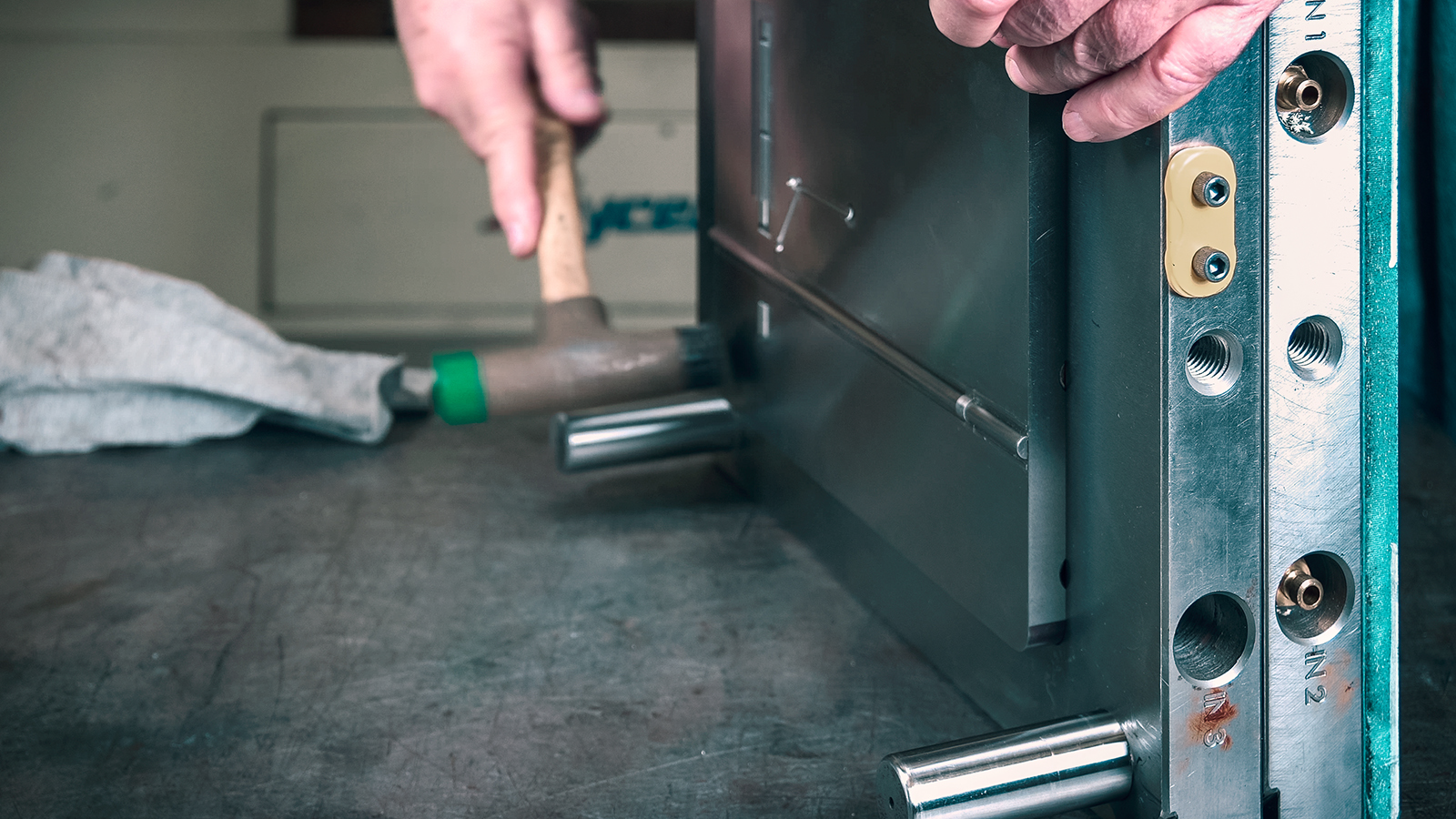
Custom tooling and reduced down time on the manufacturing floor
By quickly producing manufacturing tooling like jigs, fixtures and mold inserts, 3D printing helps shorten lead times and cost, allowing companies to move quickly from finished design to production.
