Studio System™ 2
Office-friendly metal 3D printing in just 2 steps — Print. Sinter.
Available Now.
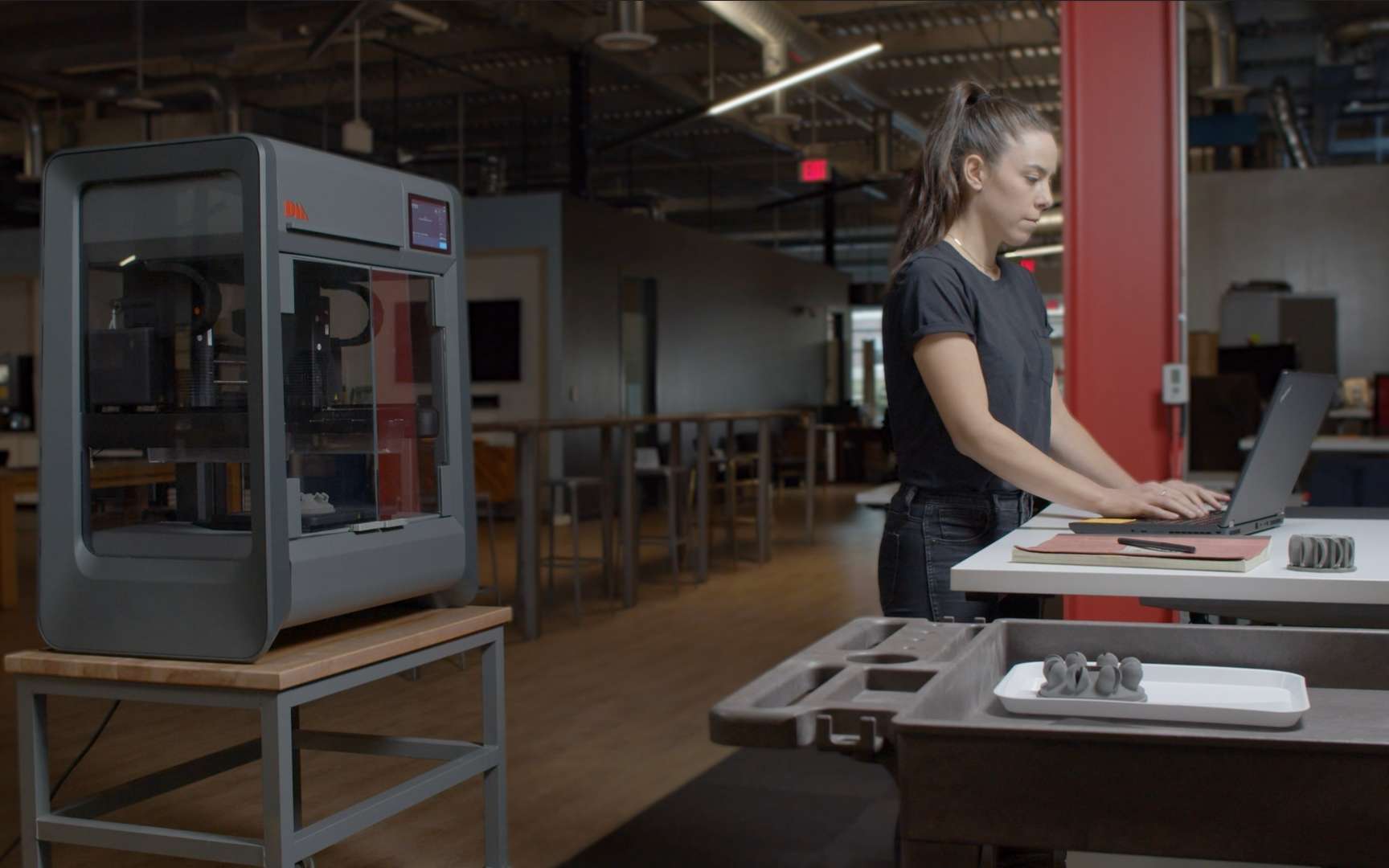

-
— 01
Easy, two-step processing
-
— 02
High-quality parts
-
— 03
Designed for the office
The Studio System™ 2 is the easiest way for designers and engineers to print metal parts.¹
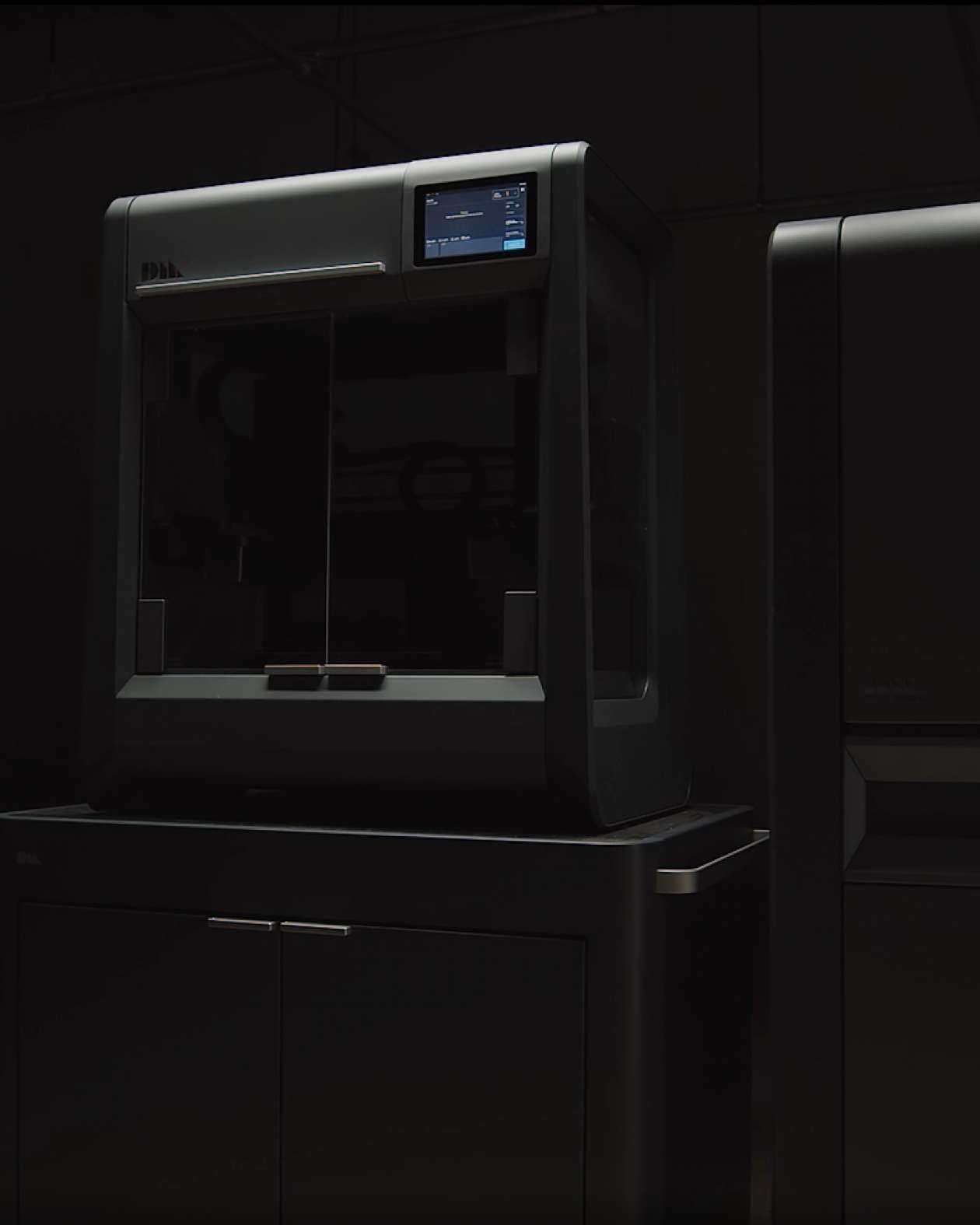
Easy, two-step processing
Making complex, high-performance metal parts has never been easier. Featuring a breakthrough two-step process, next-generation Separable Supports, and a software-controlled workflow, the Studio System 2 makes it simpler than ever to produce custom metal parts.¹
Print to Sinter
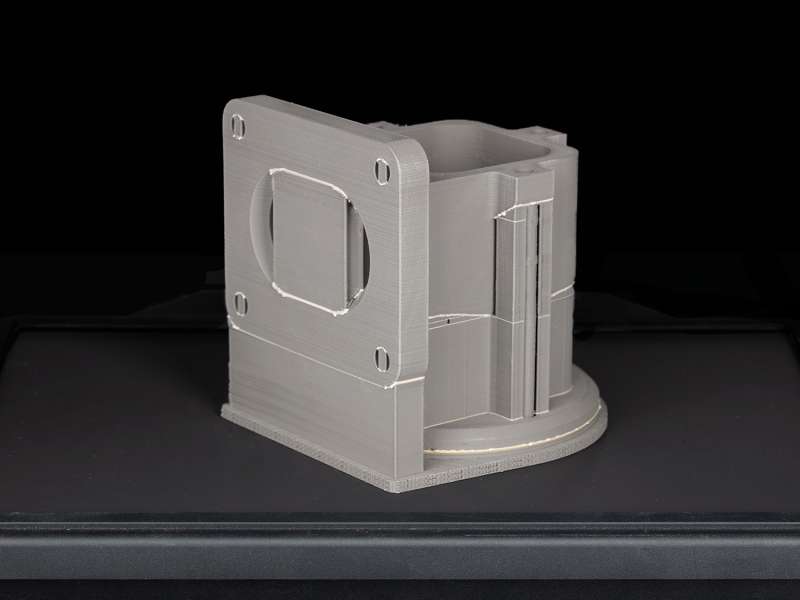
The Studio System 2 unlocks two-step processing with a fully re-engineered materials library. New material formulations allow printed parts to be placed directly into the furnace, without the need for the typical solvent debind phase. The result is an easy-to-manage two-step process with a nearly hands-free experience.
