Battlebots® team builds combat robot with Studio System™ parts
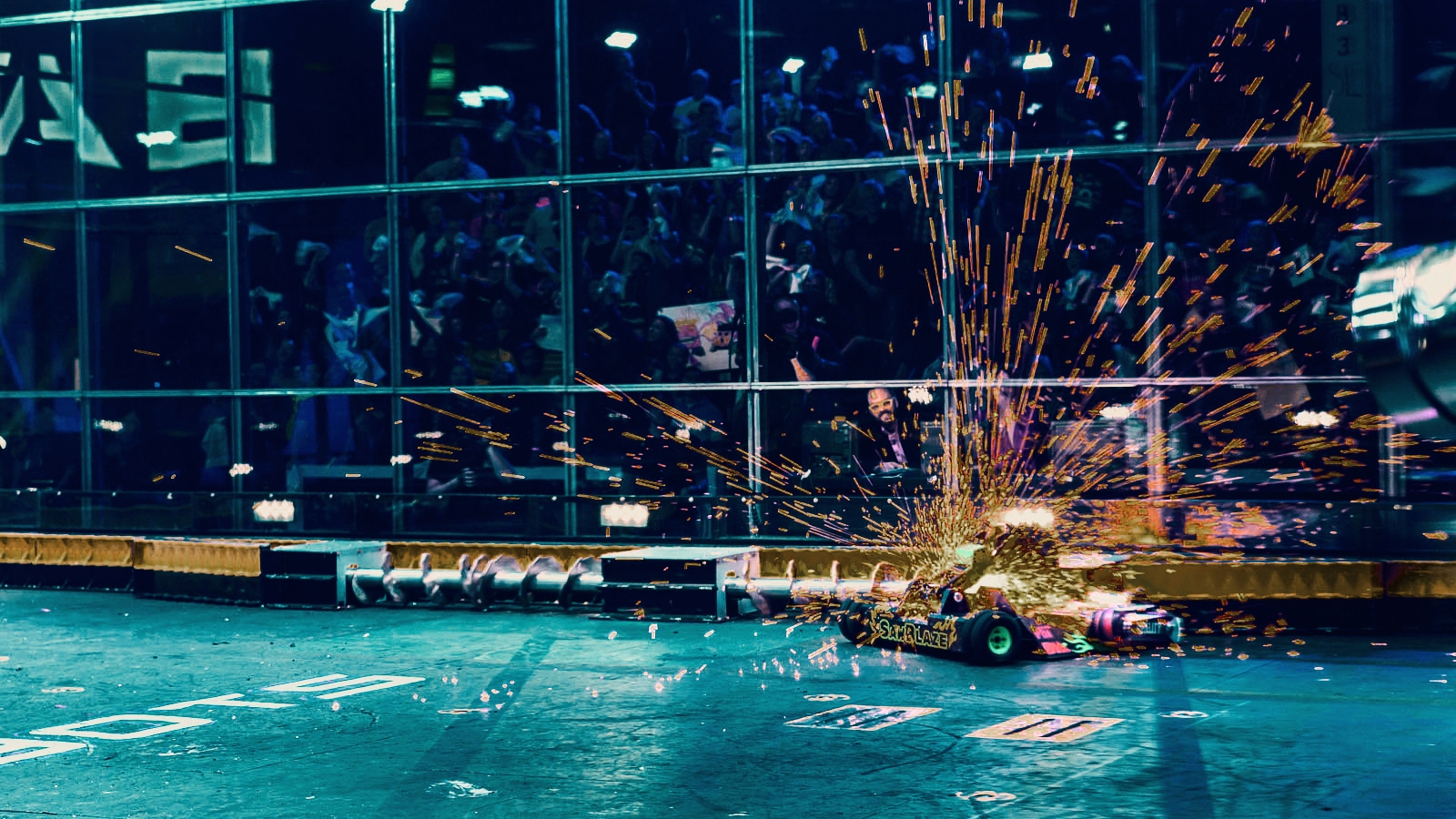
BattleBots® is a televised robot combat tournament that challenges teams of engineers from all over the world to design, build, and control a robot—demonstrating creativity, engineering skills, strategy, and driving ability. Each robot must be no more than 250 lbs with at least one independently-powered weapon. Robots fight in a closed arena surrounded by bullet-proof glass, going head-to-head to avoid elimination and get closer to the championship title.
