeated use.
To achieve high hardness many materials can be heat treated - a process in which parts are heated to a high temperature (solutionized or austenitized), cooled to room temperature (quenched), and then reheated to an intermediate temperature(aged or tempered) . For some materials like 17-4PH, this cycle is produces a microstructure of very fine precipitates within the metal matrix which strengthens and hardens the material after the aging process. For carbon steels , like 4140, the cycle produces a very hard and brittle microstructure called martnesite after the quench operation, and the tempering step is used to slightly reduces the hardness while increasing the toughness by formation of microscopic carbide particles.
More specifically, in 17-4PH, the H900 process is used when high hardness is desired. In this cycle, the material is solution treated at 1038ºC for at least one hour, which dissolves all the copper atoms into the matrix. Then the parts are removed from the furnace and cooled to room temperature in air, the cooling must be fast enough so that no copper precipitates during cooling. Then the parts are reheated or aged at 482ºC (900ºF) for 1 hour; air cooling is sufficient from the aging temp. During aging, finely dispersed microscopic copper-rich precipitates form that harden the part. For thick parts, more aggressive cooling, such as oil quenching can be used to cool the parts from the solution treatment temperature if necessary.
In carbon steels, such as 4140, the material is austenitized at about 855ºC for long enough to dissolve all the carbon into the austenite. For thin parts (6mm thick or less), this can be done in only 20 minutes. Parts are then quenched directly into a suitable cooling medium, which must be either water, oil, or polymer quenchant; cooling in air is not fast enough. Water cooling is usually used only for simple shapes because the cooling rate is so fast it can distort the part. During quenching, the material undergoes a martensitic phase transformation, which hardens the material by the buildup of very high localized stresses within the microstructure. After cooling, the parts will be at their hardest, but also brittle. In the tempering operation parts are reheated to some temperature above room temperature. During tempering, the carbon atoms precipitate to form very small metal-carbide particles and the high local stresses are partially relaxed. The choice of tempering temperature and time affects the size of the precipitates and degree of stress relaxation.
Binder jetted parts can be heat treated just like conventionally manufactured parts, and respond to normal heat treatment processes. The effect in 17-4PH and 4140 heat treatments is shown below. For 17-4PH, the as-sintered hardness (HRC) is shown for sintering in 2 different furnace styles, a graphite hot zone furnace with a 2 bar quench, and a metal hot zone H2 capable furnace. There is a small difference in the as-sintered hardness between the 2 furnaces, but both sets of material show a strong hardening response, and result in very similar hardness after the H900 process. For 4140, the as-sintered hardness is strongly dependent upon the cooling rate and neither furnace can cool fast enough to perform a metallurgical quench, so we show the hardness in three conditions after full annealing, after quenching into a polymer based quenchant and after tempering at 200ºC for 1 hr. The as-quenched hardness is quite good and tempering brings the hardness down to slightly above the MPIF 35 typical spec of 46 HRC.
As with strength and ductility testing, Desktop Metal material scientists tested binder jet parts across a variety of furnace architectures, and the results showed strong responses in every condition.