Software controlled workflow

You don’t need to be an expert metallurgist or machinist to create complex metal parts. With our Live Studio™ software, native to Studio System 2, all aspects of part creation - from printing through sintering - are automated. The software automatically scales your part, orients it for print and sintering success, generates separable supports, and applies expert metallurgy to optimize fabrication. Simply upload your design and follow the onboard UI for step-by-step guidance.
Learn MoreSmart Separable Supports
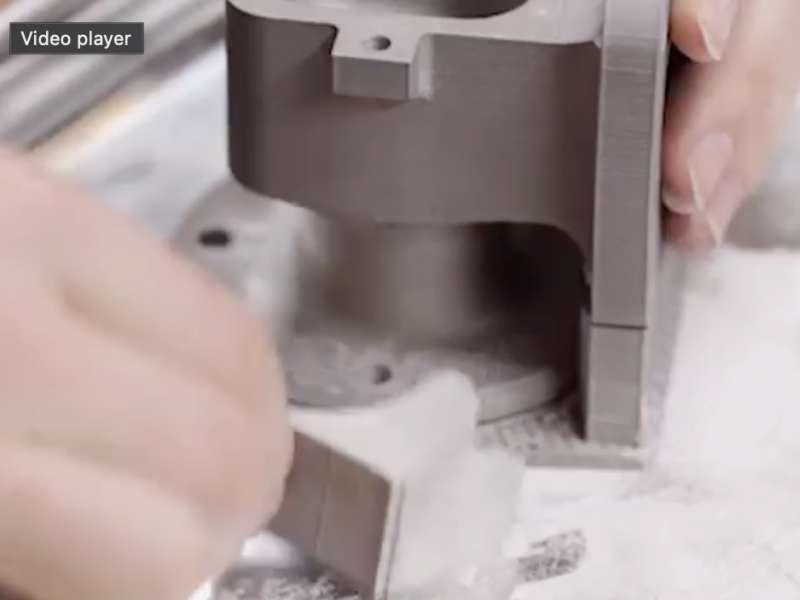
The Studio System 2 features Desktop Metal’s second-generation Separable Supports technology, which automatically generates seams throughout support structures, and prints a reformulated ceramic interface material between the support structure and the part, allowing parts to easily be removed by hand.