When designing a robot, teams consider several factors that will determine its ability to beat the competition while withstanding various obstacles built into the arena. These considerations include:
- weight
- precision of motion
- materials
- controllability
- impact resistance
- effectiveness of its weaponry
The design of each component is critical to the robot’s overall performance while the limited development timeline leaves little room for iteration.
Comprised of MIT engineering students and graduates, Team SawBlaze is a Boston-based competitor whose robot’s weaponry includes a diamond abrasive rescue saw blade and flame-thrower. The blade is mounted to a controllable rotating arm that positions the saw at the front or back of the robot. This helps to stabilize the machine while enabling a bi-directional offensive. The flame-thrower emits green flames at 350°C in the direction of the saw’s target, delivering “slash and burn” blows to the opponent.
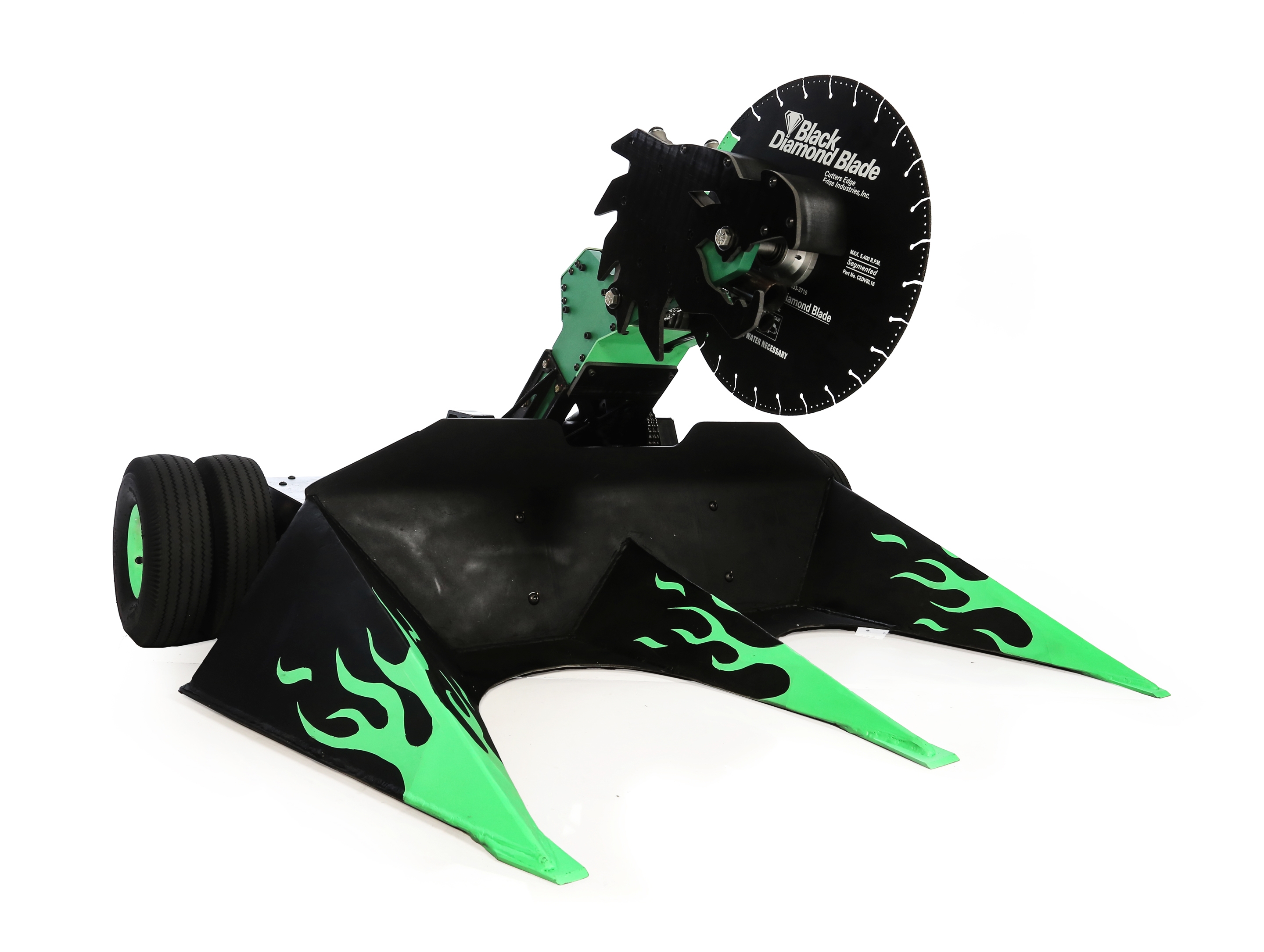
The challenge
The 2018 season featured the shortest build calendar ever, allowing just one month to build and ship the robot. Each component plays a critical role in the robot’s ability to perform, so the more design iterations the team is able to do before the final build, the better. Jamison Go, Mechanical Engineer at Desktop Metal and SawBlaze team captain, saw an opportunity to leverage the benefits of metal 3D printing with the Studio System—including design flexibility, rapid iteration in-house, high-performance materials, and reduced production costs—in order to spend more time fine-tuning custom parts for the robotic assembly.
