Optimizing Metal 3D Prints for Fish Processing Equipment
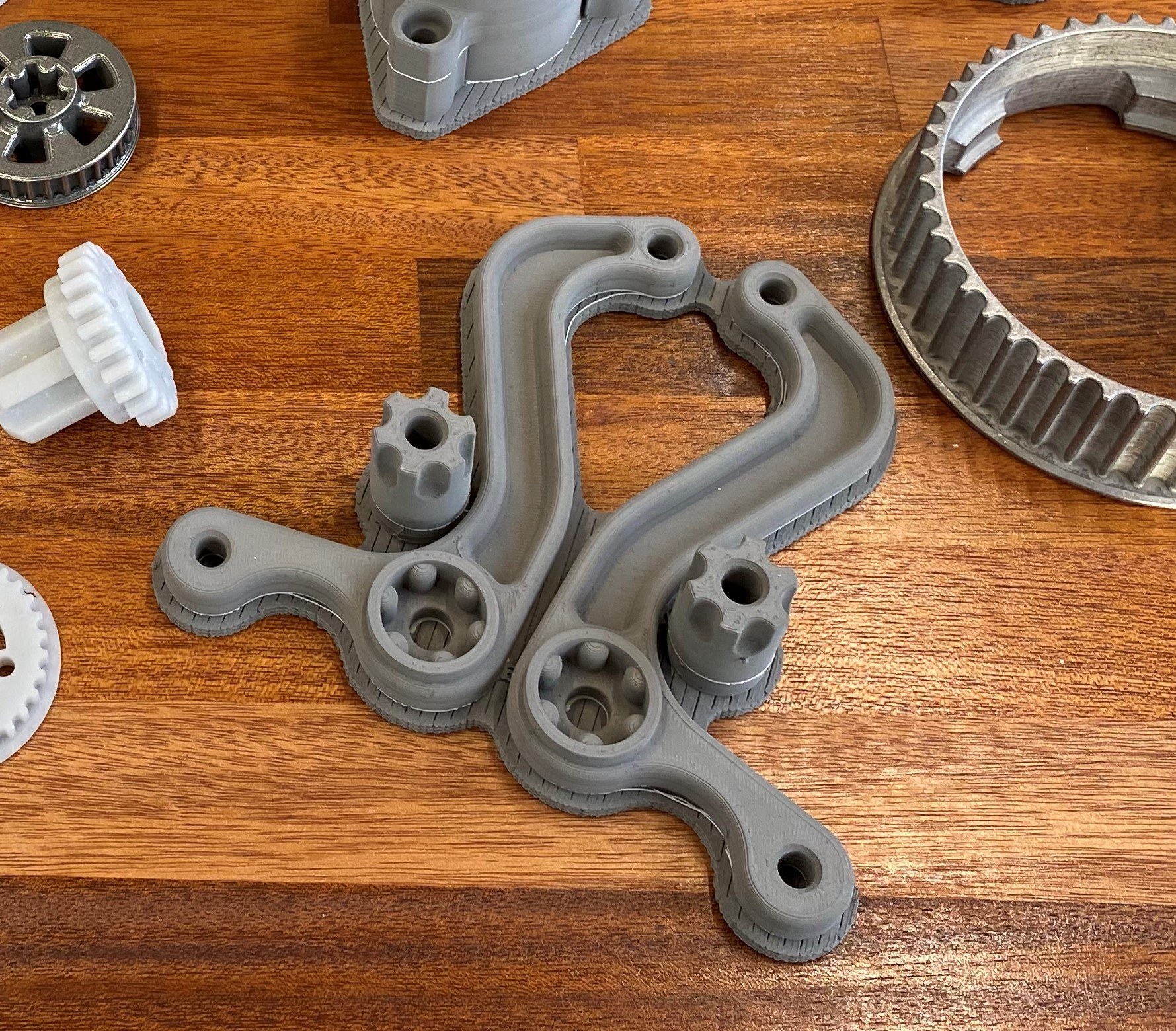
User Expertise: Easy-to-Learn Machine for 3D Printing Success
Curio is a top producer of processing machinery for the heading, filleting, and skinning of fish. The company, which utilizes a fleet of Desktop Metal and ETEC 3D printers to remain agile and innovative, was recently acquired by Marel (NASDAQ:MAREL), a global leader in the development and production of tools, complete solutions, software, and services for the food processing of chicken, meat, and fish. Elliði Hreinsson, Founder of Curio, uses bound metal deposition (BMD) technology from Desktop Metal to drastically reduce development lifecycles and time to market while also optimizing designs to improve performance.
Pictured above is a green-state metal 3D print of two brackets for the Curio C-2034 fish filleting machine. While the geometry is no problem to 3D print on the Studio System, built as singular pieces the elongated, organic shapes would cause the individual builds to curl during sintering, resulting in a warped final part out of the furnace.
Because the final assembly requires both a right and left bracket, Hreinsson mirrored the part in the slicer and exported the file as a single body. Further optimizing, he added two additional pieces to the build as well. The resulting print combines four parts that can be set on a single setter, allowing the heat to be more evenly distributed during sintering to avoid warpage. All four parts were printed together in just over one day. They then break apart from the setter after sintering via the ceramic interface layer (white lines in picture above).
The 316L stainless steel parts are printed directly from the digital design file without the lead time or investment for casting molds or tooling setups and installed on the machines at drastically reduced turnaround times compared to these traditional production methods.
Download the complete case study to learn more about how Curio food processing equipment is optimized with metal 3D printing from Desktop Metal.
100+ 3D printed parts on the Curio C-2034 filleting machine
LOCATION
Reykjavík, Iceland
CHALLENGE
First lot parts for assembly of a new machine required 54-58 weeks of lead time for tooling design to make molds to cast the metal parts. Stainless-steel components are exposed to heat, water, and harsh cleaning chemicals with the expectation that they remain easy to sanitize, durable, and corrosion-free.
SOLUTION
Desktop Metal Studio System
MATERIAL
316L Stainless Steel
PART
Combined four-part print with brackets and connectors
SIZE
178 x 170 x 40 mm, 611 g
PRINT TIME
25 hours, 38 minutes
WHY 3D PRINTING?
316L stainless steel parts are 3D printed in-house around the clock on four Studio Systems at Gullmolar, a manufacturing company and supplier to Curio
Tooling-less production allows iterations as designs quickly advance from ETEC plastic 3D printers to the Studio System for first-model metal prototypes within a few weeks
First-model metal parts are available within a few weeks after iterations and 3D printing on the Studio System