Learn MoreUser-friendly hardware
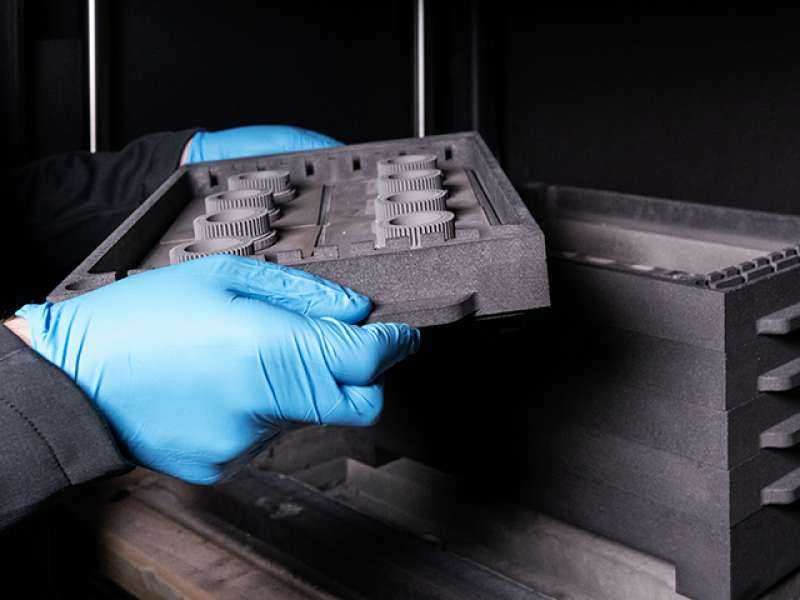
With easy-to-use hardware, the Studio System 2 allows you to spend less time managing equipment and more time designing and fabricating parts. Change printheads with the press of a button, and change materials quickly with a refillable cartridge system that allows users to easily load material during print jobs and store excess material safely. A fully-accessible printer and sintering volume and a configurable furnace retort allow for maximum flexibility.
Download Brochure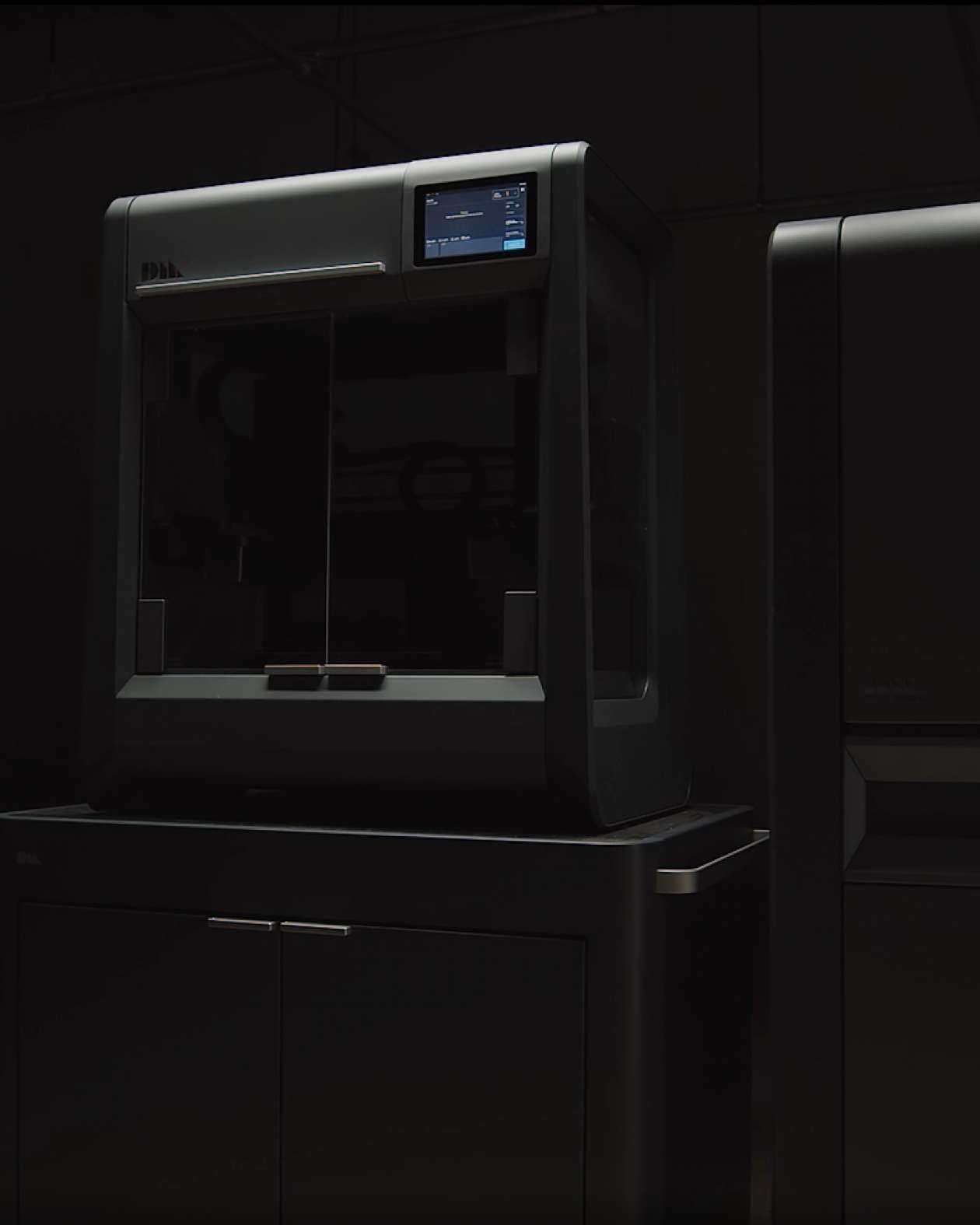
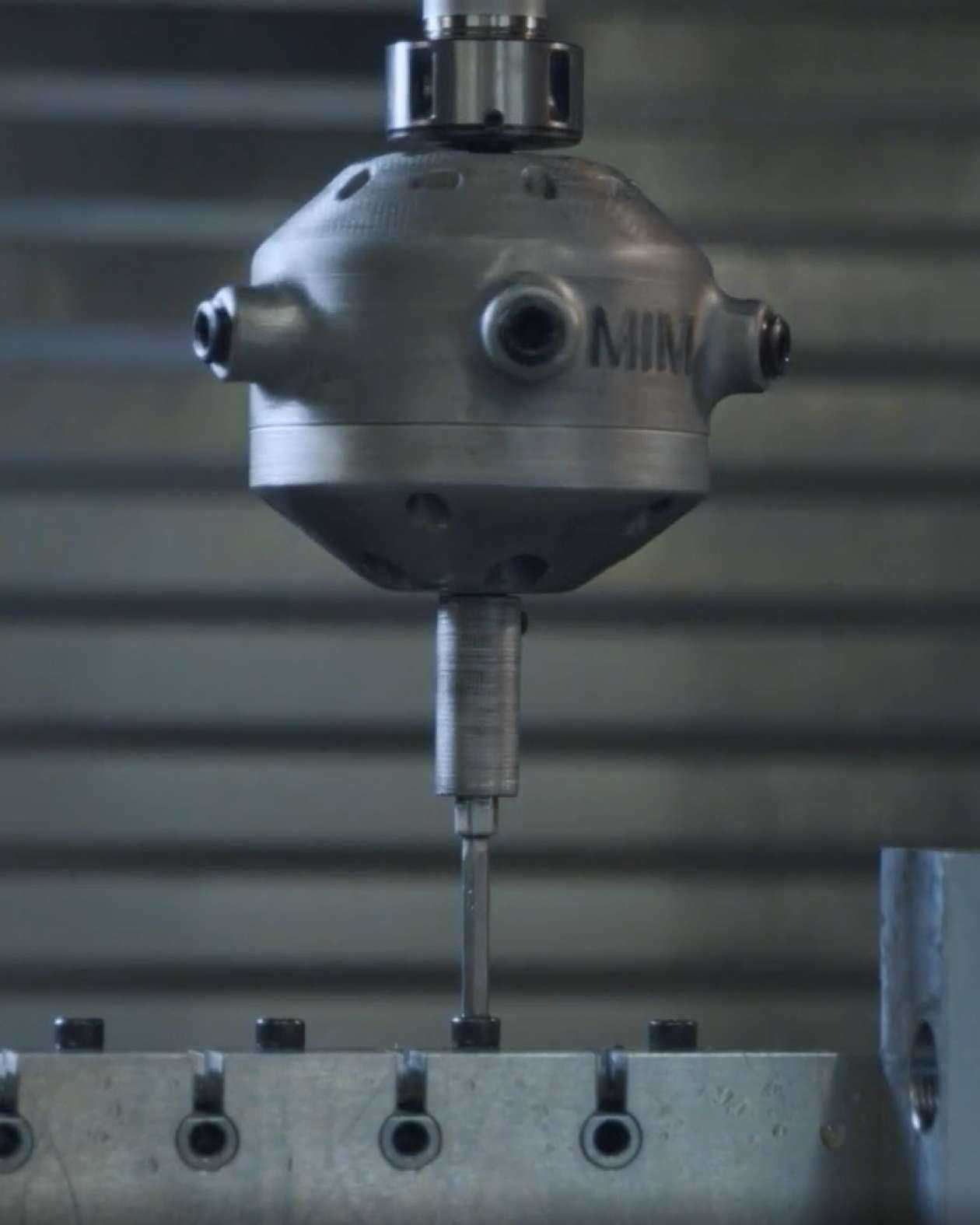
High-quality parts