In contrast to most BattleBots robots that apply brute force, SawBlaze applies precision damage. This strategy is much more difficult to execute. Working against a limited development timeline, our processes must be extremely efficient in order to achieve an optimized and consistent strength-to-weight ratio as the robot moves and comes into contact with the competition.”
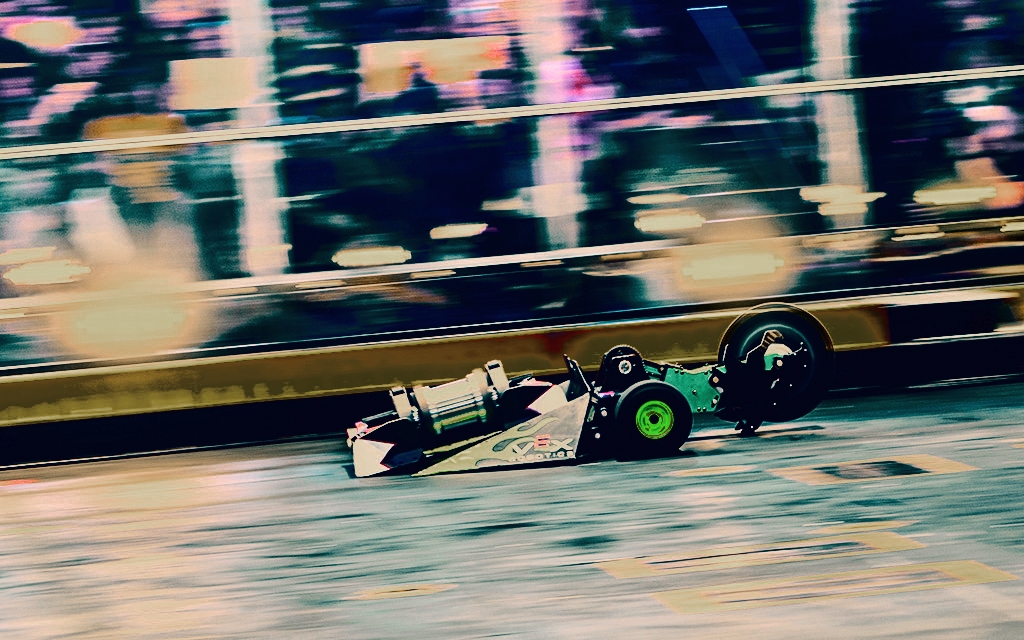
The Part
One of the key components of the SawBlaze robot is the backstop: a sub-assembly that straddles and protects the blade. As various loads are applied during battle, the backstop must demonstrate stiffness, strength, hardness, corrosion resistance, and heat resistance.
