Enhance Educational Offerings and Research Capabilities with Binder Jetting
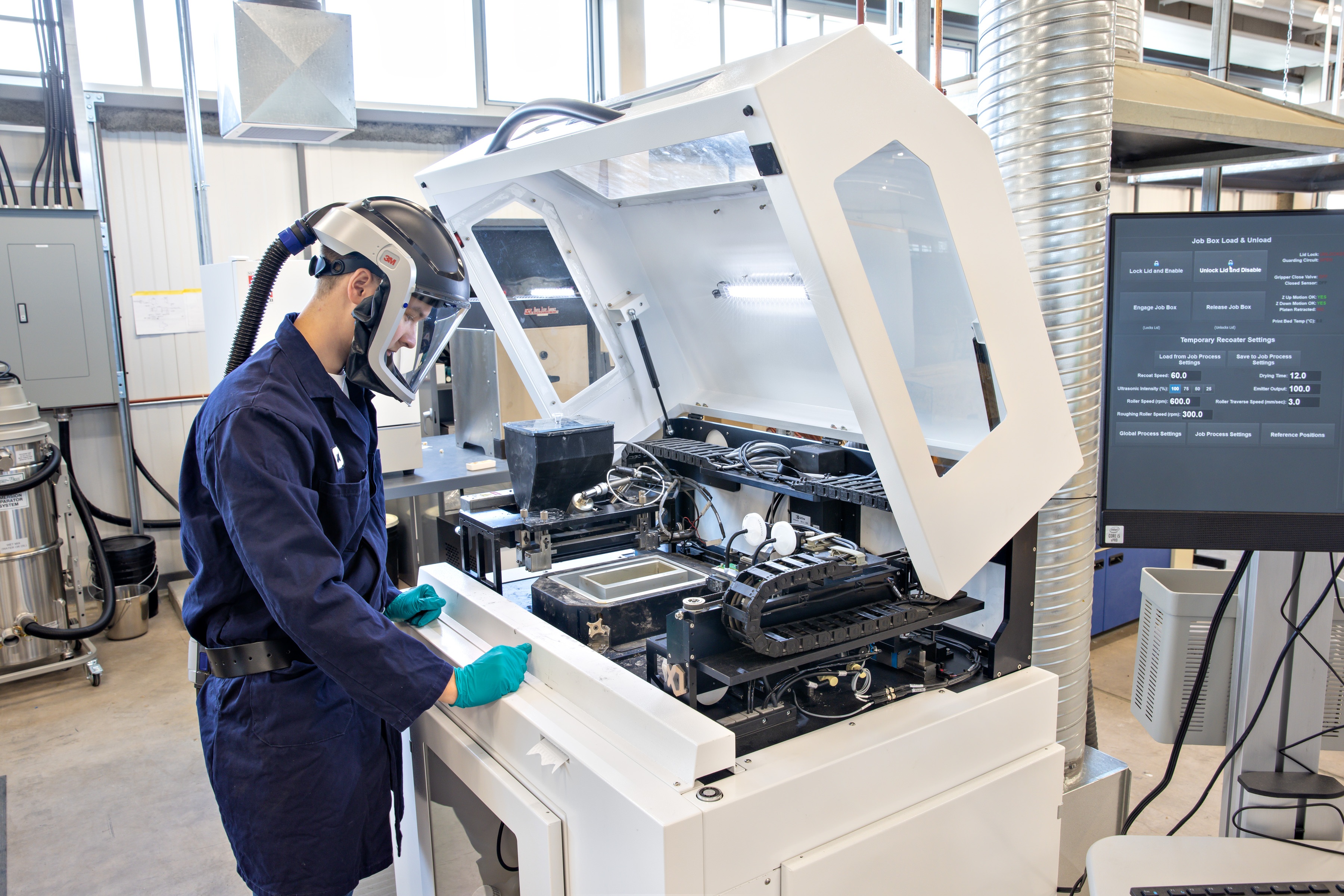
By adopting additive manufacturing technologies, educators can create an immersive learning experience that enhances curricula and prepares students for the demands of the modern workplace. Offering hands-on experience with additive equipment exposes students to advanced industrial processes and research capabilities while providing industry-relevant skills for high-tech manufacturing careers.
A variety of powder-based additive technologies are available on the market, but binder jetting is uniquely positioned to fit the needs of a flexible educational environment.