Easily produce difficult-to-machine parts featuring complex geometry like undercuts and internal channels. Live Studio, the software at the heart of the Studio System, automates complicated metallurgical processes to produce high-quality parts with densities and feature accuracy similar to casting.
Reliable Processing
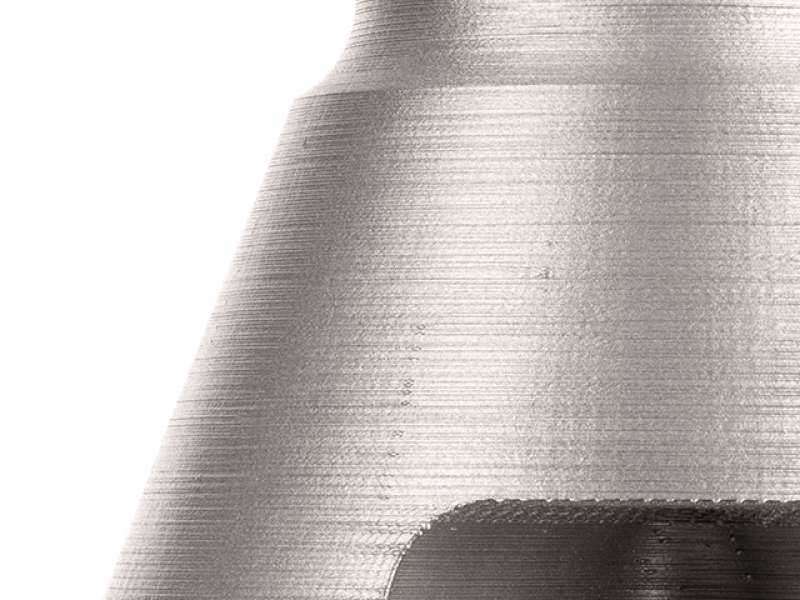
The Studio System 2 leverages data and feedback from thousands of prints and hundreds of customers. Designed to deliver outstanding part success and excellent surface finish, the system allows users to achieve first-time part success across a wide range of geometries. This is made possible by a fully re-engineered material platform, updated interface technology and new print profiles.