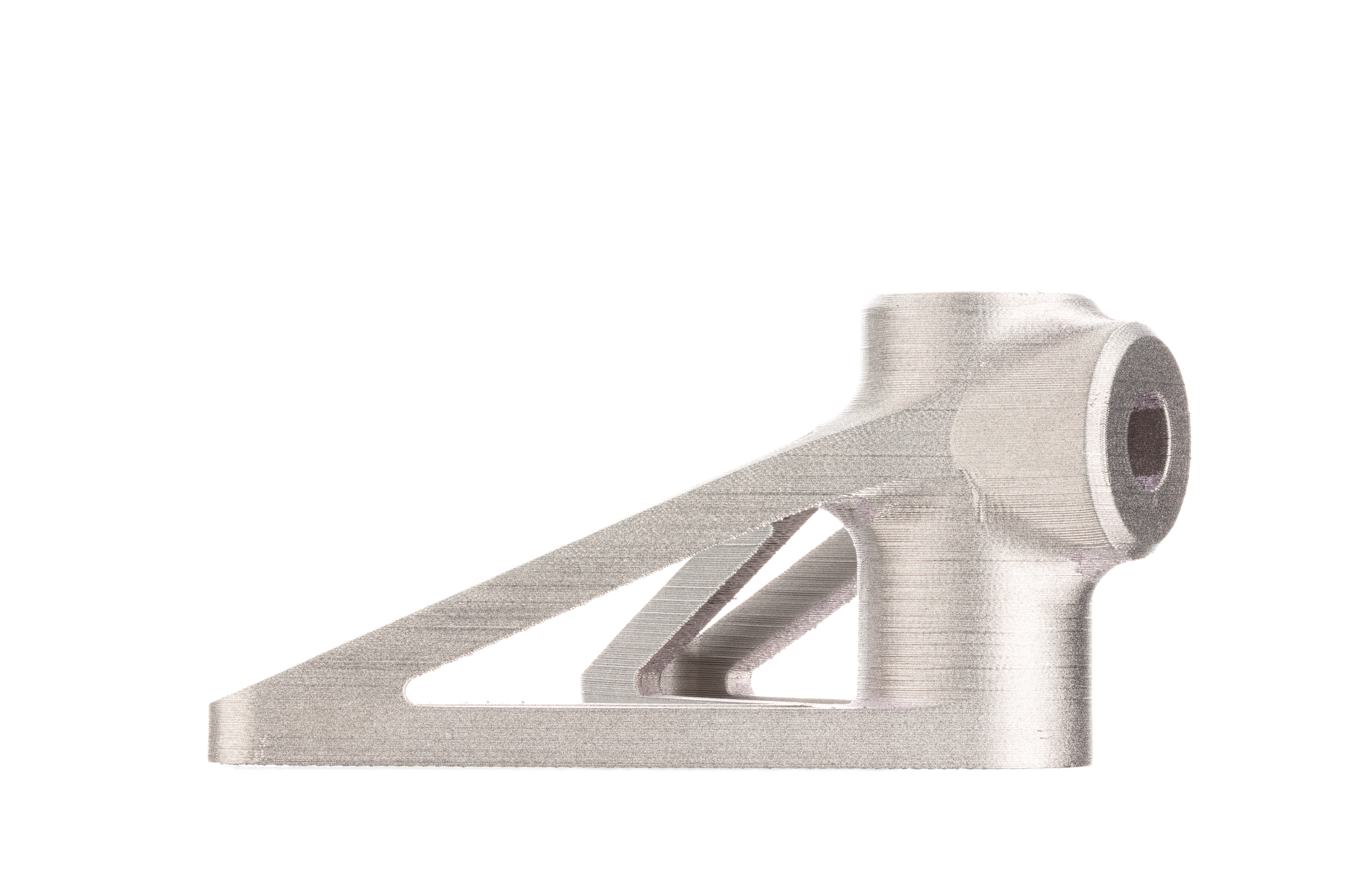
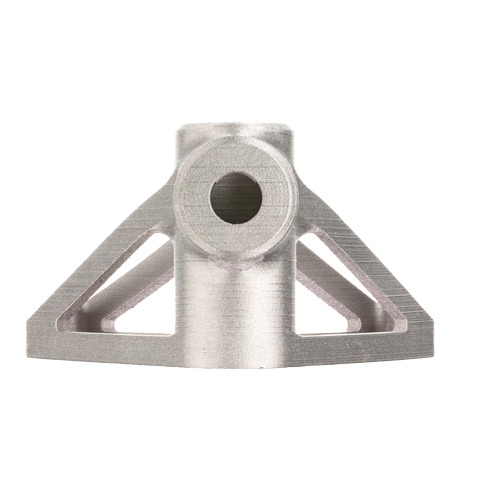
Process Comparison
With a limited timeframe and budget, the fabrication method is an important consideration—particularly for custom parts like the backstop. The cost and lead time introduced with third-party manufacturers leaves no room for iteration, while the design limitations of machining in-house would jeopardize part performance and introduce a significant opportunity cost due to the number of manual steps required.
The challenge of achieving lightweight strength made the backstop an ideal candidate for metal 3D printing. The team designed the part with “cut-outs” and leveraged closed-cell infill throughout the part to eliminate excess material and reduce its weight in techniques that are impossible with other manufacturing methods.