Due to its complex geometry, tooling is typically CNC machined, which can lead to bottlenecks due to limited capacity in both machines and operators. Printing tooling can eliminate those obstacles, reducing down time across the manufacturing floor.
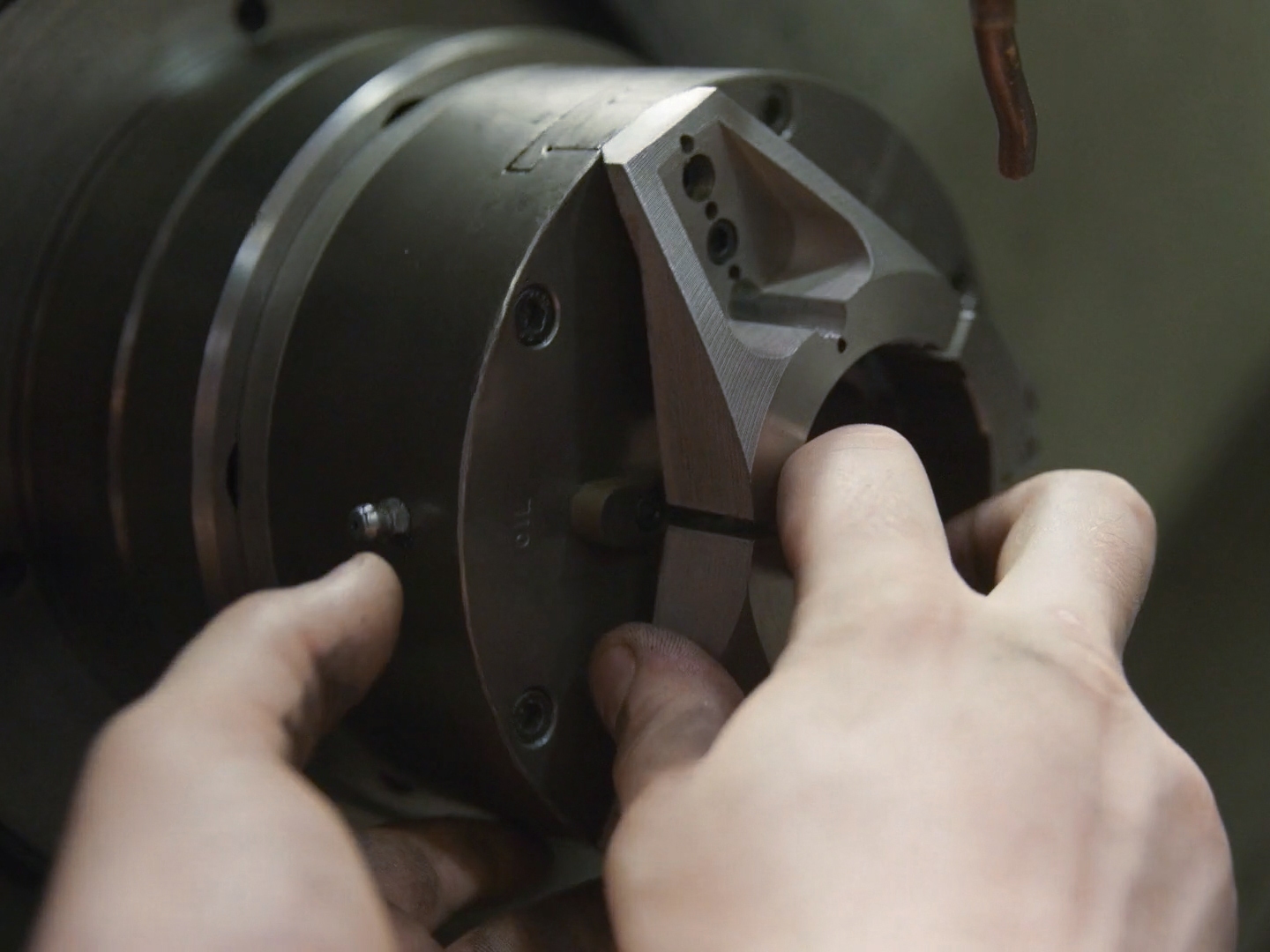
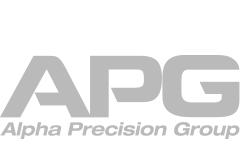
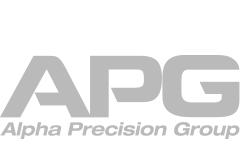
Custom tooling, easier than ever
Using the Studio System, APG engineers are able to significantly reduce the lead time and cost to produce custom jigs, fixtures and tooling. The result is faster transitions from finished design to production and less down time for manufacturing lines.