Excellent Part Properties
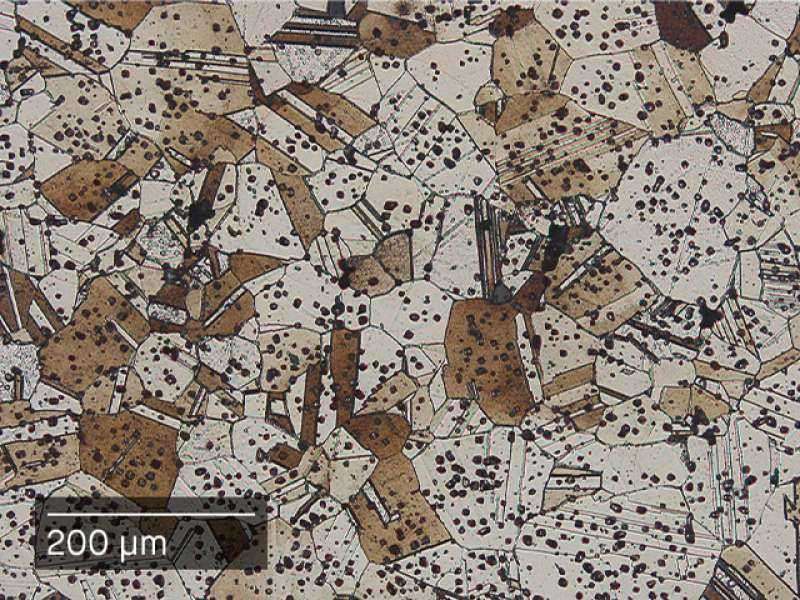
A heated build chamber and Desktop Metal-engineered print profiles produce excellent surface finish right out of the furnace, while a high strength gyroid infill now lightweights parts. With materials that meet or exceed MPIF standards and the use of high metal volume fraction media, high-pressure extrusion and vacuum sintering at temperatures of up to 1400°C, the system produces parts with densities of up to 98 percent - similar to cast parts.
Customizable print settings
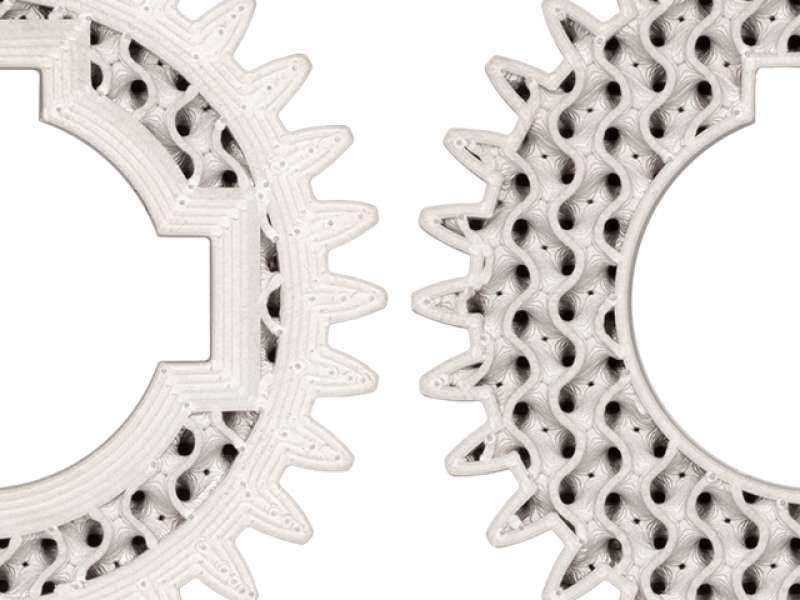
