Desktop Metal's Additive Experts Offer Engineering Partnerships to Solve Customer Challenges
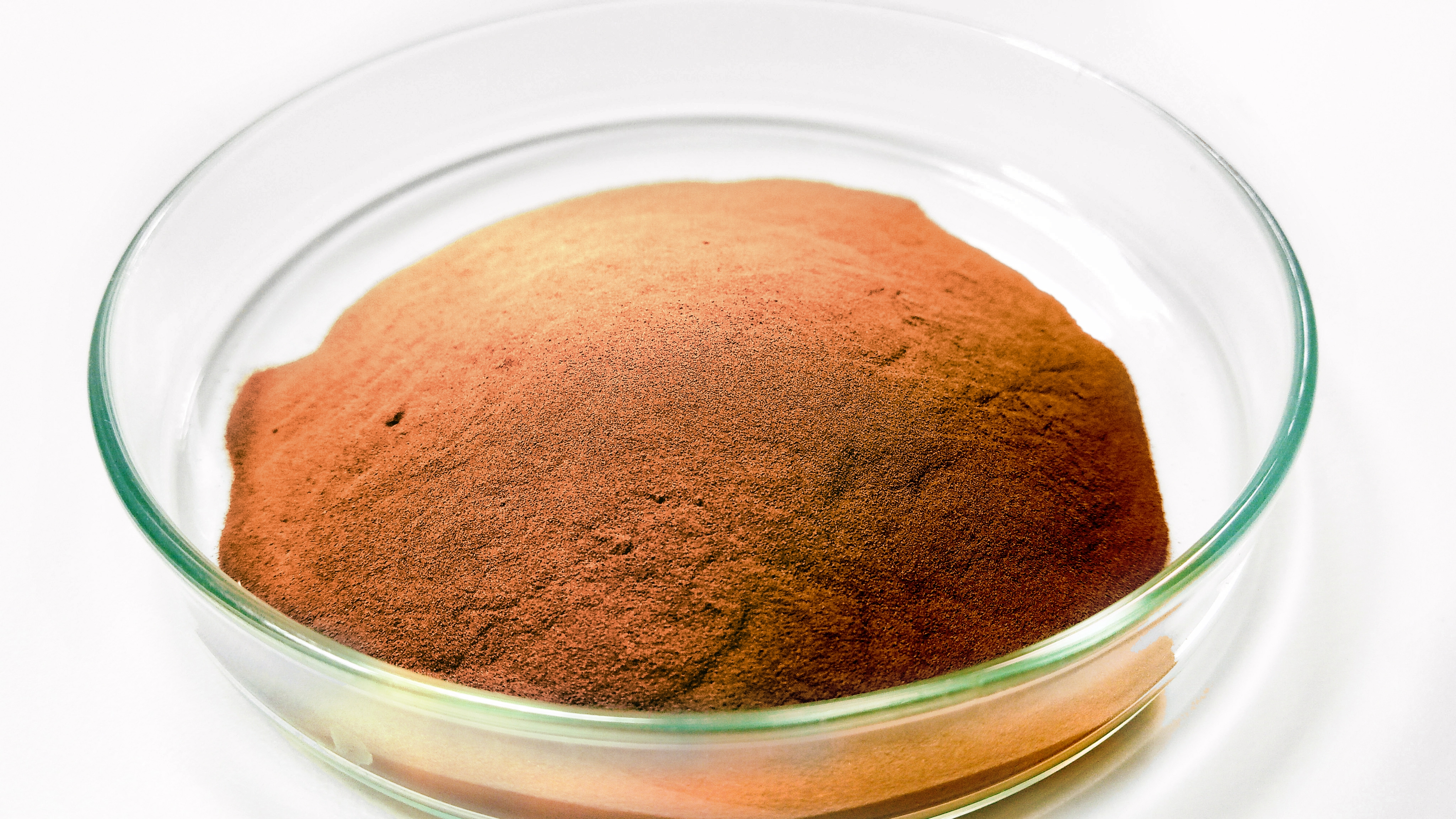
Kyle Myers, Senior Director of Materials Development at Desktop Metal, began working with a leading innovative automotive company that wanted to explore binder jet 3D printing possibilities for a targeted component. He can’t reveal the confidential application but explains that it has to do with heat transmission, requiring mechanical strength while maintaining fast heat dissipation properties. Many other industries such as aerospace and electronics have similar requirements, so Myers and his team were eager to find a scalable solution.
One of the main challenges for the application was finding the right material for the job. “Pure copper is the best metal for conductivity, but it lacked the required strength,” Myers said. Pure copper can also be a challenging material to process to high density with the binder jetting process, though many customers desire to take advantage of the geometric freedom and lower costs of 3D printing this conductive material.
So, the Desktop Metal team of material and process experts turned to their industry network; Sandvik Additive Manufacturing’s copper-based Osprey® 18150 powder (CuCrZr) seemed to fit the bill. Myers explained, “We found the idea of an enhanced copper powder very attractive. The additional chromium and zirconium would likely do the job, so we decided to test it on the specific application.”
Partnership throughout development
Over two years, Myers and his team have worked together with the customer to test and verify the material and the process. The Desktop Metal team interfaced with Sandvik to ensure the material met performance requirements and developed process parameters to successfully 3D print and sinter the desired geometries. It’s now internally qualified at the customers’ facility and ready for scale-up.
In taking any customer application from proof of concept to production, Myers stressed the importance of developing a stable manufacturing process that fits each customers’ specific production needs. “We share updates and get feedback from our customers to ensure we are meeting their specific metrics. We have worked with customers to develop materials and manufacturing cells and validate processes that can dropped at a customer site,” he emphasized.
He describes Desktop Metal AM2.Production team as experts on the frontline of additive manufacturing innovation, working dedicatedly to find the right material and right processes for each individual customer.
“We’re always looking for innovative ways of solving customer challenges, using a solid foundation of experience and expertise,” Myers said. “Throughout the entire application development process, we are an extension of the customer’s engineering team.”
Do you need a solution for your toughest manufacturing challenges? Click here to learn more about our AM2.Production program and find out how our team can help.