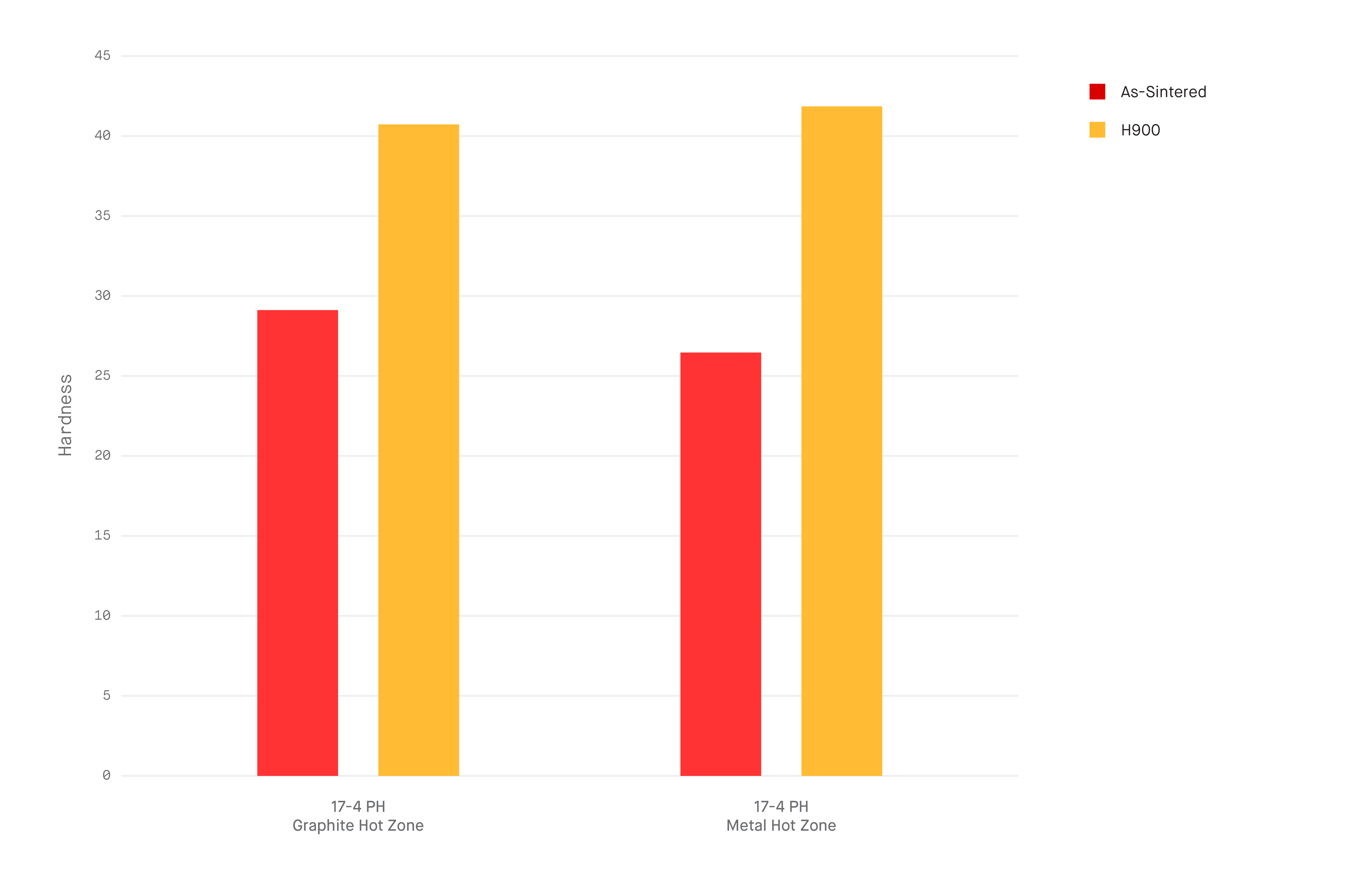
Corrosion Properties and Chemistry
Many metal parts need to operate in harsh and corrosive conditions, so resistance to corrosion is important.
One of the main ways manufacturers increase corrosion is by reducing their carbon content - something the Shop System accomplishes through vacuum sintering.
In tests, binder jetted 17-4PH parts showed lower carbon levels - and hence, greater corrosion resistance - than the 17-4PH standard, and also passed; standard boiling water and copper sulfate corrosion testing.

Density
Binder jet parts also routinely achieve high density, similar to that of typical MIM parts. High densities are essential for end-use parts with a long lifetime.
When tested across a variety of furnace architectures, the microstructure of parts printed on the Shop and Production systems are visually isotropic, and show similar pore distributions, grain sizes, and phase fractions.