The Studio System 2 allows you to tailor parts to your exact needs. Print parts with walls up to 4mm thick or fully-dense parts (with no infill) up to 5.25mm thick. Adjust shell thickness to create stronger parts or enable faster processing. Optimize prints for build speed using the standard (400µm) print head, or print fine features with the high resolution (250µm) print head.
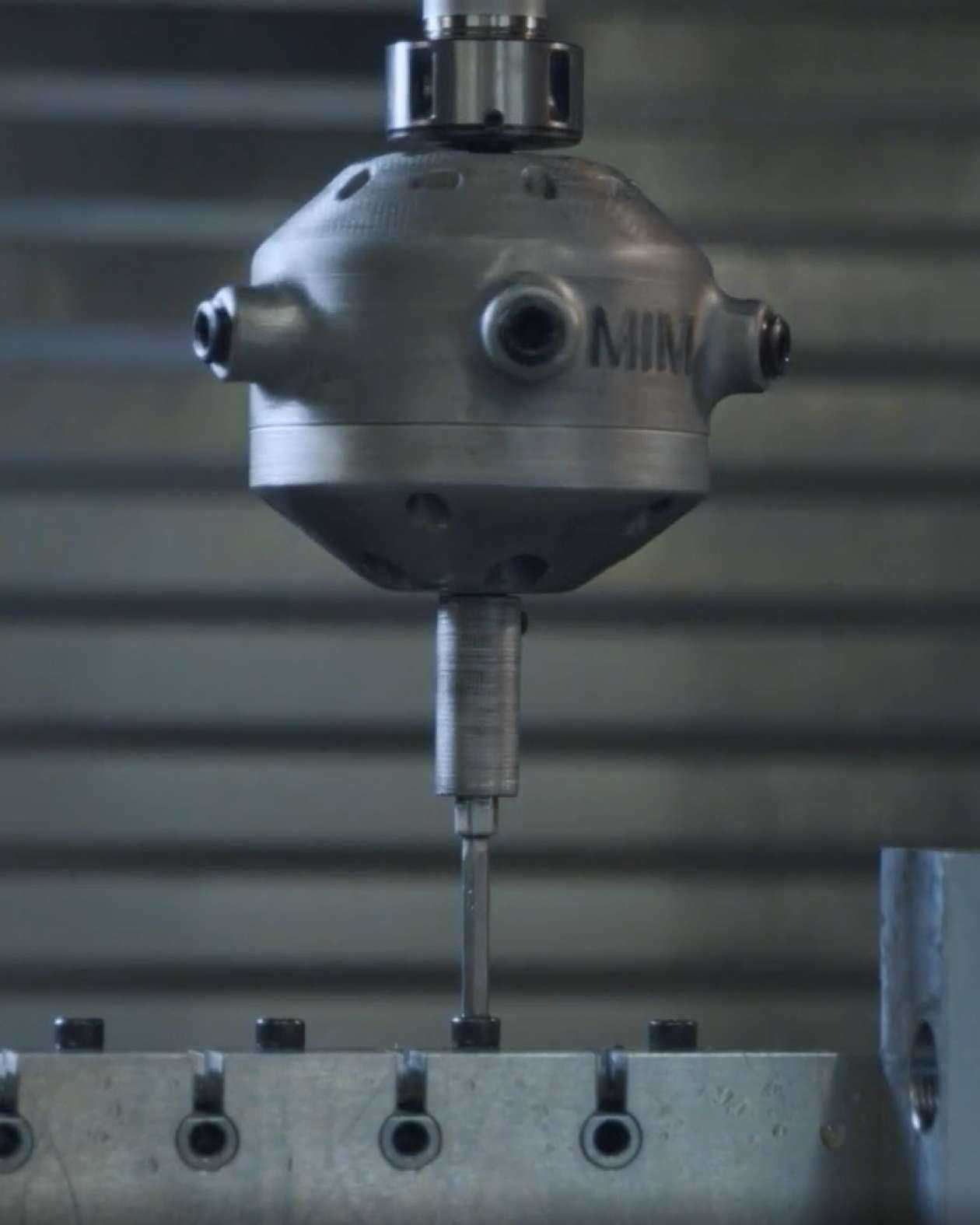
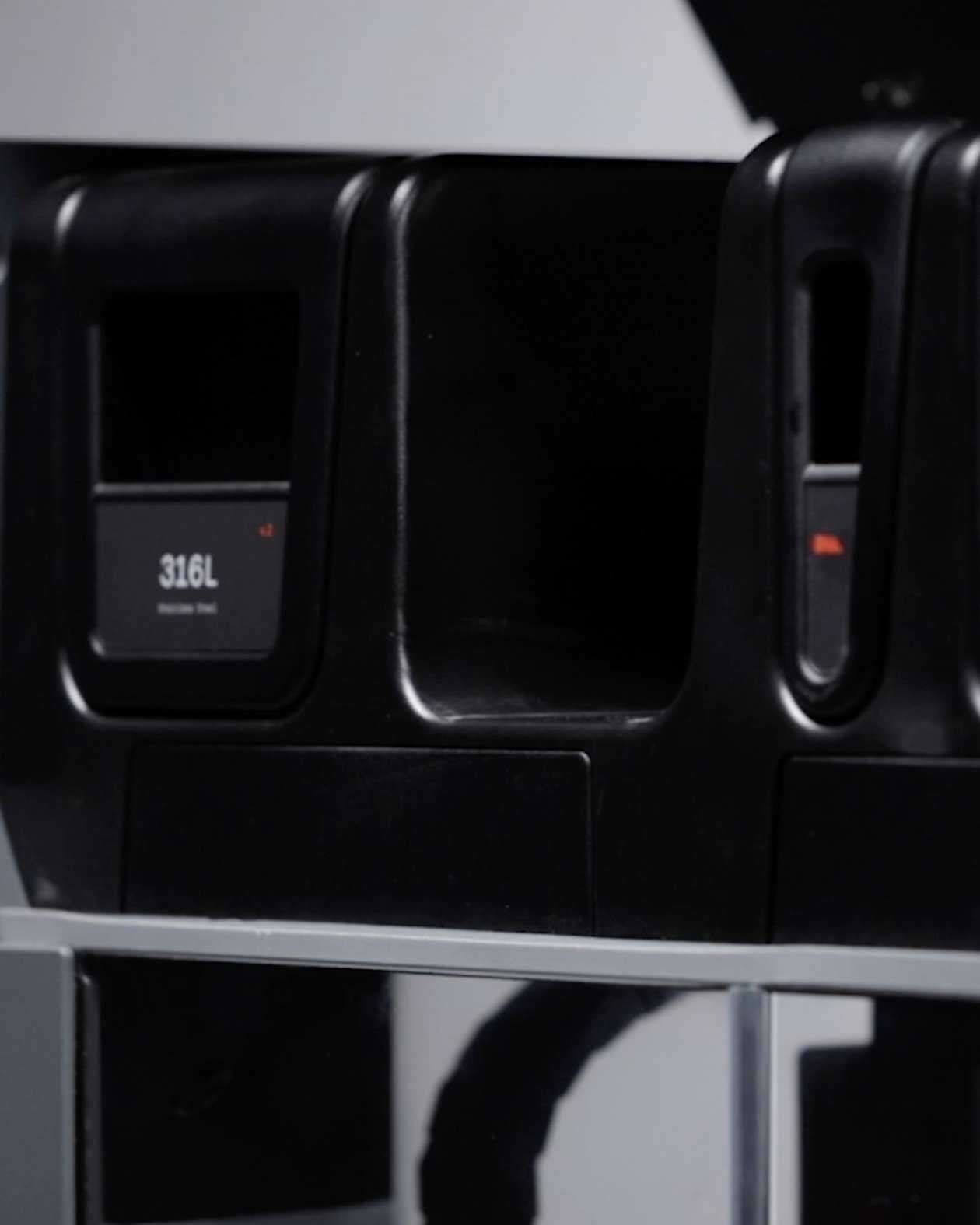
Designed for the office
The Studio System 2 was designed from the ground-up to fit into your team’s workflow. With no solvents, no loose metal powders or lasers and very little operator intervention required, the system makes it easy to start printing metal parts - no third party equipment or special facilities required.