Cost-effective technology
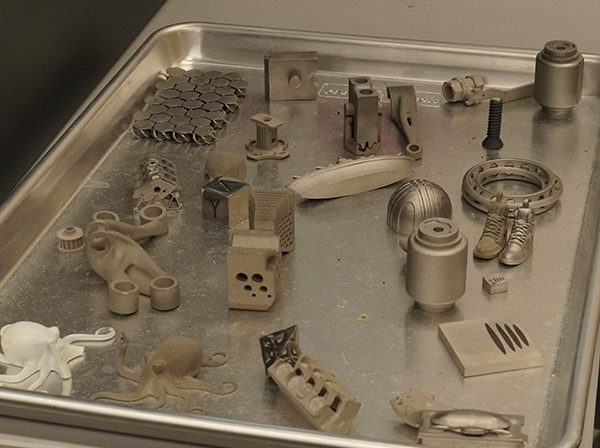
Binder jetting technology allows for the efficient production of a range of powders like metal and ceramics into complex and precise designs that can unlock performance innovations and unleash creativity.
The Shop System was developed to offer an easy-to-adopt approach in a complete software-hardware binder jetting package. Desktop Metal’s Live Suite™ software enables build success with features like automatic nesting and sintering analysis in a simple-to-use platform where users can configure part-specific settings.
With lower initial and operational costs than laser-based machines, binder jetting is a more cost-effective option for the budgets of educational institutions. The software-guided workflow and integrated metallurgical optimization make the Shop System a cost-effective investment in reliable and scalable metal 3D printing capabilities without compromising quality.
Material flexibility
Binder jetting provides the flexibility to work with a wide range of powder feedstocks, from metals and technical ceramics to foundry sands and reclaimed waste stream materials. This versatility offers educators the opportunity to explore diverse materials for their projects across a range of applications, from aerospace components and biomedical implants to architecture and consumer goods.
The Shop System is designed for easy adoption, operating with pre-qualified powders, including stainless steels and nickel alloys, and operational parameters defined for build success.
For more advanced lab settings where material flexibility is key, the InnoventX is an open-source binder jetting platform that is used around the world to research a variety of materials from unique metal alloys like copper to technical ceramics like silicon carbide. Its compact footprint makes it easy to operate for research, with a small print bed ideal for testing without large powder investments as well as simplified changeover between materials. Learn how Red Deer Polytechnic in Alberta, Canada uses the InnoventX for student and local business development in this case study.
High processing speeds
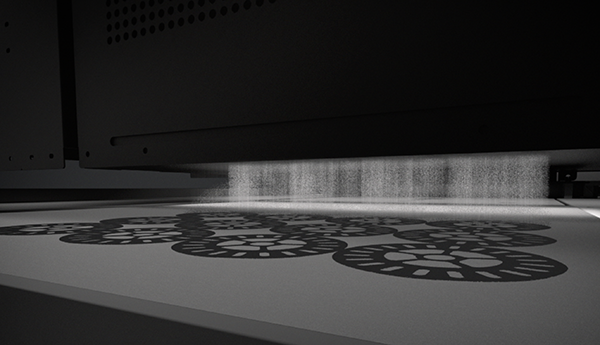
As an area-wide technology where an entire layer is processed with the sweep of a printhead, binder jetting unlocks quicker turnarounds with the ultimate production flexibility. Because each layer is built by depositing binder across the powder bed with the single pass of printhead, similar to printing on a sheet of paper, overall build times are affected more by the height, i.e. the number of layers to be built, than the design, or multiple designs, nested across the print bed. Laser-based systems, in contrast, use one or multiple single-point sources to trace geometries, increasing build times as more is added to the build plate.
Binder jetting boasts the high-speed printing capabilities that enable educators to rapidly prototype and produce metal components for research projects, coursework, and industrial collaborations.
Process optimization
Binder jetting unlocks the sustainability benefits of additive manufacturing, such as lightweighting and performance-optimized designs. Because binder jetting is a thermally-neutral process using liquid binder to build parts, the 3D printed parts are supported by the surrounding powder bed. Metal supports, as required in many laser builds to anchor parts to the build plate and dissipate heat, are not required. This minimizes material waste by utilizing only the necessary amount of powder needed for the design.
Eliminating thermal destressing as well as machining, or other means of support structure removal, also makes binder jetting an operationally efficient option for metal 3D printing. The Shop System comes as a complete software and hardware package with all the equipment needed to get started metal 3D printing with ease.