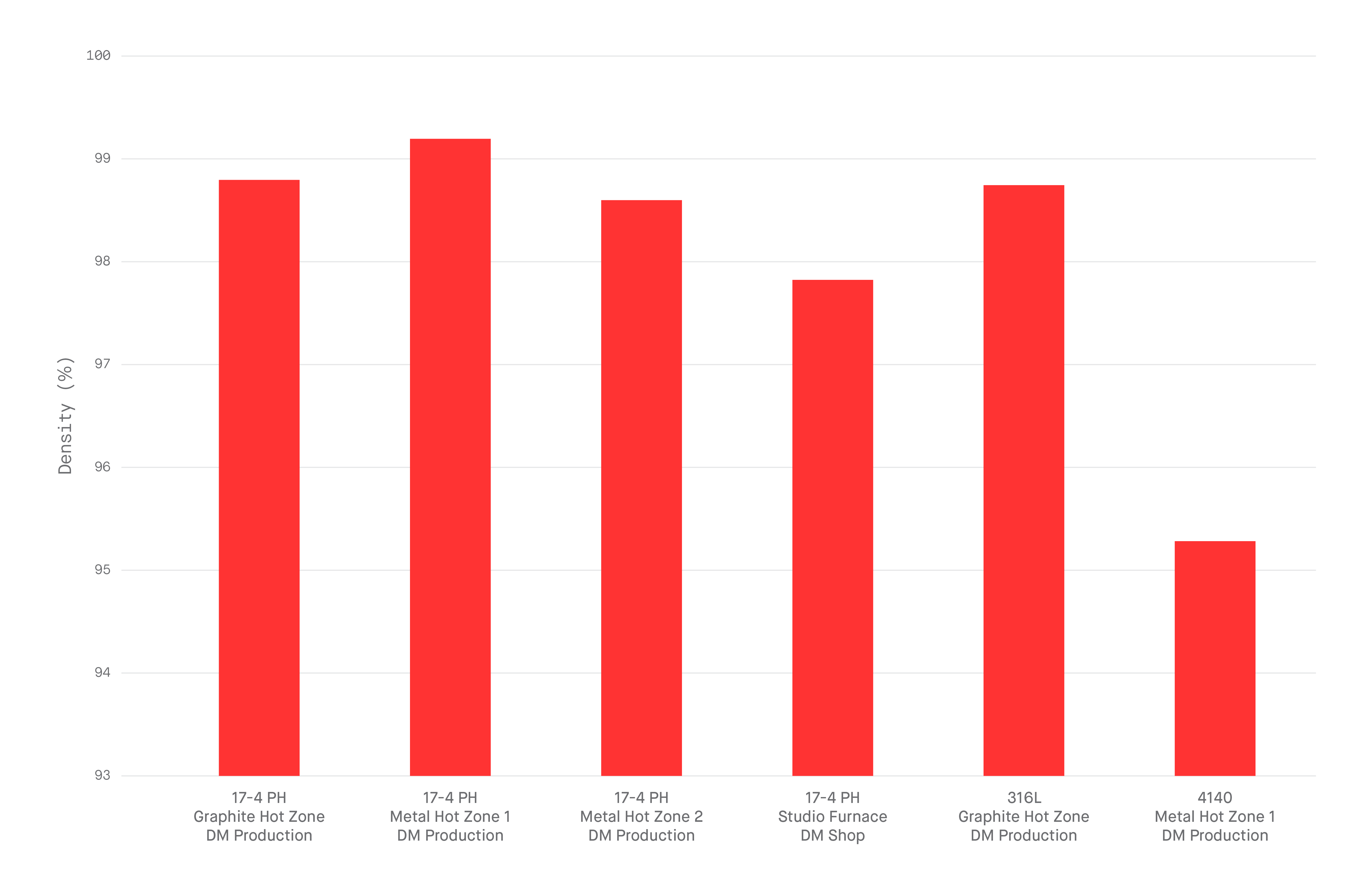
Summary
Overall, the findings are clear - binder jet parts display mechanical and material properties that meet or exceed ASTM/MPIF standards, in line with - and sometimes better than - MIM parts.
When combined with the benefits that come with binder jet printing - high-speed printing, lower per-part costs, tooling-free manufacturing, and more - it is clear that binder jet technology has the potential to leave a lasting mark on the metal manufacturing industry and transform how millions of metal parts are made each year.