No special facilities requirement
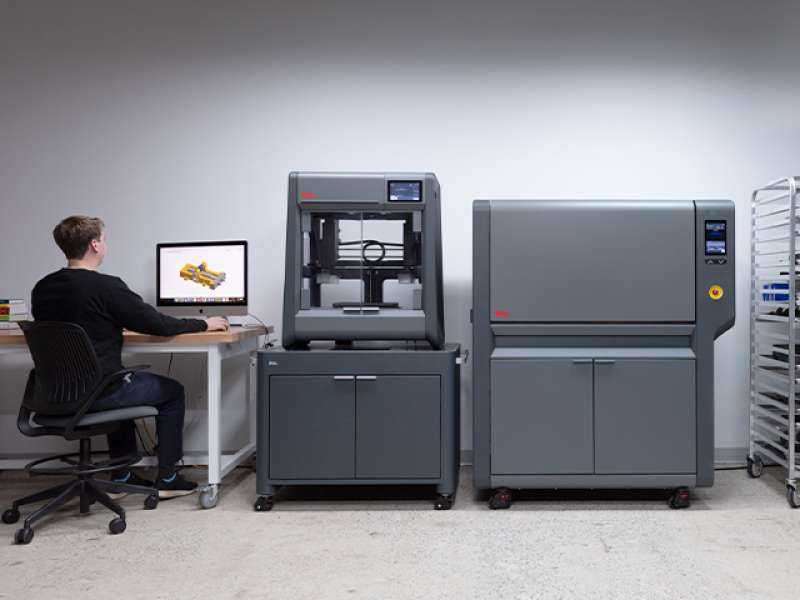
The Studio System 2 features a two-step process that eliminates the need for solvents and uses materials that can be easily stored and handled, making it ideal for use in an office environment - no special facilities and no respiratory PPE needed. The only requirements are an internet connection, ventilation and power, making it easy to quickly start printing metal parts.²
Hands-off process
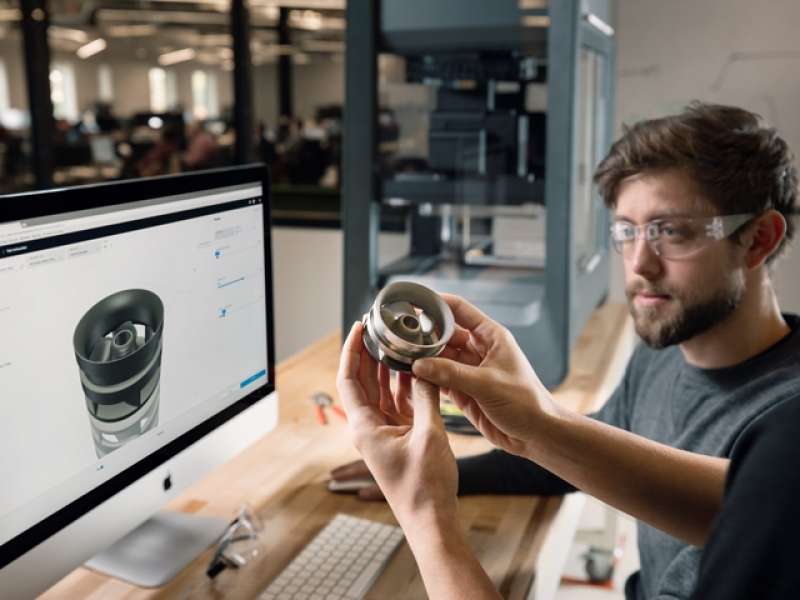
The Studio System 2 helps you regain control of your prototyping pipeline by allowing design and engineering teams to focus on making the best possible products. The simplified, easy-to-manage process allows users to quickly iterate on designs, print parts and monitor build progress from their desk, and significantly reduces operator burden - parts go directly from the printer into the furnace, where a large retort with stackable shelving (10x the capacity of a similarly-sized tube furnace) allows for batch sintering.
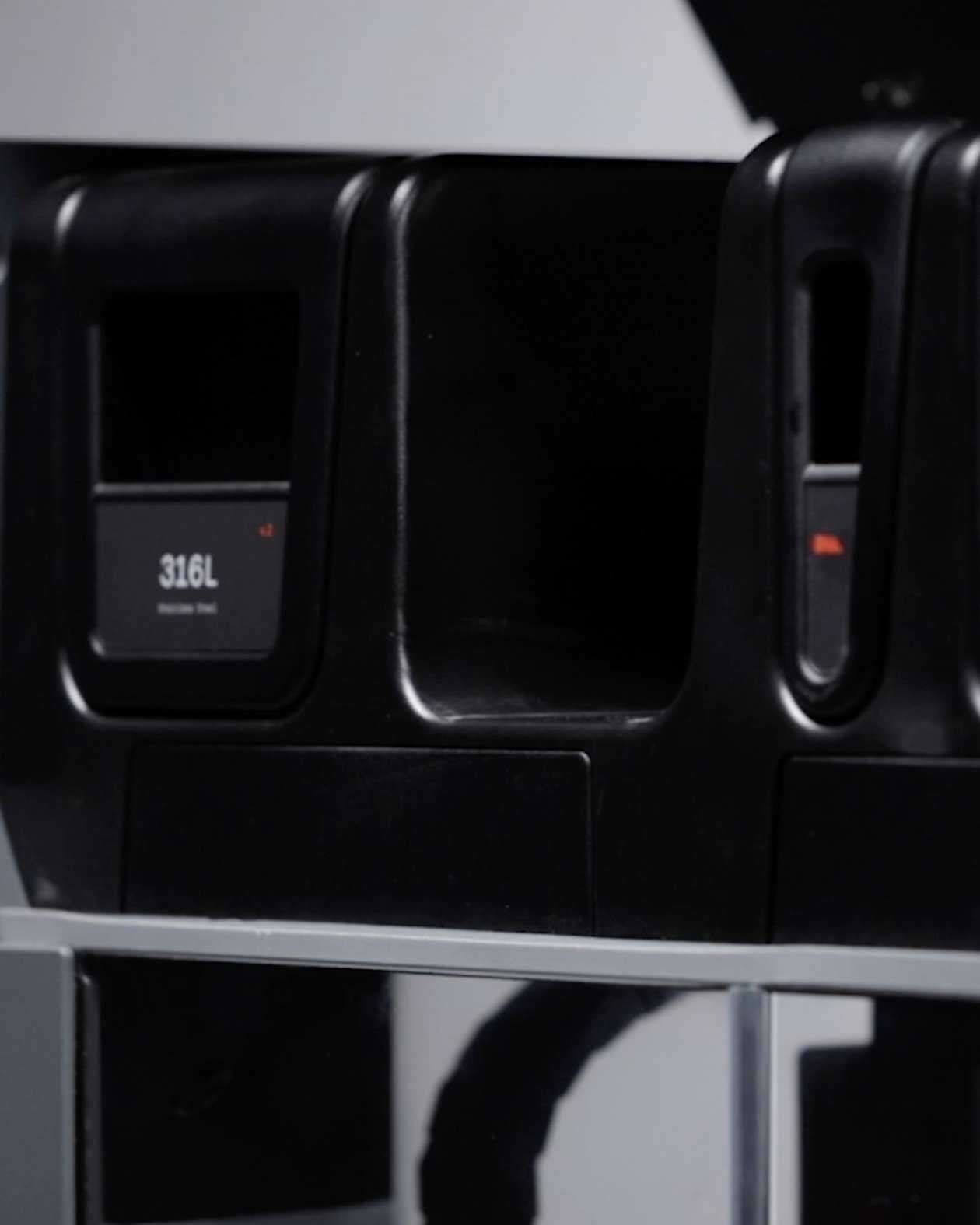
How it works
The Studio System 2 is a two-part solution that streamlines metal 3D printing. Simply load your CAD file into Live Studio, our proprietary software, print your part, and place it in the furnace for sintering.
-
Prep