In the ever-evolving landscape of metal 3D printing, binder jetting from Desktop Metal offers a user-friendly experience, making it easier to integrate into educational environments for hands-on learning. Students at Clarkson University used the Shop System to gain the competitive edge in the SAE International Clean Snowmobile Challenge (CSC). Read the case study to learn more about their experience with binder jetting.
Universities adopting binder jetting
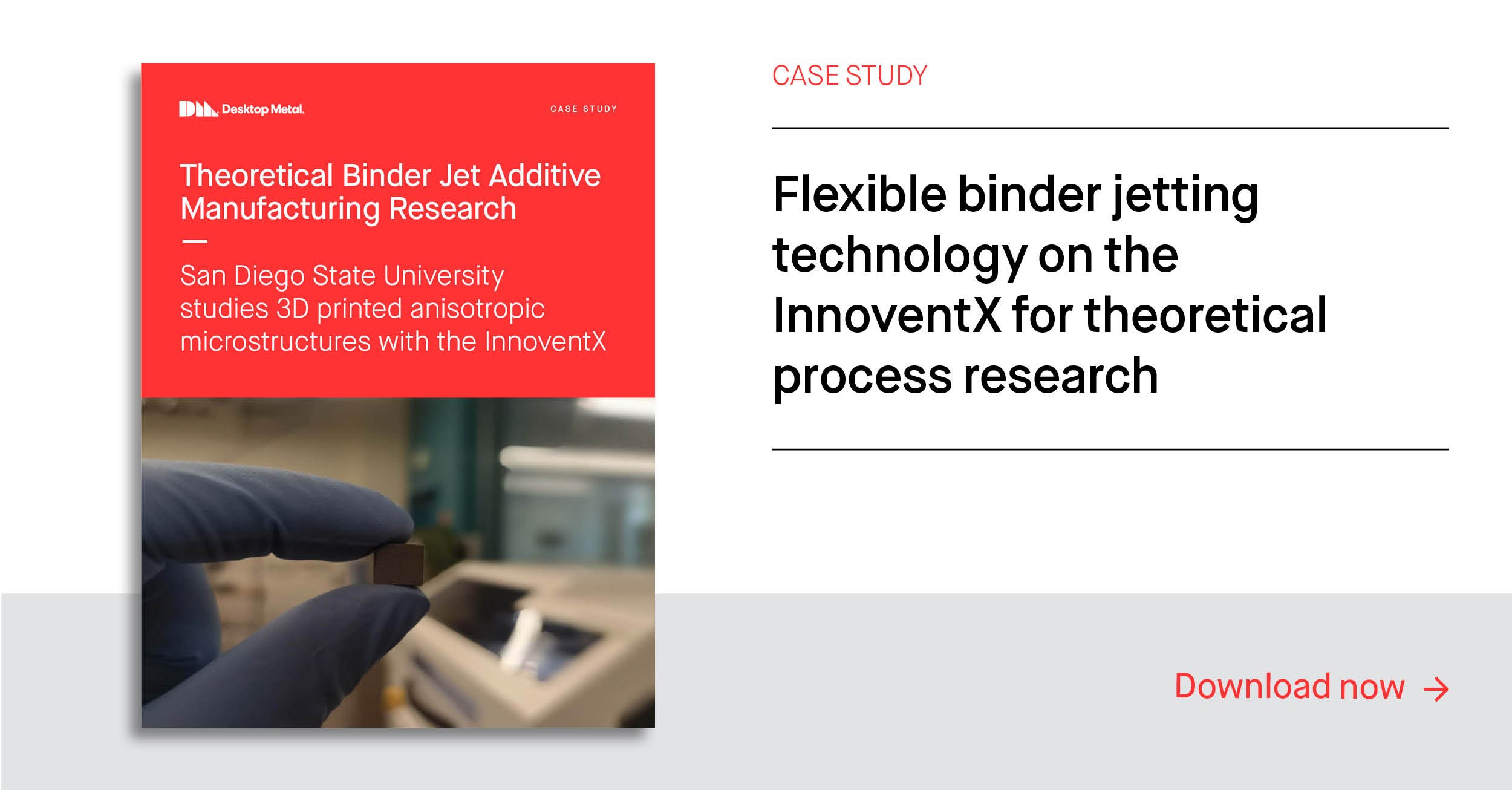
With versatile material options, from stainless steels to carbides, binder jetting equipment provides the next generation of engineers and researchers with the tools to develop industry-relevant skills to meet the challenges of the future. And many universities are already adopting binder jetting technology at their facilities - download this story from San Diego State University to hear first hand how binder jetting helps its team study the anisotropic
advance research opportunities.