Custom tooling creation
Using Desktop Metal products, the world’s top tool-makers are able to quickly produce custom tools - shortening the lead time and cost for end-use parts and reducing manufacturing down time.
Part Gallery
3D printing is an ideal solution for a wide range of tooling applications - including custom jigs and fixtures, complex injection mold inserts, extrusion dies, stamping tools, and more.
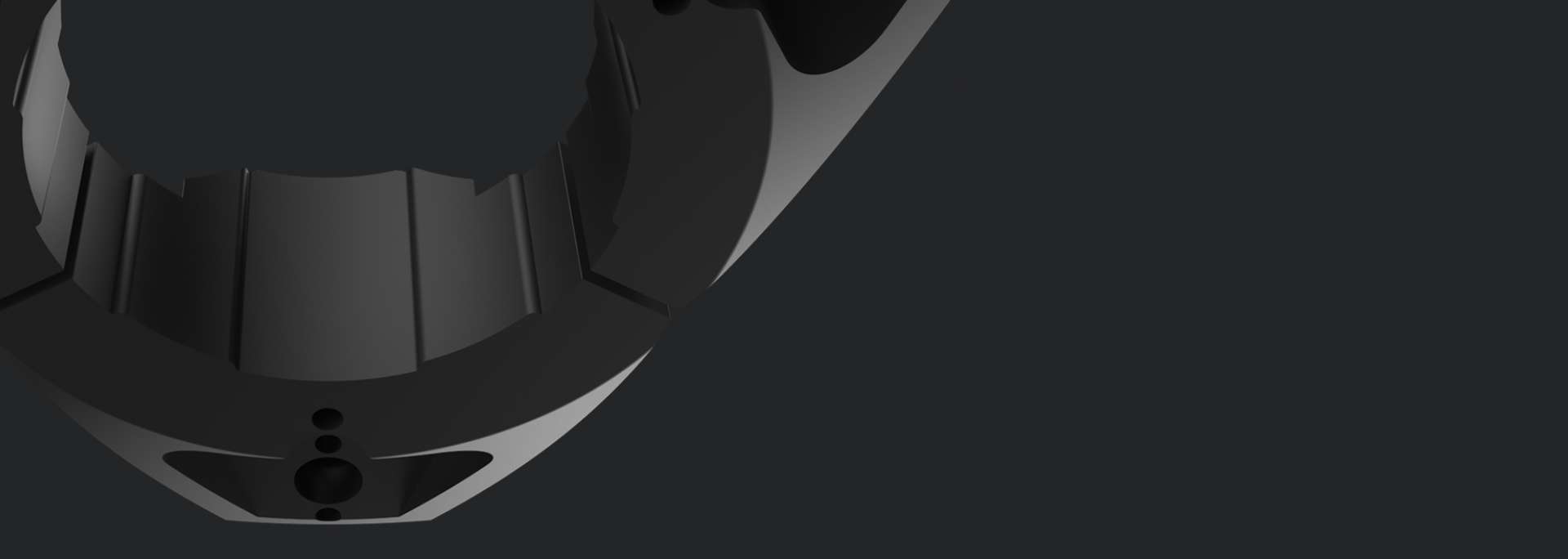