Secure, web-based software constructs build plans from STL or CAD files, automatically generating supports and control parameters based on part geometry and material.
-
Print
Layer by layer, a green part is shaped by extruding bound metal rods—metal powder held together by polymer binders—in a process called Bound Metal Deposition™.
-
Sinter
Once printed, parts are placed in the furnace. As the part is heated to temperatures near melting, binder is removed and metal particles fuse together causing the part to densify up to 98%.
Part gallery
Studio System™ applications span a variety of industries including manufacturing, tooling, automotive, consumer, electronics, and oil & gas.
Applications by Industry
Explore applications for 3D printing across a range of industries.
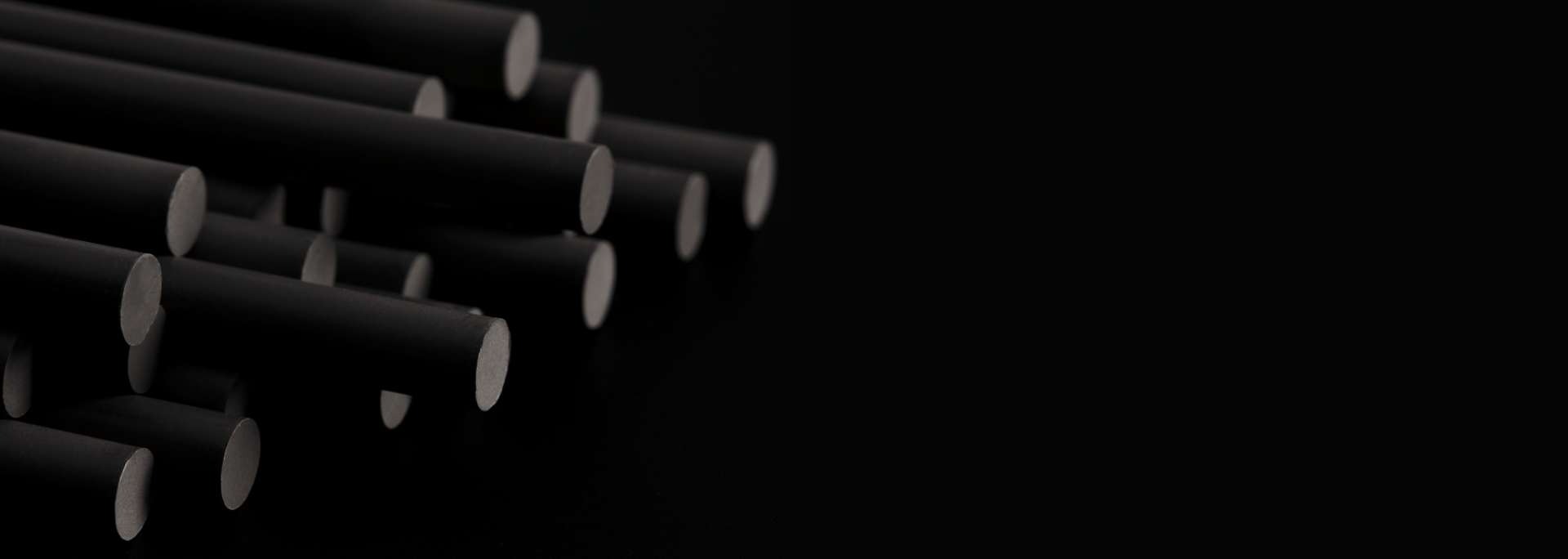
1. Unlike comparable metal 3D printing systems, Studio System™ 2 eliminates loose metal powders and features a two-step process (no solvent debind required) and features Separable Supports technology with strategic splits for hand-removable supports, hot swappable cartridges and removable printheads to make material changes easy, and a fully software-controlled workflow.
2. Statements made regarding respiratory PPE are specific to requirements for operating the Studio System. We recommend all users consult local authorities regarding PPE for COVID-19 protection.